

CNC cylindrical grinding operations can be categorized into three main types: centerless grinding, pinch/peel grinding (including form and non-round shapes), and cylindrical grinding encompassing plunge, outer diameter (O.D.) or external, and inner diameter (I.D.) or internal grinding.
In centerless grinding, the workpiece is supported on a blade-like support, rotates through contact with a regulating wheel, and is ground by a grinding wheel. This technique enables the grinding of long (and sometimes thin) parts without needing steady rests and helps minimize taper issues caused by deflection. Three primary variations of centerless grinding include:
Through-feed grinding, where the grinding wheel is angled relative to the other two axes to enable horizontal feeding of the workpiece.
In-feed grinding, where the part is fed radially into the grinding wheel in one motion perpendicular to the part. The grinding wheel can be dressed to match the specific profile the part needs.
End-feed grinding, where the part is axially fed into the machine for grinding. Once grinding is complete, the part is moved in the opposite direction to exit the machine.
Peel grinding removes the entire stock in a single grinding pass. The key requirement is using a method minimizing heat generation on the workpiece surface. This process resembles longitudinal form grinding with a narrow wheel following a specific path, similar to turning.
Grinding wheels featuring single-point contact typically are low-wear superabrasive wheels operating at higher-than-usual RPM. A single-point contact reduces the interaction zone between the abrasive wheel and the workpiece, minimizing heat generation.
An advancement in peel grinding is the technique known as pinch grinding, where a rotating blank moves between two opposing grinding wheels. The workpiece is pinched between a roughing wheel and a finishing wheel having significantly different grit sizes. The finishing wheel trails the roughing wheel at a very slight axial and radial distance.
The patented pinch/peel approach for non-round grinding is used in precision-shaping form punches of all shapes, pill (tablet) punches, and other non-round parts.
Cylindrical and plunge grinding involve fixturing the part on a spindle axis during grinding. This can be accomplished with or without using a tailstock.
External cylindrical grinding is where the grinding wheel traverses the axis of the workpiece, primarily axially, but also radially. Typically, the grinding wheel’s entire width is in contact with the workpiece.
Internal cylindrical grinding inserts an abrasive wheel, smaller than the internal hole to be ground, into the component’s center. The grinding spindle’s RPM must be high to achieve adequate surface speed on the relatively small wheel.
In plunge grinding the grinding wheel is pre-shaped to match the required profile of the component and then moved radially into the workpiece.
MyGrinding Inc.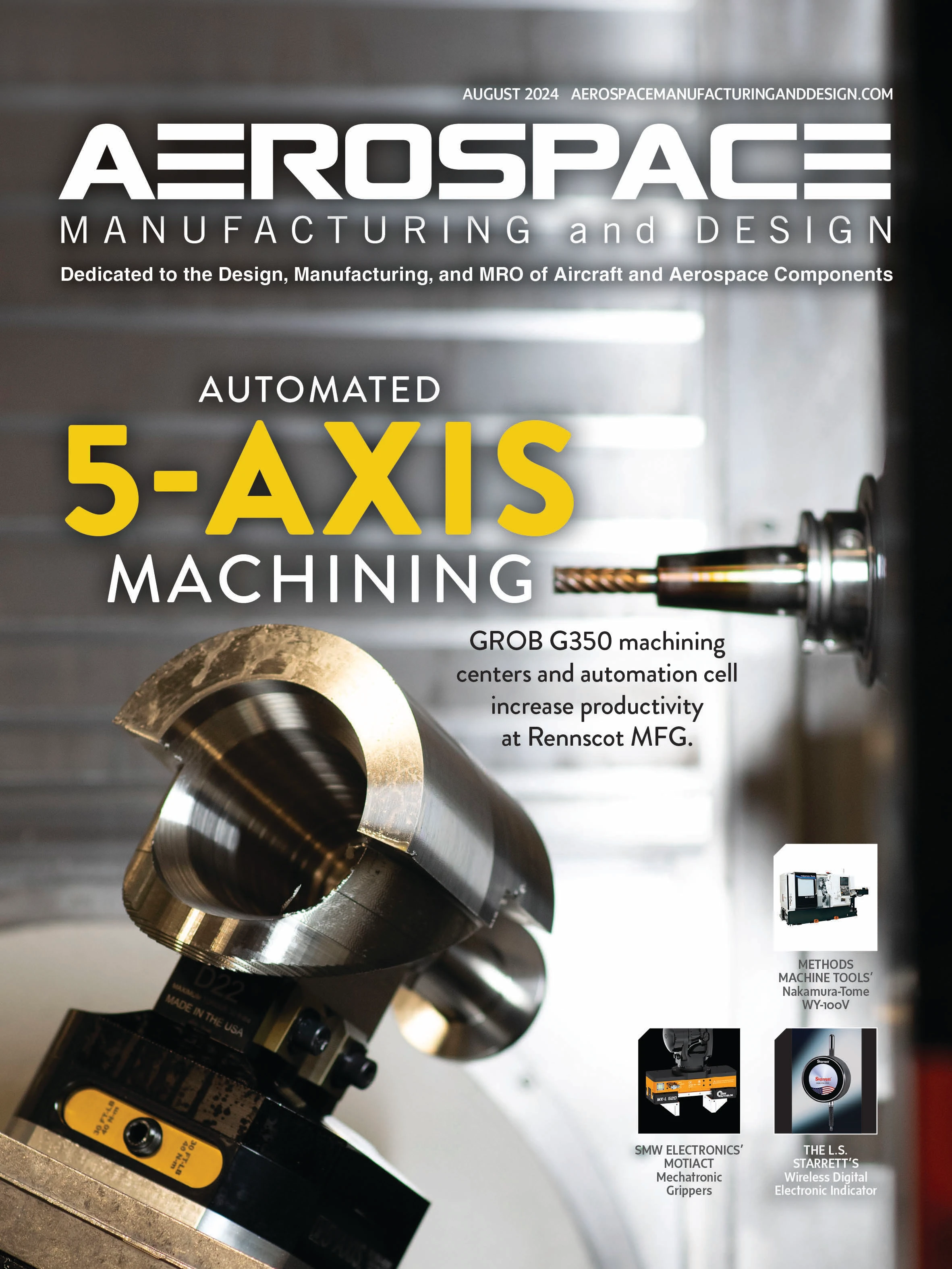
Explore the August 2024 Issue
Check out more from this issue and find your next story to read.
Latest from Aerospace Manufacturing and Design
- Talking machine tools with the professionals who build them
- Tools and strategies for improving your machining processes
- America Makes announces QTIME project call
- Innovation meets precision for 40% faster machining
- Upcoming webinar: Pro tips from a supply chain strategist
- Heart Aerospace relocates to Los Angeles
- Fixtureworks introduces Stablelock Clamps
- Piasecki acquires Kaman's KARGO UAV program