
Speed, power, and precision are coveted qualities to Justin and Maryann Schaller, both in terms of the Schaller Group family-owned business and in their other shared passion of hydroplane racing (see sidebar below). The brother and sister duo hold executive positions with Schaller Group, a third-generation, Michigan-based precision metal forming and assembly company that manufactures parts for aerospace, military, automotive, and medical industries.
For 10 years, the Schaller siblings ran their own CNC machining company, but in 2018 opted to bring their expertise back into the family-owned stamping business. The company expanded one of its plants to 90,000ft2. Designated for CNC machining, it is one of six specialized manufacturing plants operated by the Schaller Group in the Detroit, Michigan area.

Ideal for complex aluminum workpieces
The STC 800X is ideally suited for machining complex aluminum. Capable of continuous 5-axis milling using a rotary table and 120kW tilting spindle (S1), Schaller can machine with up to 162hp and 30,000rpm. With the -100°/+60° A-axis range, no angle heads are necessary for machining aerostructures. The rotary table allows economical machining by using a tombstone setup or multiple parts and fixtures on the same table. Additionally, the STC at Schaller has been integrated into a manufacturing system, allowing flexibility.
“This is the perfect machine for our growth plans,” says Business Development Specialist Maryann Schaller. “We recently poured the foundation to add a second STC 800X to our operation, and because we purchased a flexible manufacturing system (FMS) with the first STC 800X, we can have multiple machines in a single manufacturing line.”
One example of new opportunities is medical devices. In March 2020, the Schaller Group manufactured and donated parts for a prototype ventilator project at a university in the hope of helping with the COVID-19 crisis. Although that project didn’t take off as hoped, it showed Schaller another market where the Starrag STC 800X will be greatly beneficial.
“The speed and accuracy of these machines were big reasons why we chose Starrag,” Maryann says.

Buyer’s journey was seamless
Schaller Group Chief Technologist Justin Schaller says the customer journey from research to demonstration, purchase, and installation was seamless. “I don’t even feel like a customer of Starrag. We have a relationship that’s really more like a partnership.”
That partnership was formed at the International Manufacturing Technology Show (IMTS) where Justin was introduced to Starrag products.
“When the right project came along in 2020, it provided us the opportunity to purchase the Starrag STC 800X,” Justin says.
After the foundation was poured, installation was completed in September 2020. However, the project was put on hold because the additive manufacturing (AM) customer converted its manufacturing to produce testing swabs for healthcare professionals to use during the pandemic. The customer is now re-engaged with Schaller Group to fulfill the original project.
Range of markets
Precision, quality, total cost of ownership, and guaranteed 95% uptime are all advantages of Starrag machines. Schaller selected Starrag because the equipment can be used in a wide array of industries – not just aerospace. Other markets that require high precision, complex parts include various racing vehicles, satellites, or electrical vehicles (EVs).
Tim Mooney, Starrag North America sales director says, “The STC 800X is ideal for machining 55" or smaller precision parts, which is what Schaller needs for the complex aerospace, defense, and specialty industry markets it’s expanding into. Having machines that are highly reliable and able to manufacture the most challenging parts consistently are part of the Starrag guarantee. That’s really what drives business, because manufacturers want their machines running 24-7 without the need for constant intervention.”
With the anticipated growth and diversification, “we’ll be putting in a couple of more Starrag machines,” Maryann says. “To us, Starrag and automation make sense.”
Diversify into high performance racing
Get curated news on YOUR industry.
Enter your email to receive our newsletters.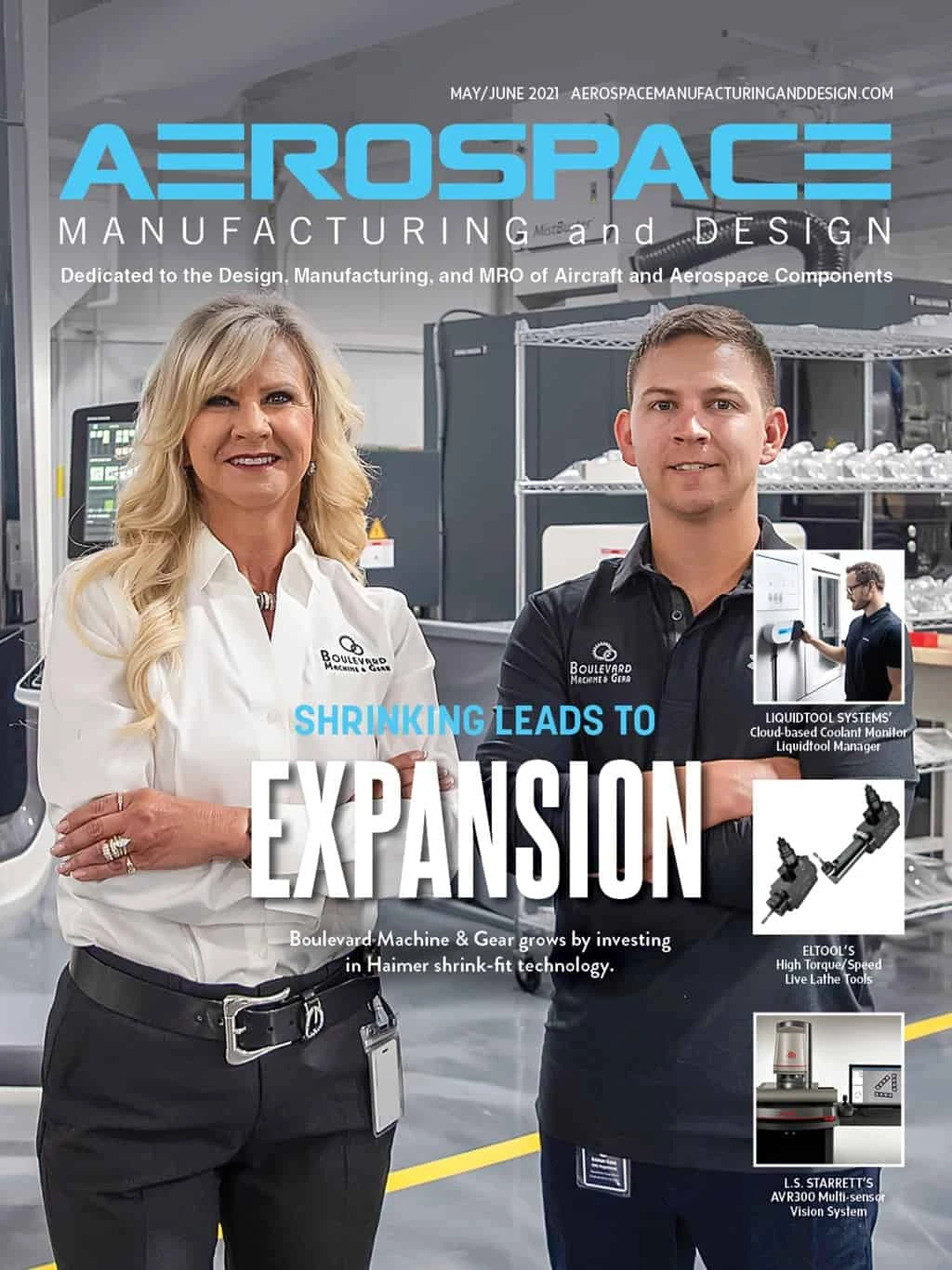
Explore the May June 2021 Issue
Check out more from this issue and find your next story to read.
Latest from Aerospace Manufacturing and Design
- Aerospace Industry Outlook - Spring 2025, presented by Richard Aboulafia
- Panama’s National Air and Naval Service selects Embraer Super Tucano
- Model 5770 Linear Abraser
- #42 Lunch + Learn Podcast - Quell Corp
- RECARO Aircraft Seating showcases advanced comfort solutions at AIX 2025
- Mitutoyo America’s MiSTAR 575 Shop Floor CNC CMM
- Korean Air finalizes Boeing widebody order
- Walter introduces a performance copy milling grade