

After decades of continued growth supplying ultra-precision aerospace components, C&S Machine Products Inc. recently consolidated three disparate operations into a new, state-of-the-art 122,000ft2 facility in Niles, Michigan, about 90 miles east of Chicago.
About 100 employees use more than 100 advanced machines to perform CNC turning, 5-axis milling, grinding, electrical discharge machining (EDM), and Swiss multi-axis turning to machine small, difficult, ultra-precision parts. The shop holds grinding tolerances within 0.00005", and such tight tolerance parts have become the shop’s niche and competitive advantage. Associated operations include honing, lapping, additive manufacturing (AM), laser marking, assembly, testing, and cleaning.
Serving aerospace manufacturers since the 1980s, C&S supplies critical aerospace assemblies including hydraulic spool and sleeve valves, and the shop’s components are on nearly every military and commercial airplane platform active today. Typical workpiece materials are hardened 440C and 52100 aerospace steels and nitriding steels, in addition to nickel-base alloys and titanium commonly used in aerospace.
“The parts generally are small enough to be held in one hand,” says C&S President Dominick Saratore. “And we can often ship 20 to 40 pieces in one small box. We’ll make any part for any customer that needs our kind of tight tolerance capabilities, but aerospace is our bread and butter.”
Precision grinding
Within C&S’s lean manufacturing part processes, high-precision Studer CNC grinders from United Grinding expedite production and reinforce quality.
“United Grinding is our go-to grinding machine tool source that offers real depth in capabilities,” Saratore says. “There are a lot of grinding machines out there that just don’t have the same consistent quality, service, parts, or training. We use our Studers for cylindrical grinding. But we are also looking at other projects in the future, using different capabilities.”
The shop installed a Studer favorit machine a year ago, another a few months ago, and has a third on order.
“We are always setting up and changing over to run part families,” Saratore says. “We get the luxury of running the same jobs over and over, but we don’t do it in large volumes and don’t get to set up and run something for a month. Typically we will set up a job and run it for the day, and the next day we are running something else.”
Some of the company’s customers specify part dimensions as well as grinding processes to avoid putting stress on a part that could later crack.
“Our customers are very specific in what they want,” Saratore says. “Not only do we have to produce to the print, we also have to meet their processing requirements.”
The shop has a catalog of about 500 high-accuracy part numbers. “To be able to do that day in and day out for 500 part numbers, you have to have a complete depth in your system and people, and your organization has to be robust,” Saratore says.
Saratore credits the company’s investment in technology, facilities, equipment, and people for its continued growth and success. “Many shops don’t put all of those pieces together, but we do. We produce precision products and have systems in place to control the processes.”
At C&S, putting all the pieces together starts with the facility and equipment.
“Our facility is temperature, humidity, and air quality controlled. Every machine tool that we buy is best in class, and we don’t cut corners on equipment, tooling, fixturing, workholding, business processes and systems, employee training, and so on,” Saratore says.

C&S and United Grinding are similar in that they both provide all the pieces necessary for success.
“There’s not a missing piece. If there are 20 things required to be great, United Grinding and C&S have all 20,” Saratore notes.
C&S Machine plans to keep growing in the sectors it serves. Part of the plan is the recent creation of an advanced manufacturing research and development (R&D) group consisting of a director of advanced manufacturing R&D, an applications engineer, an automation engineer, and a program manager. C&S is currently on pace to add one advanced manufacturing cell per year, but as the shop grows and evolves, the plan is to bring on two to four cells annually. Grinding technology from United Grinding will likely figure into these plans.
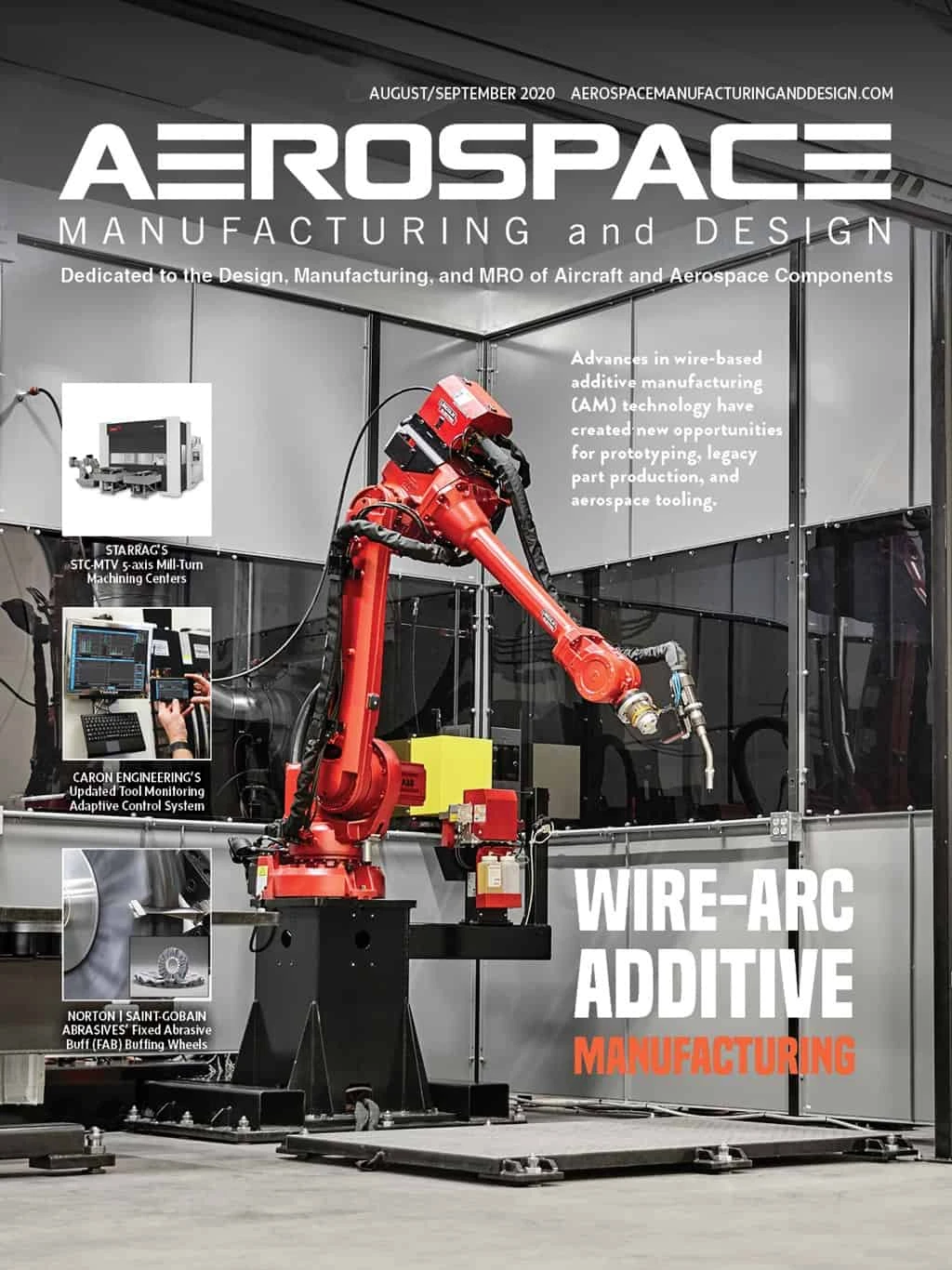
Explore the August September 2020 Issue
Check out more from this issue and find your next story to read.
Latest from Aerospace Manufacturing and Design
- Piasecki acquires Kaman's KARGO UAV program
- PI Americas’ long-travel XY piezo nanopositioners-scanners
- AAMI project call submission deadline extended to May 12
- Jergens launches cast iron tooling column additions
- Airbus to acquire assets relating to its aircraft production from Spirit AeroSystems
- FANUC America's Cobot and Go web tool
- Chicago Innovation Days 2025: Shaping the future of manufacturing
- High-density DC/DC converters for mission-critical applications