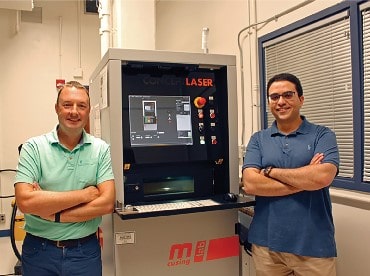
Precision and quality are key in additive manufacturing (AM) when it’s being used to create heat-resistant metal parts for jet engines, rockets, or other high temperature environments. University of Arizona engineers are using machine learning methods and $750,000 in NASA funding to monitor and mitigate defects that occur in AM. Mohammed Shafae and Andrew Wessman are collaborating with Lockheed Martin Space, Open Additive LLC, and CompuTherm LLC.
Different defects, different problems
Two defects occur in AM products:
“You can think how dangerous that would be if the part was used in a jet engine or rocket,” Shafae says. “The types of defects we’re focused on are defects that will make the material behave differently than intended.”
Machine learning is key
Shafae and Wessman use a sophisticated sensor system, combining thermal imaging and high-speed localized cameras, to monitor the 3D printing process and identify when and where defects occur. They apply machine learning methods to the data and develop a model predicting when defects occur so scientists can take corrective action, preventing the defects or terminating a process before wasting time and materials.
“We’re trying to learn how these separate categories of defects can be linked to each other, because sometimes process defects can cause material defects,” Shafae says.
Machine learning (ML) is key: a product is only as strong as its weakest point, and industrial scale AM processes generate several terabytes of data no researcher could sort through. Taking data crunching out of human hands allows for closer analysis of the process.
Augmented intelligence with the fusion of digital, physical, and biological worlds forms the cornerstone of the University of Arizona’s strategic plan combining data processing, process optimization, materials analysis, and ML.
“This is truly an example of what people need to be doing to get to Industry 4.0, the use of data to improve processes, and ensure they’re performing as you want,” Wessman says. “By improving manufacturing process quality, you know you have a good product from the time you take it out of the machine.”
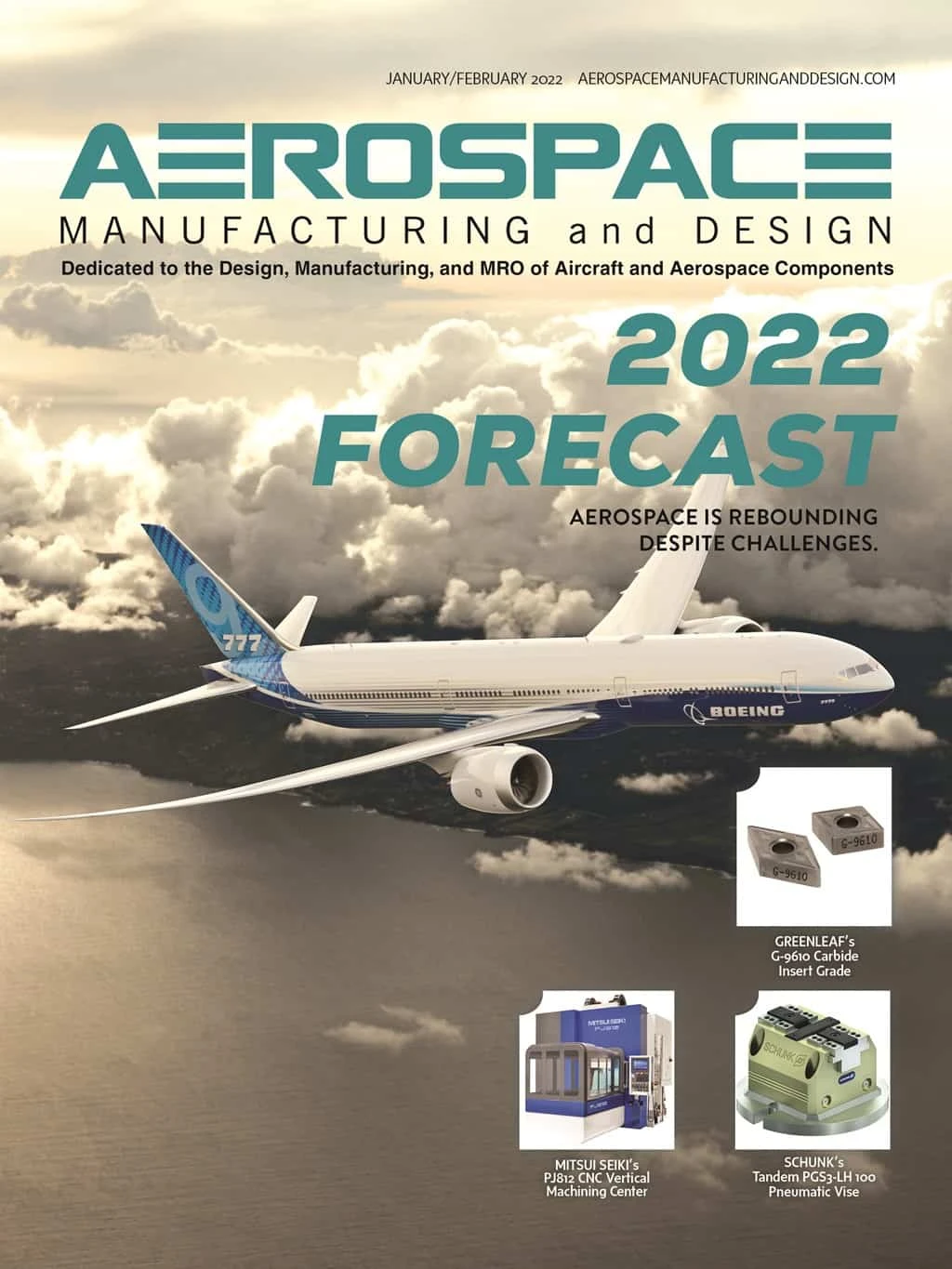
Explore the January February 2022 Issue
Check out more from this issue and find your next story to read.
Latest from Aerospace Manufacturing and Design
- Revitalizing the Defense Maritime Industrial Base with Blue Forge Alliance
- Safran Defense & Space opens US defense HQ
- Two miniature absolute encoders join US Digital’s lineup
- Lockheed Martin completes Orion for Artemis II
- Cylinder CMMs for complex symmetrical workpieces
- University of Oklahoma research fuels UAS development
- Motorized vision measuring system
- Everyone's talking tariffs