
With longstanding relationships with the aerospace, defense, and nuclear power refueling industries spanning more than 70 years, Paul Fabrications Ltd., a Unitech Aerospace company, has expanded its laser processing capabilities by acquiring the large work envelope version of the 6-axis Laserdyne 795XL. The fiber laser incorporates Laserdyne SmartTechniques processing technology for high-speed, high-precision laser cutting, welding, and drilling.
Long-term strategic partnerships
With more than 185 employees operating in a 6,000m2 manufacturing facility in Derby, United Kingdom, the company has been involved in the development of major aero-engine programs for civil and military applications. It has honed strong expertise in the production of value-added complex fabricated and machined components and assemblies resulting in long-term strategic relationships with leading manufacturers such as Rolls-Royce.
Gary Hemmings, Paul Fabrications’ business improvement director calls the 795XL “a fantastic addition to our existing 5-axis CO2 laser technology. In certain applications, it’s 4x faster than technology previously available and gives us the ability to add enhanced features to our customers’ parts. This, along with its welding capabilities, gives us a competitive advantage on a variety of different products including transition ducts, silencers/attenuators, and combustor chambers for land and aero turbines.”
The system offers high-speed, high-precision percussion and trepan drilling, cutting, and welding technology.
“Our customers have a broad range of requirements, from a single complex assembly to an entire program of parts needed within short lead times, manufactured over many months with multiple releases,” Hemmings says.
To handle these needs efficiently, manufacturing capabilities include the Laserdyne 795XL, QVI/OGP vision inspection, a Mazak Variaxis i-800 mill-turn center, Doosan Machine Tools’ Puma VTL and turn-mill centers, other existing 3-, 4-, and 5-axis CNC milling and turning machines, and more than 40 different processes to deliver engine-ready assemblies.
“This includes managing an assembly’s exacting purchasing and production requirements from beginning to end. A recent example is a strategic partnership with Rolls-Royce to provide a turnkey new product introduction process,” Hemmings notes.
Mark Barry, vice president of sales for Prima Power Laserdyne adds, “The 795XL, outfitted with a 15kW QCW fiber laser, adds capacity for complex laser hole drilling at angles as shallow as 10° to the surface in uncoated and thermal-barrier- coated

Programming design support
“We’re operating the system for trepanning using continuous wave and peak power pulsing,” reports Sean Ahern, CAD/CAM laser engineer for Paul Fabrications. “We are laser processing silencers and liner assemblies made from nickel alloy C263 and C625. These materials have exceptional fabrication characteristics with excellent intermediate temperature tensile ductility and high strength. The Laserdyne system allows us to easily achieve a tolerance range from 0.30mm down to 0.05mm on part features including inner and outer profiles and hole sizes of 0.6mm, 0.9mm, 1.5mm, and 26.0mm. Laserdyne’s ongoing support has also allowed us to move quickly to expand on these capabilities with the system.”
Processing accuracy
For Paul Fabrications, achieving a high level of accuracy from prototype to production stages and from one job to another is possible because of the Laserdyne design that integrates all system features. Everything works in a coordinated manner – controller, software, motion system, laser, and process sensors. Laserdyne’s software and hardware for part mapping and focus control enhance quality and cycle times compared to traditional production methods.
Among these are the S94P control, which includes dedicated hardware and software features including automatic focus control (AFC) for capacitive part sensing, optical focus control (OFC) for sensing of non-metallic or thermal barrier coated surfaces, ShapeSoft software for programming shaped holes, and multi-buffer capable mapping of part surfaces.

The focus control feature is particularly important to Paul Fabrication’s work. OFC/AFC precisely guides the motion system, maintaining critical focus position and following the contour of the part regardless of slight surface irregularities. OFC/AFC allows top machine speeds, maximizing productivity without downtime or scrapped parts.
The Laserdyne fiber laser system operates at up to 800ipm (0m/min to 20m/min) in all axes with bidirectional accuracy of 0.0005" (12.7µm). This accuracy is throughout the system’s 80" x 40" x 40" (2.0m x 1.0m x 1.0m) work envelope, for reliable and consistent processing of small, medium, and large parts.
After only a few months of use, Paul Fabrications’ overall appraisal of the Laserdyne 795XL fiber laser quality is quite high.
“The trepan quality is excellent with very little exit burr, or as laser processing engineers prefer to say, dross. Our operators like operating the system. Maintenance of the new fiber laser system hasn’t been an issue,” Ahern says.
Paul Fabrications Ltd. Prima Power Laserdyne LLCGet curated news on YOUR industry.
Enter your email to receive our newsletters.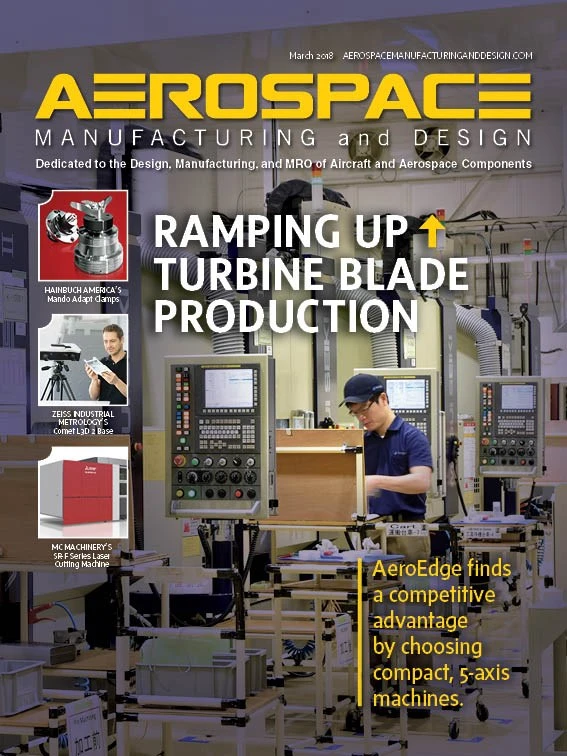
Explore the March 2018 Issue
Check out more from this issue and find your next story to read.
Latest from Aerospace Manufacturing and Design
- Revitalizing the Defense Maritime Industrial Base with Blue Forge Alliance
- Safran Defense & Space opens US defense HQ
- Two miniature absolute encoders join US Digital’s lineup
- Lockheed Martin completes Orion for Artemis II
- Cylinder CMMs for complex symmetrical workpieces
- University of Oklahoma research fuels UAS development
- Motorized vision measuring system
- Everyone's talking tariffs