
Technology is great – until it isn’t. In aerospace companies, the usual fate of no-longer-great technology – especially software – is rip-and-replace, out with the old, in with the new. It’s everything top management wants to hear: decisive, intuitive, cost-effective, one-and-done.
Unfortunately, rip-and-replace never works that way, in aerospace companies or in any other large complicated enterprise. Aerospace arguably has developed, bought, used, customized, and retired more technology than all other industries combined – and retired almost always means completely ripping out old solutions and replacing them.
The costs can quickly climb into the millions of dollars, months of additional effort in information technology (IT) and engineering, and potential loss of data that users need to do their jobs. Loss of data is usually a hidden cost, undiscovered until the data is needed. In aerospace, the consequences of both can be particularly severe; deadlines get missed and sanctions may be imposed.

The rip-and-replace problem can be severe in product lifecycle management (PLM). CIMdata formed its Aerospace and Defense (A&D) PLM Action Group, in part, to address this obsolescence issue. Comprised of thought leaders and operations executives, the group is sponsoring PLM-related research to better understand the issues and guide solution providers and standards bodies.
Action Group members are Airbus, Boeing, Embraer, Gulfstream, and Rolls-Royce. Membership is open to commercial aircraft original equipment manufacturers (OEMs), defense OEMs (aeronautics and space sectors only), and aircraft engine providers. Much of this article is derived from the Action Group’s sponsored research project launched in 2014.
The challenges
PLM implementations embody over-arching technology strategies and provide an infrastructure to manage product-related data. PLM helps diverse teams collaborate, getting wildly dissimilar solutions to work together (interoperate), and monitors all of these processes.
The ideal is a sustainable PLM solution that can be implemented and updated at reasonable cost with minimal disruption. A sustainable PLM must meet evolving business needs and return-on-investment (ROI) requirements within the terms of aerospace contracts; compatibility with industry standards is a plus. A sustainable solution is one in which obsolescence/ retirement can be mitigated or avoided far into the future.

The biggest challenge in sustainability is justifying the cost of the technology upgrade or refresh and then controlling the unanticipated costs of integration, data migration, and customization. These costs are typically underestimated and are not usually built into aerospace budgets, proposals, or contracts. This is why so many aerospace technology transitions are postponed or avoided.
In aerospace contracts, life cycle means years if not decades. During such long stretches of time, obsolescence and retirement is guaranteed for virtually all product-development tools, systems, technologies, and solutions – plus people, skill sets, and workflows.
As both a business strategy and an engineering technology, the PLM infrastructure reaches deeply into the details of developing new products, maintaining control of intellectual property spanning the enterprise.
Long, complex life cycles make sustainability essential in PLM strategies. Until recently, however, little attention was focused on sustainability. An inescapable truth being recognized is that PLM and all the other computerized solutions are not by themselves sustainable. Just like the products developed, strategies and solutions also become obsolete.
The benefits of PLM are well documented and some common ones are shown in the table below. By addressing PLM’s own lifecycle cost, ROIs can be dramatically improved by reducing rip-and-replace expenses.
Retiring rip-and-replace
Rip-and-replace has always been a bad idea. At first glance, it sounds good – out with old, clunky, cumbersome, costly, slow, and frustrating. Multiple, new solutions smoothly integrated improve business performance and everyone’s happy.
But what actually happens? The old solutions cannot be completely ripped out. They reach too far and too deep, so parts of them keep operating as legacy systems. Legacies aren’t all bad if they can be integrated effectively, but that rarely happens.
Aerospace rip-and-replace horror stories include:
- Old and new solutions differ in their data structures, data access interfaces, and standards and protocols they support. Even if integration is available out-of-the-box, some customization is needed. Work bogs down and additional resources are required.
- Integration projects may deal with multiple generations of solutions running simultaneously. One company has product definition data spread across mainframes, minicomputers, product data management (PDM) solutions, desktops, and is now studying mobile devices. Scattered standards, data structures, protocols, and application programming interfaces go back for decades. They make even minor upgrades costlier, slower, and riskier.
- Integrating legacy and new solutions can cost hundreds of thousands of dollars in medium-sized aerospace suppliers and tens of millions in the primes, even hundreds of millions. It is possible to implement a sustainable solution in an unsustainable way, replacing one unsustainable legacy with another.
- Poor alignment of new and legacy solutions with existing processes can lead to more connections and more maintenance. A common euphemism is parallel solutions, several systems that need to be accessed to perform a single task. Identical data may be entered manually into several partially redundant solutions, adding opportunity for error and confusion.
- Tactical upgrades, another euphemism, meaning upgrades without executive buy-in, sign-offs, or upfront funding. Typically, these upgrades understate costs, efforts, and risks while over-promising benefits and go-live dates. Worst case, funds are cut off.
A sustainable PLM solution requires a modular architecture, one that supports minimal cost, low IT effort, and no loss of data transitioning throughout the life of the underlying contract or program.
Lost data costs

Data loss is rarely discovered until someone searching for the information comes up empty handed.
Data that goes missing. This is a well-known risk in solution migrations, and aerospace contracts stipulate that any lost data must be recreated. For example, new drawings must be verified by comparing the new image and information with the original in CAD and CAE files, solid models, and in technical data packages such as product manufacturing information (PMI), and geometric dimensioning and tolerancing (GD&T).
Regenerating drawings is tedious, labor-intensive, carries a large opportunity to introduce new errors, and often eludes automation. Moreover, the regeneration of drawings is done without compensation in fixed-price aerospace contracts.
Data that is stranded. When data moves to different hardware, formats, product design software, PLM, and PDM solutions, knowledge gained in previous contracts and programs can be locked in obsolete, legacy systems. Users often struggle to remember where the data was and how to retrieve it. In IT, this is known as eating the learning curve.
The architectures, workflows, data formats, and best practices of many older PLM solutions were developed in the early 1990s for vertically integrated aerospace OEM enterprises. With so much design and production outsourced, those solutions do not meet today’s demands for collaboration and interoperability needed to support global outsourcing.
The goal of PLM obsolescence management is to provide aerospace companies with the ability to incrementally and continuously upgrade and transition PLM solutions. This means transforming data to accommodate new technologies, spanning several decades without loss of data or incurring excessive cost and effort in diversion of scarce technical resources. Data must be transformed, as well, when one solution provider’s new features and functions leapfrog older PLM implementations.
CIMdata Inc.
About the author: Tom Gill is practice manager for PLM enterprise value and integration at CIMdata Inc. He can be reached at 603.651.7496 or t.gill@cimdata.com.
Get curated news on YOUR industry.
Enter your email to receive our newsletters.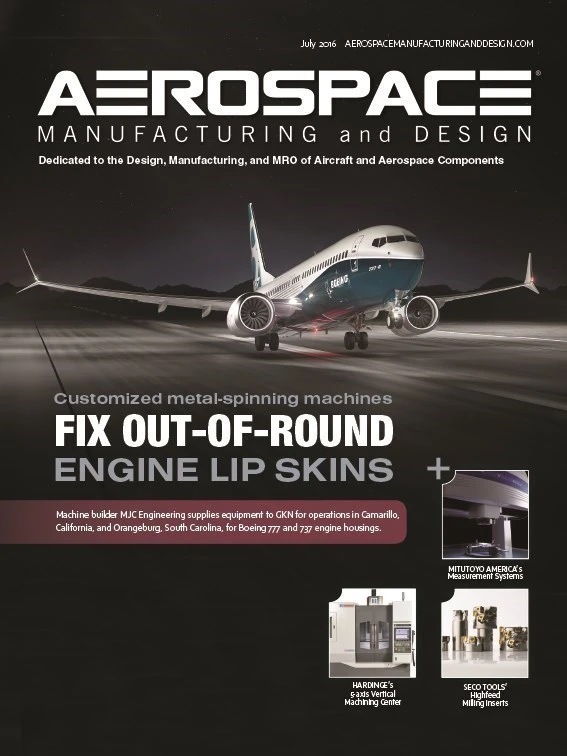
Explore the July 2016 Issue
Check out more from this issue and find your next story to read.
Latest from Aerospace Manufacturing and Design
- GE Aerospace awarded subcontract for FLRAA next phase
- KYOCERA Precision Tools publishes 2025-2026 Indexable Cutting Tools Catalog
- BOC Aviation orders 120 Airbus, Boeing jetliners
- Mazak’s INTEGREX j-Series NEO
- Embraer tests wing for new technologies demonstrator
- Mitutoyo America’s SJ-220 portable surface roughness tester
- #55 - Manufacturing Matters - A Primer on Defense Contract Manufacturing
- Registration is open for April’s Manufacturing Lunch + Learn!