
With 2.2 million parts, seating for up to 330 passengers, a maximum range of 7,600nm, and a top speed of Mach 0.90, more than 600 Boeing 787 aircraft are in service worldwide.
The aircraft’s complicated electronic systems communicate through a maze of cables, so each 787 carries thousands of connectors. It was the first commercial aircraft to adopt rectangular, composite cable connectors throughout the entire airplane. Others use them in cockpit electronics, but the 787 completely ditched traditional round, metal connectors.
Boeing made sweeping changes to the connectors when it designed the 787, and the rest of the industry is following suit. Circular, metal-housed connectors are being replaced with rectangular, composite ones for weight reduction, space efficiency, and modular capabilities.
Weight reduction
When Boeing was developing the 787, the first plane reportedly was 5,000 lb heavier than specified, prompting designers to reevaluate many parts. Weight concerns partly drove the decision to deploy composite materials – making the 787 the first major commercial plane with a composite fuselage, wings, and frame components.
While the difference in weight between a round metal connector and a rectangular composite connector is barely noticeable, the difference between thousands of such connectors adds up. One study concludes a fleet of composite planes could reduce carbon emissions by up to 15%. Conversely, lighter planes can carry more cargo, potentially reducing the number of flights required and costs to airlines and air transportation companies.
Space optimization
When bakers cut sheets of cookie dough with a circular cookie cutter, lots of dough between the circles remains. Imagine instead cutting the dough
Traditionally, panels of round cable input jacks accept the cables. The panel layout is like that first cookie sheet – lots of wasted space around the circular-shaped jacks. Rectangular connectors reshape those panels, allowing designers to squeeze more cables into the same space or reduce the size of the panel while still accommodating the same number of inputs.
Modularity
Automobile manufacturers use the same parts in many car models. Equipment standardization can streamline the supply chain and improve product quality, principles applicable to airplane manufacturing. However, platform flexibility doesn’t exist with round metal connectors, which have an insert glued into them that can’t be changed. A specific connector is required for a specific application.
Rectangular connectors are made of multiple pieces that can be mixed and matched to tailor the connector to a given application. To ensure safety, connectors are keyed so only the correct connector can go into each dock. Rectangular connectors are also fiber-ready, while circular connectors generally are not.

What’s next?
The Bombardier C Series aircraft has transitioned to rectangular connectors, and Gulfstream has used some rectangular connectors. Boeing’s recently announced new mid-sized aircraft (NMA) replacement for the 757 may use rectangular connectors, as well.
Cinch Connectivity Solutions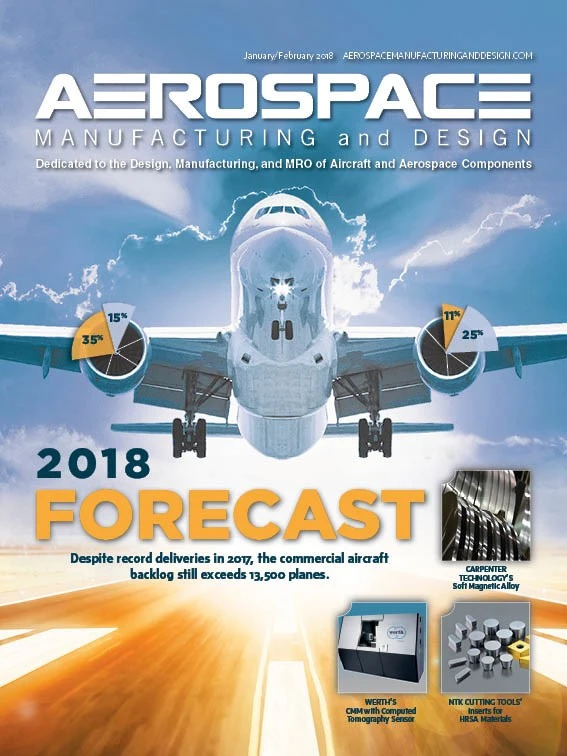
Explore the January February 2018 Issue
Check out more from this issue and find your next story to read.
Latest from Aerospace Manufacturing and Design
- Textron Aviation to bring its largest-ever lineup to 2025 EAA AirVenture
- Qualified materials for 3D-printing mission-critical applications
- #69 Manufacturing Matters - Shopfloor Connectivity Roundtable with Renishaw and SMW Autoblok
- Demystifying Controlled Unclassified Information (CUI)
- Simplify your shop floor operations while ensuring quality parts
- Happy Independence Day - July 4th
- Bombardier receives firm order for 50 Challenger, Global jets
- Automatic miter bandsaw