One common thread runs through every corner of the aerospace industry – precision is paramount. From initial manufacture to operation, there’s no room for error in creating and leveraging aerospace technologies.
The goal of any aerospace manufacturing operation is to increase shop-floor efficiency and safety while adhering to this elevated level of quality and precision. Artificial intelligence (AI)-powered tools help achieve that vision, but vetting, applying, and using automation solutions can be a challenging prospect.
Automated measurement technologies and consistent end-to-end manufacturing are critical for success and prevention of expensive accidents. Every tool must meet stringent standards for quality, repeatability, safety and, most importantly, mission-critical results.
Fortunately, solutions are being innovated that meet those expectations.

Overcoming unique challenges
Aircraft and other aerospace equipment are marvels of engineering, and automation helps produce these assets efficiently. However, where there are can’t-fail components, there are can’t-fail operations.
Aerospace automation needs to address unique challenges associated with size and scale of aircraft; make investment worthwhile for complex, low-volume processes; and work effectively with materials and equipment often unique to the industry.
However, when accomplished, automation can bring aerospace measurable benefits in efficiency, safety, quality control, and brand elevation and protection.
Let’s explore a key example.
Painting aircraft is typically conducted by skilled artisans who must work efficiently without sacrificing quality. This means moving up and down the aircraft quickly and getting very close to it – but never colliding as such a mistake has extremely costly implications. Therefore, a collision avoidance system is necessary – but traditional options present limitations, such as coarse 3D visualization that restricts platform movement and downtime to update the system when new airplane models enter production.
Although the collision avoidance system might have prevented some disastrous mistakes, it was also causing significant waste of time and efficiency lost while in use.
Collision avoidance solutions in other use cases also exhibit limitations.
When professionals are teaching a robot a path during a guided production mode, they may fail to realize they’re about to make one tiny misstep that sends the machine crashing into the part. When automation solutions are first installed, it may be difficult to realize they’ll eventually crash into one another based on that installation – until it’s too late.
Accidents are going to happen. Aerospace manufacturing operations need to ensure they don’t waste dollars.

Elevating collision avoidance
OnGuard Collision Avoidance is a better way to protect critical assets and ensure mistakes, while inevitable, aren’t costly ones.
As a collision avoidance software, it allows a machine to be operated without fear of a collision between the machine and the asset it’s working on or other machines, because the solution leverages a variety of existing, proven technologies to build an efficient and reliable automated collision-avoidance system.
OnGuard marries software developed at the University of North Carolina called the Proximity Query Package with Open Graphics Library and clients’ design software, building precise visual representations of situations at any given moment and engaging in complex decision-making to avoid collisions.
For aircraft painting, the solution empowered one organization to cut the time needed to accommodate a new plane design by 50% and to view aircraft on a computer screen in real time. It also allowed the painters to move their platforms more freely.
In all applications, OnGuard uses real-time monitoring of machine positions, using that information to issue immediate stop commands should a collision occur.
A simulation mode also allows operations to simulate jobs exactly as they’ll occur in the real manufacturing environment, cutting off potential collisions before they happen and addressing challenges before the machine runs.
With innovative design and powerful use of robotic vision, AI, simulation capabilities, 3D modeling, and advanced warning and controls, OnGuard Collision Avoidance prevents aerospace manufacturers’ most costly mistakes before they happen.
Lightweight robotic tool changer

The durable, lightweight QC-7 robotic tool changer offers various configuration choices with ATI’s pass-through utility modules and tool stand systems. An optional ML12 electrical module attaches easily to the tool changer, which also includes five pass-through air ports and lock/unlock air fittings.
Featuring a low stack height, the tool changer mounts directly to ISO 9409-1-31.5-4-M5 robot wrists.
Integrated with lock/unlock sensors that don’t require an additional interface, the system’s no-touch locking technology and fail-safe locking mechanism secure connection between the master and tool. The device can handle payloads up to 35 lb (16kg) and is compatible with an array of industrial and collaborative robot models.

Mountable motion control drives
ION/CME N-series digital drives provide high-performance motion control, network connectivity, and amplification. The compact, PCB-mountable motion controllers feature a patented, ultra-rugged PCB-mountable package with three power output levels: 75W, 300W, and 1,000W.
Each drive supports brushless DC, DC brush, and step motors. ION/CME N-series digital drives provide profile generation, servo compensation, stall detection, field-oriented control (FOC), electronic camming, and many other motion control functions. They also include support for Ethernet, CAN, serial, and SPI communications.
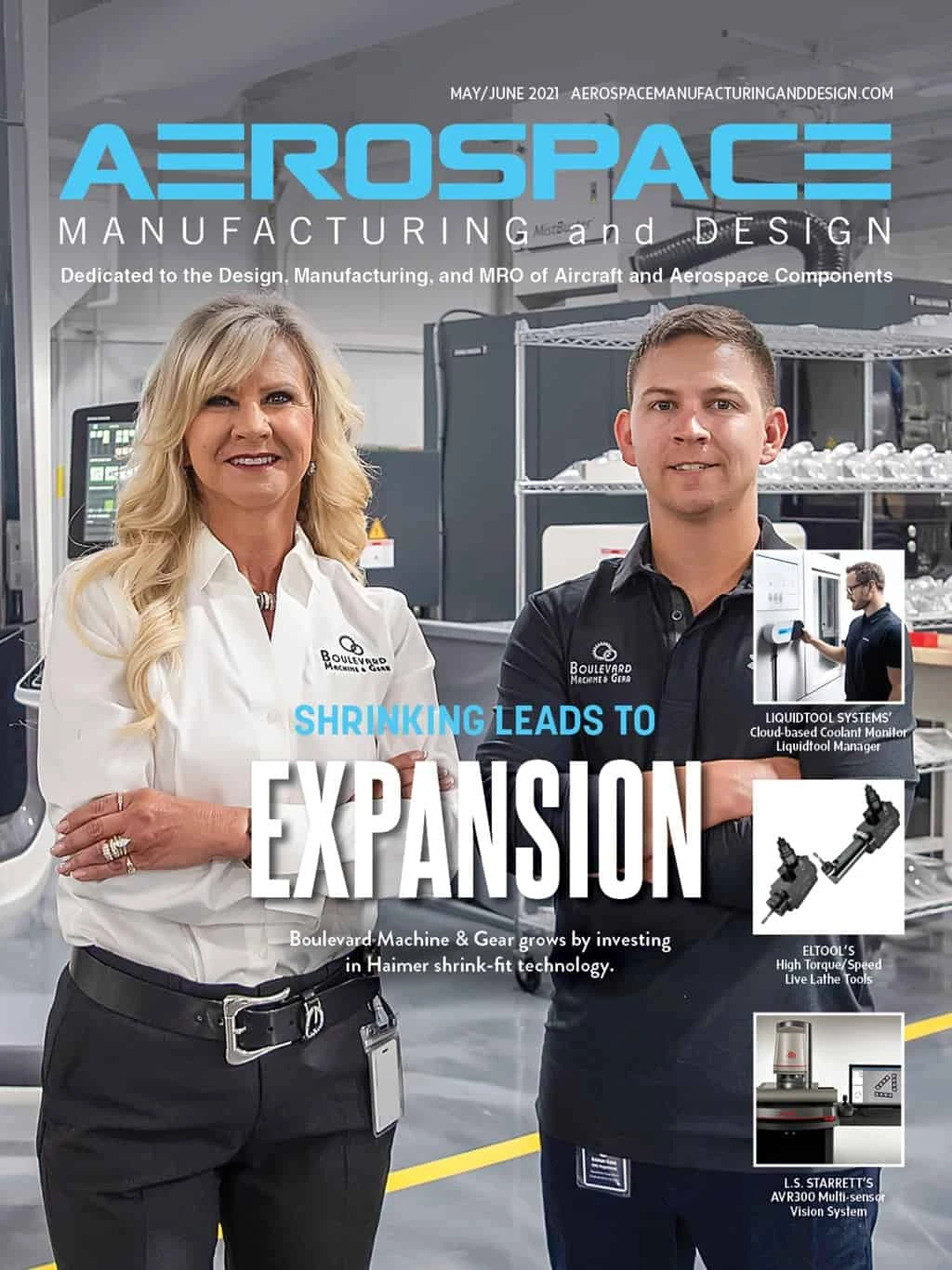
Explore the May June 2021 Issue
Check out more from this issue and find your next story to read.
Latest from Aerospace Manufacturing and Design
- Heart Aerospace relocates to Los Angeles
- Fixtureworks introduces Stablelock Clamps
- Piasecki acquires Kaman's KARGO UAV program
- PI Americas’ long-travel XY piezo nanopositioners-scanners
- AAMI project call submission deadline extended to May 12
- Jergens launches cast iron tooling column additions
- Airbus to acquire assets relating to its aircraft production from Spirit AeroSystems
- FANUC America's Cobot and Go web tool