
Part performance is critical, especially in the aerospace industry, where standards are exceptionally high. High-stress, corrosive conditions, long-term use of parts, and the requirement to produce parts to industry standards make manufacturing aerospace components challenging.
Adopting electropolishing in research and development (R&D) can ensure prototypes pass stringent inspections and testing before moving into production. Most importantly, electropolishing improves part performance and helps aerospace manufacturers meet industry standards.
How electropolishing works
The process converts AC current to low-current DC voltages. Cathode plates made from copper or stainless steel are lowered into the chemical bath and attached to the negative side of the power source. A part or group of parts is then lowered into the chemical bath fixed to a titanium, copper, or bronze rack, which is then fixed to the positive side of the power source.
When current is applied, surface metal ions are removed from the parts and drawn to the cathode while the electrolyte maintains the dissolved metals in the solution. Oxygen gassing occurs at the metal surface, further cleansing the parts. Upon completion, the parts undergo a series of cleaning steps to remove any clinging electrolytes and are then dried.
Electropolishing can be applied to nearly any metal alloy, including stainless steels, copper alloys, nickel alloys, carbon steels, tool steels, aluminum, and titanium.
AMS 2700 aerospace material specifications
Parts used in aerospace applications must be able to perform in harsh conditions, have a long cycle life, and be extremely reliable. In commercial or military aircraft, for example, liquids and gases must flow smoothly through pipes, tubes, and hoses. For fittings, valves, and nozzles that function with metal-to-metal contact, electropolishing creates a smoother surface, free from surface flaws, and extends component life. Unlike mechanical polishing, the electropolishing process creates a uniform, repeatable surface finish, improving the Ra value up to 50%. Strict standards and requirements must be met under ASTM B912 to satisfy aerospace material specification AMS 2700 for passivation. Electropolishing achieves passivation of stainless-steel parts for high levels of corrosion resistance.

Parts requiring dye penetrant testing
Electropolishing resolves surface anomalies on failure-prone parts, such as micro-cracks. Fracture-critical parts that require dye penetrant inspection (DPI) to detect micro-cracks and other potentially dangerous flaws require the part surface to be clean of debris or any substance layer that could camouflage a defect. As a pre-cleaning step, electropolishing exposes the base metal. It enables precise control in removing the outer skin of material, an advantage over other techniques such as chemical etching.
Chemical etching baths without electrical current risk part damage. The heated chemical bath works more aggressively, the removal of material is more difficult to control, and some alloys do not respond well to etching. Parts with very tight tolerances can be irreparably damaged with chemical etching. In contrast, electropolishing can achieve a tolerance of ±0.0002" stock removal and eliminate the peeling and abrading common with a plating or coating and the surface distortion seen with mass finishing. The benefits of implementing electropolishing in prototyping include:
electropolishing improves part performance and helps aerospace manufacturers meet industry standards.’’
- Corrosion resistance: An ultra- smooth surface eliminates initiation sites for part corrosion, aiding long-term part performance. Removing a thin, uniform layer of surface material creates an exterior surface that inhibits corrosion advancement and increases part longevity and integrity. The chromium-rich, passive surface will delay corrosion in various alloys.
- Microfinish improvement: Micro- imperfections and defects, common initiation sites for cracks, are eliminated with electropolishing. Various types of machining, stamping, forming, and welding leave imperfections on the prototype surface. Electropolishing is effective for creating a smooth microfinish on simple or complex geometries and delicate parts.
- Deburring: Parts fit and function as designed, free of friction created by microburrs left by manufacturing. The process improves part integrity by removing a marginal quantity of metal from parts to maintain precise sealing surfaces or other critical part features.
- Ultracleaning: Aerospace parts are free of surface contaminants, debris, and foreign materials.
- Fatigue life improvement: Aerospace parts can achieve a higher level of fatigue life improvement, whether the part was machined or stamped. Electropolishing removes manufacturing defects such as micro-cracks, pits, and other surface anomalies that can lead to premature part failure.
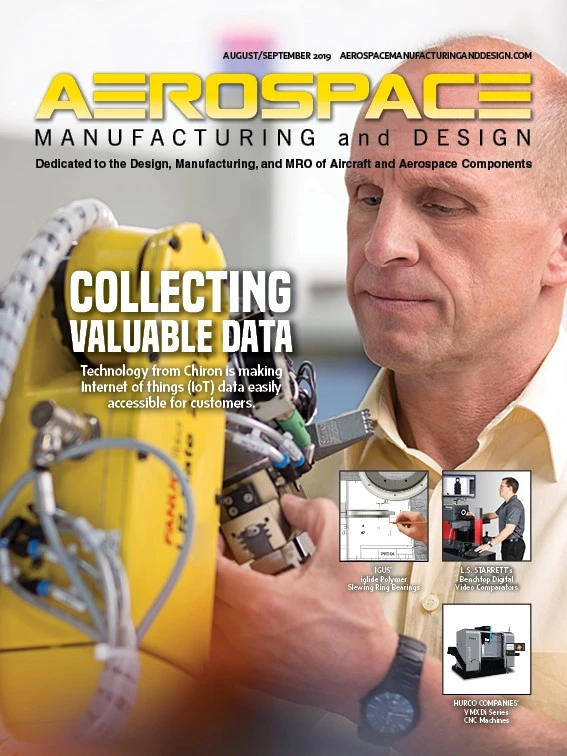
Explore the August September 2019 Issue
Check out more from this issue and find your next story to read.
Latest from Aerospace Manufacturing and Design
- Piasecki acquires Kaman's KARGO UAV program
- PI Americas’ long-travel XY piezo nanopositioners-scanners
- AAMI project call submission deadline extended to May 12
- Jergens launches cast iron tooling column additions
- Airbus to acquire assets relating to its aircraft production from Spirit AeroSystems
- FANUC America's Cobot and Go web tool
- Chicago Innovation Days 2025: Shaping the future of manufacturing
- High-density DC/DC converters for mission-critical applications