
Hydraulic flight control actuators, though simple and reliable, are maintenance-intensive due to leak-susceptible tubing. Fluid-filled lines are also heavy, as fluid goes throughout the entire aircraft. High costs and frequent maintenance work create a need for an alternative.
In today’s passenger aircraft, numerous small electric motors handle aircraft system tasks formerly performed mechanically or hydraulically. Improvements in magnet technology have transformed electric actuators into compact, high-power devices that reduce maintenance costs and lower weight.
“Industrial motors have become a lot more reliable as the push for quality from normal industry has been increasing throughout the years,” says Robin Phillips, aerospace project manager at motor maker maxon. “And it’s at the point now where industrial motors are reliable enough to be used in aircraft with just small additional changes. This means that the aircraft manufacturers don’t need to go to specialist motor suppliers. That makes a big difference for their costs and it’s where our advantage comes in now.”
Since 2010, maxon has supported special projects in space and aviation, with its motor drives incorporated into systems such as safety valves that cut off fuel supply in an emergency. As aerospace business has increased at maxon – nearly 10,000 drives supplied per year for the Boeing 787 Dreamliner – the company has trained its specialists to focus on quality.
“We are providing focused training for our employees, for example, in soldering techniques,” Phillips adds. “At the same time, we are automating high quality standards in production processes with the relevant tools and processes. This enables us to reliably deliver large quantities.”
Several hundred drive systems are now installed in every modern long-haul airliner, with maxon motors controlling items from steering and landing to bathrooms and the Internet.
Automatic aviation systems
As the pilot steers the plane to the runway, they push the thrust lever forward to take it into the air. The control joystick uses small electric motors as part of the force feedback system, letting the pilot know in real-time what is happening at the wings. When the plane reaches cruising altitude and the crew engages autopilot, the throttle lever moves automatically (auto throttle), controlled by a DC motor.
In the pressurized cabin, the plane’s air conditioning ensures that passengers feel well at an altitude of 10,000m. Numerous small valves and actuators, most of them brushless flat motors, control temperature, oxygen, and air. For example, the air conditioning system of a Boeing Dreamliner contains nearly 40 maxon EC 45 flat motors.
In the bathroom, electric drive systems in the background ensure clean processes by regulating water supply and flushing. In the future, planned touchless functions should provide even more convenience.
Seats can be adjusted and even extended to form a bed at the push of a button – electrically and automatically driven.
Recently introduced adjustable seat cushions adjust hardness by changing air pressure to make long-haul flight more pleasant. The manufacturer Lantal uses brushless maxon motors for the valve. If sunlight disturbs a nap, the window blind can be lowered with the push of a button.

Internet connection
In the economy class, screens above the seats extend simultaneously to show safety instructions or movies. An increasing number of passenger aircraft are equipped with communication antennas that continuously and automatically direct themselves to capture the best satellite Internet signals. Each antenna requires three EC-4pole drives with matching HD gearheads.
As the plane climbs after takeoff, the landing gear retracts. To ensure it remains retracted, a motor gearhead combination of a DCX 22 and GP 32 HD operates a locking hook.
By saving significant weight compared with hydraulics, electrical systems also play an important role in making passenger planes more environmentally friendly and cost-effective. Electrical engines aren’t available yet, and air traffic is increasing continuously by 5% per year. To keep pollution from increasing at the same rate, engineers are working to make future planes faster, quieter, and more environmentally friendly.

Kit encoders for stepper motors
Absolute multi-turn kit encoders provide absolute position feedback for stepper motors. They are available with multi-turn measurement ranges, suitable for when a motor is connected to a screw shaft, cable drum, or gear reduction system. The multi-turn rotation counter is self-powered, using Wiegand energy harvesting technology. The rotation count is always up-to-date, even if the machine moved while control system power was out.
The kit or modular devices integrate into a motor housing, measuring the rotary position directly from the drive shaft. Kit packages are available with the same mounting form factor as incremental encoders for NEMA-standard stepper motors, providing drop-in replacements for less advanced incremental encoders. The 37mm x 23mm magnetic measurement module resists dust, moisture, and shock/vibration loading. Shields are available to protect the measurement module from external magnetic fields.

Autonomous Mobile Robot Conference
Key players in the expanding autonomous mobile robots (AMR) market will gather in Louisville, Kentucky, for the Autonomous Mobile Robot (AMR) Conference on September 17, 2019. Sponsored by the Association for Advancing Automation (A3) and the Robotic Industries Association (RIA), the AMR Conference will include sessions about using these innovative tools to increase productivity.
AMRs automate monotonous, repetitive, and potentially injury-prone manual material transportation, freeing staff for higher-value activities. The robots can be implemented without disrupting a building’s permanent infrastructure with wires or magnets added to the floor. AMRs offer easy programming, flexible deployment, and built-in safety features.
“Whether in manufacturing, logistics, or even retail, AMRs are already proving to be a perfect tool for dynamic environments and on-demand automation,” says A3 President Jeff Burnstein. “Conference attendees will learn how to deploy AMRs across myriad applications, learn first-hand how AMRs are changing businesses for the better, and network with leading players in the industry.”
Smart controller vision systems
GigE and USB 3.2 industrial cameras, when used in conjunction with a SmartVision controller, guarantee sharp images and high-quality inspection results.
The machine vision systems provide flexibility, ease of operation, and extend vision capabilities in resolution, speed, interfaces, and flexibility.
Combining industrial cameras and a SmartVision controller provides powerful visual quality control, identification, error proofing, and image processing. The systems are suitable for optical-based traceability, verifying automated processes, and vision-guided robotics.
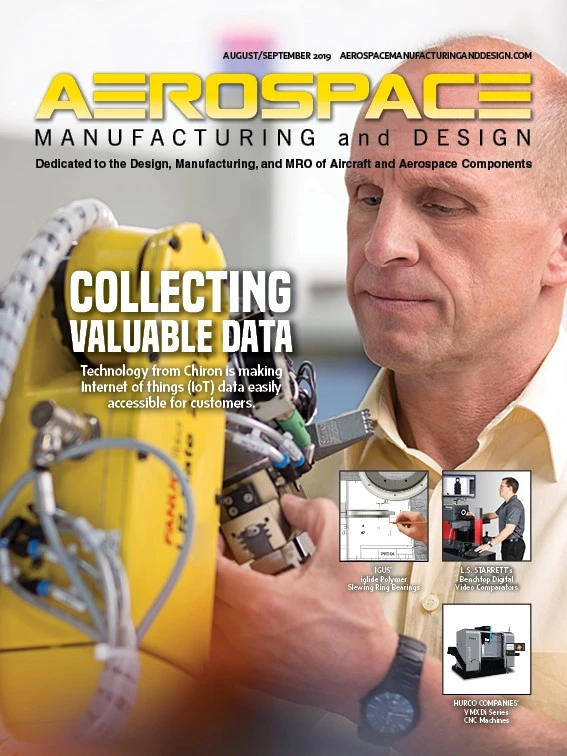
Explore the August September 2019 Issue
Check out more from this issue and find your next story to read.
Latest from Aerospace Manufacturing and Design
- America Makes announces QTIME project call
- Innovation meets precision for 40% faster machining
- Upcoming webinar: Pro tips from a supply chain strategist
- Heart Aerospace relocates to Los Angeles
- Fixtureworks introduces Stablelock Clamps
- Piasecki acquires Kaman's KARGO UAV program
- PI Americas’ long-travel XY piezo nanopositioners-scanners
- AAMI project call submission deadline extended to May 12