
From edge prep to deburring solutions, the partnership between Toolink Engineering Inc. and Cleveland Deburring Machine Co. (CDMC) offers the latest advancements in aerospace manufacturing technology. CDMC’s commitment to quality and precision coupled with Toolink Engineering’s dedication to customer satisfaction elevates production processes to new heights.
Application
A manufacturer specializing in aerospace components sought efficient solutions for deburring inside and outside diameters (I.D. and O.D.) of a diverse range of brass aircraft bushings. Burrs arising from machining grooves and lubrication ports necessitated a comprehensive approach. To address this, Toolink designed a tailored tooling package encompassing quick-change drive tooling and adaptable brush tooling to accommodate various brush sizes required for the wide range of ring diameters. Collaborating with an external company, Toolink arranged for a work stacking machine to feed its application, while the customer opted for a long-reaching robot for loading/unloading each station. Given the scale of the operation, safety was paramount, prompting the installation of an industrial fence and necessary safety measures around the work area.

Solution
For this application, Toolink implemented an off-the-shelf machine base design sourced from its network of contract fabricators. Leveraging a prefabricated base ensures cost savings and enhances efficiency for all stakeholders. To ensure precision and repeatability, Toolink opted for a precision ground and stress-relieved machine base.
O.D. burrs are addressed using a 14" nylon (abrasive) brush, powered directly by a sizable DC motor. A pivot assembly facilitates the movement of the brush between work and home positions. Engaging the system, vertical and horizontal motion is governed by two electronic linear slides with positional feedback for repeatability. Leveraging Auto Amp Compensation, the PLC program uses amperage feedback from the brush motor to determine and automatically maintain cut pressure.
I.D. burrs are treated similarly, employing a nylon brush across a range of diameters. This brush is driven by an output shaft and collet assembly, propelled by an electric motor via an offset belt drive. Auto Amp Comp is also employed to ensure consistent burr removal.

All parameters related to brush feeds/speeds, work rotation, and cutting head travel are adjustable via HMI screens within the program. All part-specific parameters are saved as a dedicated recipe that can be recalled for instant setup in the future.
Part drive assemblies are equipped with pneumatically actuated Kitagawa chucks featuring custom quick-change clamp tooling and increased stroke length. This tooling is designed to seamlessly facilitate the processing of various part family members without necessitating changeovers, and is easily accessible for adjustments when required.
With a skilled team trained in FANUC robot programming, Toolink trains the robot loader to interface with the customer’s preferred work stocker and develop all robot program logic in-house. Additionally, CDMC possesses the capability to manufacture custom end-of-arm tooling for FANUC robots. All manual doors and machine panels that can be opened without the use of hand tools are outfitted with electronic safety interlocks. Disengaging this interlock triggers an immediate halt or fault in machine operation, ensuring swift and reliable safety measures. E-stop recovery is logical and efficient, eliminating the need for an experienced robot tech to reset the machine after a fault.
Results
Toolink’s comprehensive approach to addressing deburring challenges in aerospace component manufacturing showcases its commitment to innovation, efficiency, and safety. By leveraging off-the-shelf base designs, advanced brush technologies, customizable tooling solutions, and skilled FANUC robot programming, Toolink ensures seamless operations while meeting customers’ diverse needs. With safety as Toolink’s top priority, electronic interlocks on machine panels further reinforce its dedication to creating a secure working environment. CDMC is poised to continue delivering cutting-edge solutions and unparalleled service to the aerospace industry and beyond.
Get curated news on YOUR industry.
Enter your email to receive our newsletters.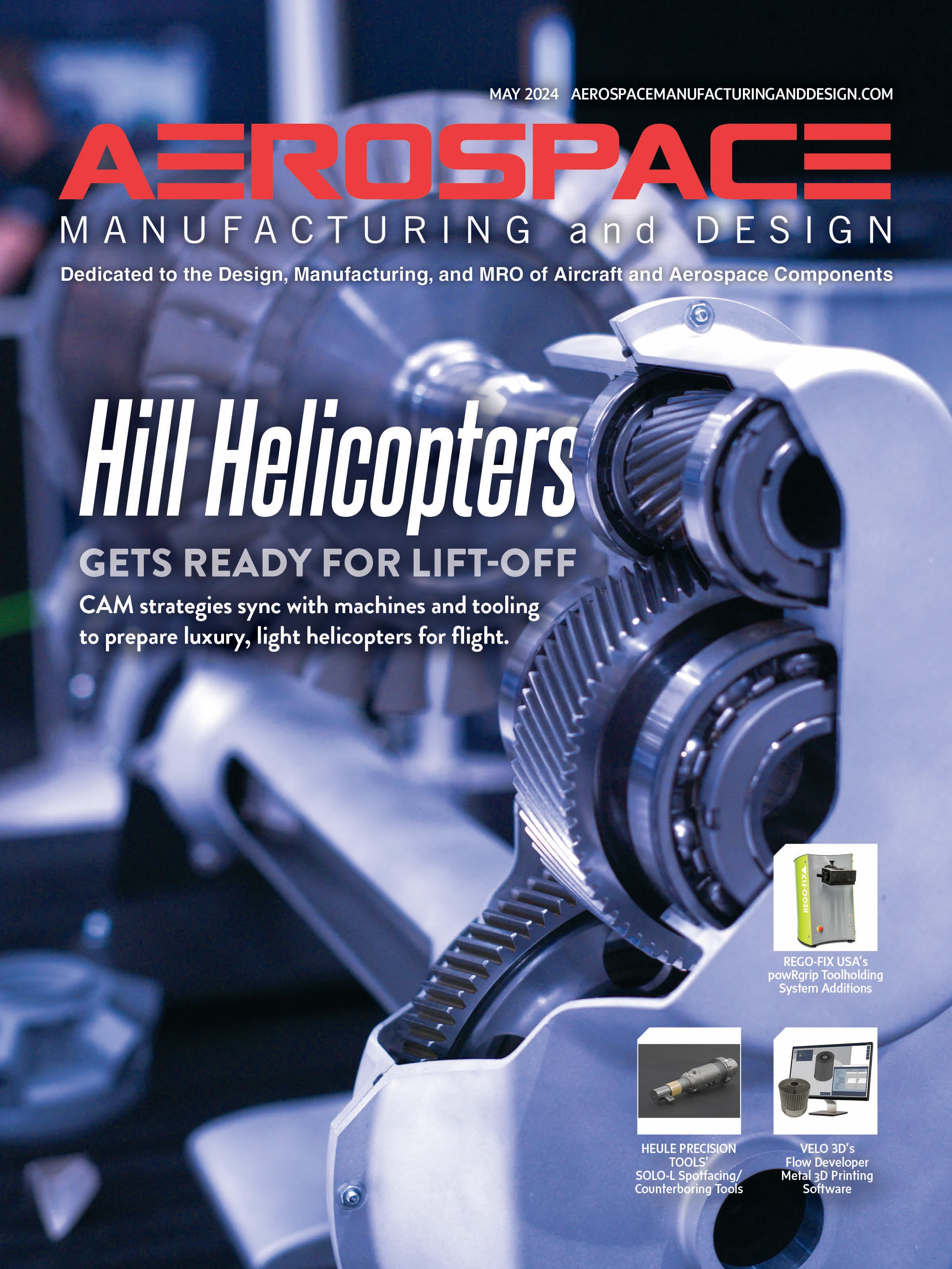
Explore the May 2024 Issue
Check out more from this issue and find your next story to read.
Latest from Aerospace Manufacturing and Design
- NASA-supported technology outfits Venus Aerospace hypersonic engine
- To the Smoothest Surfaces, Finishes, and Beyond | Okuma GA26W
- Extraordinary Starts Where Limits End | Okuma
- Satair, Champion Aerospace sign multi-year distribution agreement
- EMUGE-FRANKEN USA expands N. American solid carbide drill program
- AURA AERO unveils INTEGRAL R to the US market
- Creform Tite-Space AGV fleet
- Cyient Group, Deutsche Aircraft finalize multi-year contract