
With the goals of increased flexibility and reduced maintenance, the next generation CUT S 400 Dedicated wire electrical discharge machine (EDM) improves production of aerospace jet engine turbine disks, especially cutting fir tree blade patterns. The machine allows manufacturers to cut a wider range of turbine blade diameters with fewer production interruptions.
Geared toward disks made from nickel-based or Waspaloy alloys used in the hot, critical side or the cold, non-critical side of an engine, the latest wire EDM handles disks measuring from 160mm to 680mm in diameter.
A more robust rotary/tilt axis manages heavier part loads without risk of deflection. An additively manufactured smaller lower head nozzle size provides additional room for smaller disk diameters while allowing for the use of various types of wire and wire guide diameters.
The eTracking software enables comprehensive monitoring of machine status, job progress, and processing traceability in real time. Spark Track optimizes spark energy in real time to prevent wire breaks and maximize cutting speed. The Intelligent Spark Protection System (ISPS), part of the Uniqua control, identifies the position of each spark along an EDM wire’s length. Knowing the exact location of a spark allows the system to automatically adapt to prevent wire breakage, especially beneficial during long cuts and unattended operations.
The unit has wire coil capacity up to 45kg, six highly efficient filters, and easy integration into automation solutions for lights-out production.
SMART wire spools with radio frequency identification (RFID) improve traceability and efficiency in the production process.
The machine’s design makes it easy to access for cleaning and maintenance, reducing downtime and operating costs. Advancements in the machine’s casting, tank design, and filtration system help combat problems caused by EDM particles/residue generated by long hours of disk production cutting.
For faster, easier cleaning, tank water constantly runs down the work envelope’s interior sides, preventing EDM residue from drying and hardening. To prevent residue from making its way inside filter and drive systems, water constantly circulates through the machine’s upper and lower heads.
In the machine’s tank, all the corners are radiused to eliminate crevices that make residue cleaning difficult. Additionally, the tank channels water flow with EDM residue directly to the tank bottom, preventing residue from being dispersed throughout the work envelope.
The EDM has increased capacity and the number of filters. Quick releases and an air purge system remove water from the filters to reduce their weight, making them easier and quicker to remove. The machine’s pumps are readily accessible and don’t need to be removed for cleaning.
GF Machining Solutions
https://www.gfms.com
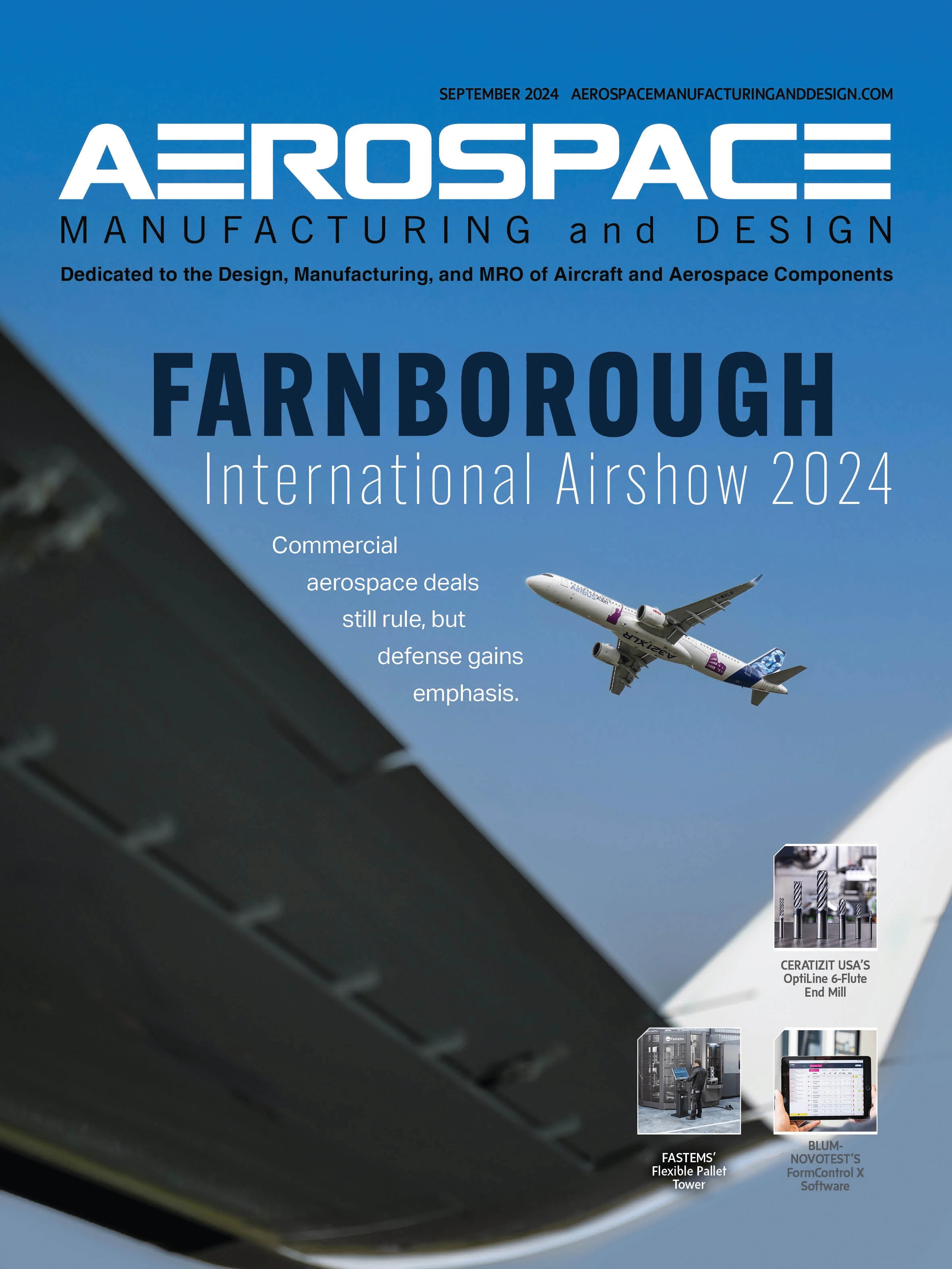
Explore the September 2024 Issue
Check out more from this issue and find your next story to read.
Latest from Aerospace Manufacturing and Design
- Bell awarded funding for X-plane build phase of SPRINT program
- Shaft coupling clamps
- #46 Lunch + Learn Podcast with SMW Autoblok
- Gleason Corp. acquires the Intra Group of Companies
- Thread milling cutter reduces cutting pressure, vibration
- Malaysia Aviation Group orders 20 more Airbus A330neo widebodies
- More displacement from space-tested piezo actuators
- Textron Aviation to bring its largest-ever lineup to 2025 EAA AirVenture