
For aerospace manufacturers, electrical discharge machining (EDM) has long been the answer to achieving high levels of accuracy and precision. The industry has relied on this technology for various parts, especially ones exposed to high temperatures and stresses. Some producers turned away from early EDM equipment because of damaged surfaces, but continued development has resulted in more stable, predictable processes. Among these improvements are automation components. Robots, handling systems, and sensors provide real-time feedback, greater repeatability, and improved quality.
In the following Q&A, Mike Bystrek, national wire EDM product manager at MC Machinery Systems, discusses other advantages of EDM automation, available tools, and considerations for implementation.

Aerospace Manufacturing & Design (AM&D): What benefits does automation offer in EDM machining?
Mike Bystrek (MB): It comes down to knowing how many parts you really need to produce and helps avoid any guess work, keeping work costs under control. For example, an Erowa Robot Compact 80 can be implemented on a sinker EDM to perform automated electrode changing and it changes out the parts as well. So, the good long-term solution is it improves productivity and reduces overall cost.
The biggest advantage to automation is increasing your productivity while reducing lead times. Once a process is proven and automated, it provides repeatable results every time. This ultimately reduces your labor costs, increases part quality, and provides profitability.
AM&D: What smart tools are available on MC Machinery’s wire and sinker EDM machines?
MB: On both the wire and sinker we have an artificial intelligence (AI) system that allows the operator to enter/answer some simple questions on the control, allowing the machine to take over. The system uses real-time condition monitoring within the burn and directly modifies specific parameters for a stable cut that produces optimal results. Because the AI technology analyzes this data, it can reduce overall electrode wear and cost.
In today’s workforce, the older generation of toolmakers in the shop are retiring, bringing in younger people, which is great. But sometimes that experience doesn’t transfer over. So this experience or knowledge we’re building directly into our machines allows operators at all levels to produce quality results.
AM&D: What are some challenges to implementing a wire or sinker EDM in an aerospace facility?
MB: Before you fully automate a process, you must prove that process out. You need to make sure that you’re able to get the part, put the part in the machine repeatably on some tooling, cut the part, and make sure you get the same results. Once that whole process has been proven, I think then you can move on to automating where you can run something like that 24/7. Sometimes people skip the basic steps and try to jump right into implementation, but then miss some of the obvious things.

AM&D: Why is automating EDM important now?
MB: In this industry, whether it’s aerospace, tool and die, or any kind of manufacturing industry, they’re still on a hunt for skilled professionals to do a lot of this work. Having skilled people set up something like this and allow the customer to automate it would enable them to function at a much lower overhead, making them more profitable. And analyzing to determine if results would lead to reduced overall turnaround time or increased productivity or product prove-out would probably be the first thing I would consider for automation.
It also comes down to dollars and cents. Do you really want to pay somebody X number of dollars to stay in there, pull a part, and take it out? Everybody’s worried about them taking their jobs, but I think that would allow a company to be profitable and perhaps open more doors to people to train them in other areas. That’s the way they should be looking at it. By allowing that, productivity increases and your shop will be much more profitable.
It’s important that we achieve a greater acceptance of EDM and the smart tools and controls that can be incorporated. It’s the optimal way to produce a cheaper part more quickly.
Job shop automation for high-mix manufacturing
In collaboration with ProCobots, Hurco has developed a streamlined automation package for high-mix manufacturing to make job shop automation practical, providing automation packages that are flexible, easy to program, and easy to move to other Hurco machines without requiring an integrator to make a change.
The Automation Manager control feature seamlessly integrates automation to CNC machines. It includes a setup wizard, job and queue progress bars, a graphical interface between the collaborative robot (cobot) and the CNC machine to facilitate an easy setup process for each job, run multiple jobs sequentially, and load and save job sets.

Real-time production monitoring
The Smart Manufacturing Platform seamlessly connects industrial assets and business systems to collect data and provide real-time data collection and monitoring from any industrial asset, regardless of brand, age, or process. Reports are accessed anytime, anywhere via browser devices. This cloud-enabled Internet of Things (IoT) platform includes customizable dashboards and alerts, identifying manufacturing bottlenecks and inefficiencies, and streamlining manufacturing processes.
The Freedom Platform is available at three plan levels to right-size the program to individual shop and process needs.

Miniature strain sensors
The DST20 miniature strain sensor provides static and dynamic measurements of large forces across a range of 500µm/m to 1,000µm/m, even within limited spaces. Measuring 28mm x 12mm x 10mm, the screw-on sensors can withstand the rigors of industrial applications thanks to stainless steel housing and protection to IP65. They are suited to challenging industrial environments and mechanical engineering applications, as well as general process automation. The output signal is 1.0mV/V and connection is via an M5, 4 pin, male connector.

Robotic screwdriver
The OnRobot Screwdriver is a smart, complete-out-of-the-box device allowing manufacturers to automate a range of assembly processes quickly, easily, and flexibly.
Programming only requires entering the appropriate screw length and torque value into the user interface integrated into the robot’s teach pendant. With precise torque control and embedded axis, the screwdriver automatically calculates the necessary speed and force. It can detect incorrect screw length, improving overall quality and reducing scrap. With the Z-axis, screws are retracted inside the tool and driven automatically once the robot arm moves into position, which reduces robot arm movement and additional programming. Screws up to 35mm long are retracted completely inside the screwdriver when moving until the screwdriving process is safely initiated, enhancing its collaborative capabilities.
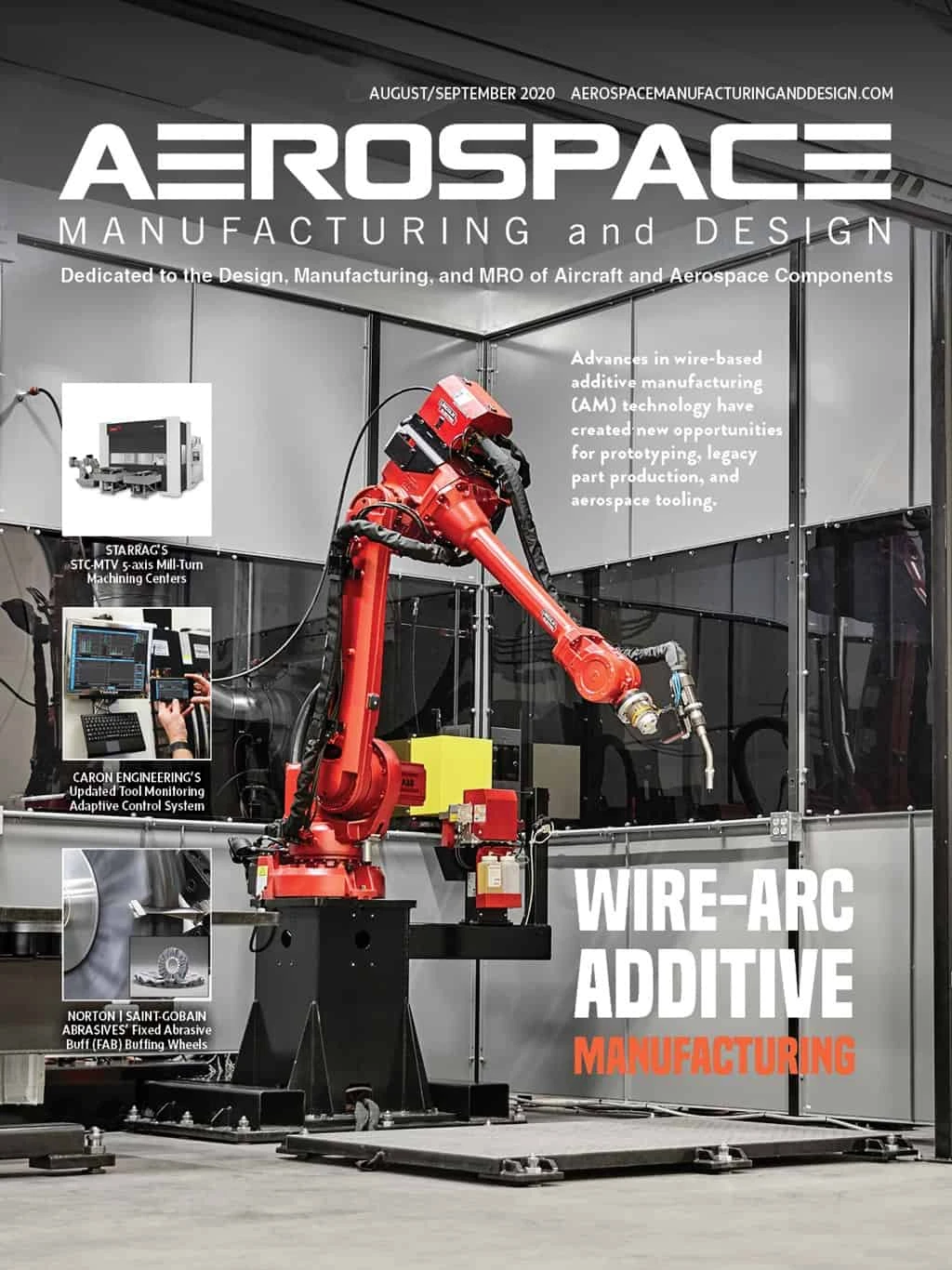
Explore the August September 2020 Issue
Check out more from this issue and find your next story to read.
Latest from Aerospace Manufacturing and Design
- Extraordinary Starts Where Limits End | Okuma
- Satair, Champion Aerospace sign multi-year distribution agreement
- EMUGE-FRANKEN USA expands N. American solid carbide drill program
- AURA AERO unveils INTEGRAL R to the US market
- Creform Tite-Space AGV fleet
- Cyient Group, Deutsche Aircraft finalize multi-year contract
- High surface quality at high speed
- #57 - Manufacturing Matters - Agile & Robust Supply Chain Management with Lisa Anderson