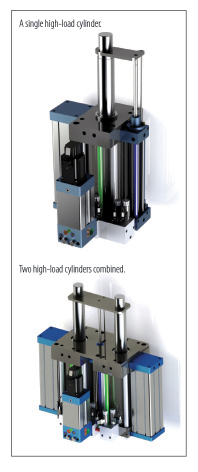
Traditional clamp-and-press actuation applications present the challenge of having a rapid stroke at a low force, while requiring steep ramp-up to a high force for a short period. Achieving these demanding performance parameters typically means expensive oversizing of the hydraulic infrastructure to provide both high speed and high force.
Within this large machine footprint, delivering required position and force control presents complex motion and expense variables. In addition to having too many pieces in the equation, other factors include oversized and continuously running pumps, large hoses that often leak and require maintenance, and the energy consuming valves repeatedly turning on and off while transitioning from high speed to low speed.
To overcome the problem of oversizing components for applications that have a rapid stroke at low force with a load stroke at high force, motion control/actuation specialists Kyntronics have developed a high speed/high force (HSHF) all-in-one actuator. Combining a servo-based SMART hydraulic actuator (SHA), coupled with a high-speed actuator and a high-force pair of actuators – the HSHF delivers a cost-effective solution in a scalable, modular, power-on-demand machine platform.
The self-contained design doesn’t have hoses, eliminating expensive leaky infrastructure. The dual-cylinder configuration results in lower operating costs and better performance across various original equipment manufacturer (OEM) applications.
Clamp, press mode issues
The actuation technology uses hydraulics to overcome issues with existing clamp-and-press mode technologies including:
Clamp mode – In this mode, rapid cycling times are needed while holding a force of 170,000 lbf/756kN going back and forth. This mode is predominant in injection and blow molding applications which require rapid back/forth position and hold, which puts significant pressure on the actuator.
Traditional systems include hydraulics that feature check valves that lock in position. Requiring a large footprint with a large pump and huge hoses, this solution is noisy and expensive. Electromechanical is also another option, but requires large and expensive components including motors, gearboxes, and roller screws/ball screws. Applying loads at the same mechanical position, consistent metal-to-metal contact reduces component life.
Press application– This mode is typically used for 20 ton to 80 ton presses that need to come down quickly and work within a small distance for a short time. This application is currently dominated by hydraulic systems with large power units, pumps, and hoses.
Actuator innovation
As an all-in-one solution, the HSHF’s multi-cylinder, drop-in design features a variable displacement pump, servo motor, servo drive/motion controller, and closed-loop position and force control, with precision position and pressure sensors.
The design eliminates oversizing, and solves issues associated with current options (no hoses, quieter operation, more connectivity) in a reliable small package, potentially saving 50% or more in equipment and operating costs.
A reduced machine footprint eliminates the hydraulic infrastructure and oversized elements. Since there is no huge cylinder or large pump waiting for the cycle to start, it only uses power on demand. HSHF uses minimal energy for the long stroke and proportional energy for the load stroke.
Ease-of-integration with machine control systems and versatile control is possible, as the HSHF actuator is compatible with Fieldbus, I/O (selectable indexes), and analog (0VDC to 10VDV or 4mA to 20mA).
Dual-cylinder design
The HSHF actuator’s approach to hydraulic cylinder design mechanically connects a high-speed cylinder to a larger, high-force dual cylinder.
The dual cylinder combines a larger (high-speed zone) cylinder and a slightly smaller (high-force zone) cylinder together with a piston that seals in the smaller cylinder and moves freely through the larger cylinder. The high-speed cylinder pulls the dual cylinder’s piston through the longer stroke, so oil flows freely around the piston, into the smaller cylinder (high-force zone), sealing the piston, allowing for press or clamp mode. Cylinders can be adjusted to various lengths.
With SMART actuation, the system knows the exact position where the piston enters the smaller high-force cylinder zone and creates a seal. As the smaller high-speed cylinder approaches the high-force zone, the system slows and combines the fluid flow to the high-speed cylinder and the high-force cylinder without stopping motion. The system continues to press forward to the desired location based on force or position. After completing operation, the high-speed cylinder retracts, pulling the piston back. The high-speed cylinder’s speed reduces cycle times with minimal flow, force, and heat, reducing overall energy consumption.
The HSHF actuator design offers rapid, controlled clamp mode and smooth press mode in transitioning from HS-to-HF cylinders – with accurate force and position control.
During press mode, maximum power is required for a short period of the cycle (slower speed with high force) – minimizing the motor and drive size along with heat.
During a clamp mode, minimum power is required to rapidly move the cylinder (extend/retract). During clamping, power is not required as the check valves in the HF cylinder lock the actuator in position and the HS cylinder is placed in float mode to prevent cylinder damage.

Open aperture stage
The AU200-100x100 stage is a low-profile, 80mm (3.15") high stage with a 348mm x 348mm (13.701" x 13.701") footprint. Preloaded V-groove, crossed roller bearings and ground 4mm per-turn lead screws with 2µm of backlash provide high precision and stiffness. Designed for laser drilling, machining, industrial, semiconductor handling, testing, scanning, alignment, assembly, and optical applications, the X-Y stage integrates into many systems.
A recessed mounting and precision pattern of drilled and threaded mounting holes align tooling and fixtures. Solid tooling plates are available for custom and interchangeable applications.
The standard two-phase (1.8°) stepper motors have knobs for manual axis adjustments. Incremental encoders can replace the knobs for position verification.
N. American machine vision market grows 10%
Sales of machine vision components and systems in N. America reached $2.874 billion in 2018, an increase of 9.2% from 2017 and a record for the market. According to statistics from AIA, the industry trade group and part of the Association for Advancing Automation (A3), application-specific machine vision (ASMV) systems led 2018 growth with $1.998 billion in sales, an increase of 7.8% from 2017, followed by smart cameras with $466 million, a 14.2% increase.
Machine vision component markets also set records in 2018 with $401 million in total sales representing 11.7% growth. This increase was driven primarily by component camera sales, which increased 16.2% to $219 million, followed by software (8.9% to $21 million), optics (8.8% to $44 million), lighting (7.9% to $77 million), and imaging boards (1.5% to $40 million).
According to AIA's latest survey, 80% of respondents believe that machine vision component sales will remain flat or decrease in the next six months. Similarly, 62% believe machine vision systems markets will plateau or decrease in the next two quarters. According to Shikany, this prediction might come from a slight softening of the manufacturing sector seen in the last quarter of 2018, which showed the purchasing manager’s index (PMI) in the low 50s indicating slight expansion and the semiconductor market decreasing. The results reflect experts’ belief that this market is due for normalized growth.

IEC connector system
The IEC TS 62735-1 connector system, GS21 socket-outlet and GP21 plug, is rated up to 400VDC and enables a global, standardized approach to DC power distribution in data centers.
From source to load, DC architecture improves overall power supply quality, eliminating harmonic distortions. There is no need for phase compensation, or coupling synchronization to different sources and networks, increasing operational reliability and improving efficiency.
The new IEC TS 62735-1 standard for DC power distribution requires a more complex design than traditional AC connector systems in the IEC standard 60320. The DC connector system design must consider the increased potential for arcing when disconnecting the DC power supply under load. The IEC TS 62735-2 standard for developing a DC connector system rated up to 5.2kW will require additional structural elements, referred to as a safety interlock (cold switch). The GP21/GS21 operates from -5°C to 105°C.
The GP21 rewireable plug accommodates a cable cross-section from 0.75mm²/18AWG to 1.5mm²/16AWG. The GS21 socket-outlet offers mounting options for 1.5mm or 2.0mm panels with quick-connect 6.3mm x 0.8mm or PCB.
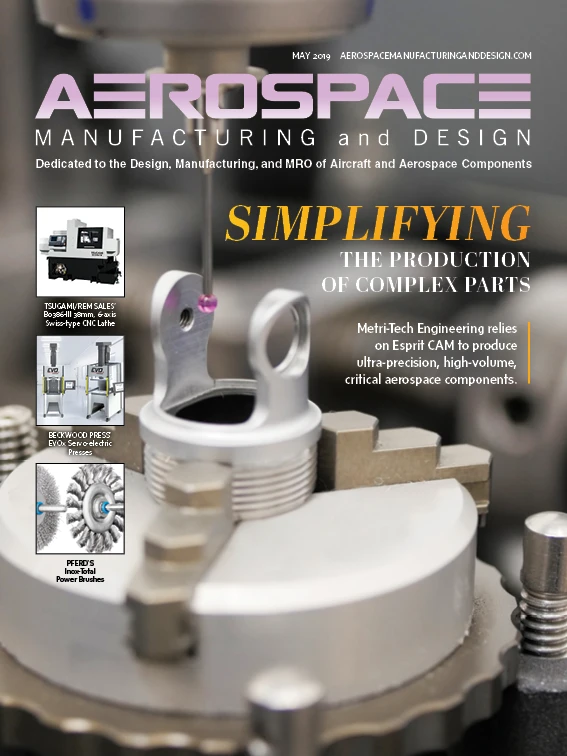
Explore the May 2019 Issue
Check out more from this issue and find your next story to read.
Latest from Aerospace Manufacturing and Design
- Trelleborg acquires Aero-Plastics
- Industrial automation products, enclosed encoders
- #61 - Manufacturing Matters: CMMC roll out: When do I need to comply?
- AIX shows aircraft interiors are a strategic priority for global airlines
- Machine Tool Builders Roundtable: Turn equipment into expertise
- No time to waste: How to machine MedTech parts more efficiently
- The 5 Best and Fastest Spindle Repair Services
- Mill smarter, not harder: How collaboration optimizes production