
The ECONOmaster line of drilling units features low power and air consumption, adjustable motor housing, adjustable total stroke up to 4", hydraulic feed control cylinder, J33 taper spindle end, 0 to 1/2" drill chuck, electric front & rear position limit switches, belt tensioner, and chrome-plated quill. Basic unit weight is 45 lb.
Other key features include adjustable feed stroke of 1/2" to 3", 400 lb thrust at 85psi, operating pressures to 110psi, TEFC/IP56 protection, standard 230V/460V, concentricity of 0.002" TIR, speeds to 9,600rpm, and an air connection retract/advance of 1/4" to 27" NPT.
ECONOmaster drilling units can be supplied with an adjustable stand, inline vertical configuration, and multiple spindle heads for medium-duty production drilling, with many other spindle options and toolholders available.
Suhner Manufacturing Inc.
IMTS 2022 Booth #431205
Multi-sensor vision system

The AVX550 multi-sensor vision system is equipped with dual optical systems and touch-probe capability to measure parts with a range of feature sizes and geometries. The AVX550 can be equipped with two cameras and lenses for sequential use in the same program along with touch probe options. The system features a granite base and bridge design for accuracy, durability, and stability, including under demanding requirements.
The primary zoom lens inspects small intricate features with high precision and resolution up to 2µm. A secondary large field-of-view (FOV) camera is equipped with a telecentric lens simultaneously inspecting large areas of a part, or an entire part itself. Zoom options allow customized configurations to meet specific application requirements and eliminate changing lenses or re-calibrating the system. Throughput is enhanced with fast platform travel speeds and dual collimated profile lights, essential to the effectiveness of dual optical systems.
For inspection of small, intricate areas, a 12:1 zoom lens is equipped with a 26x to 310x magnification range for precise resolution. The fixed magnification telecentric lens comes with magnification options of 0.14x, 0.3x, 0.5x, 0.8x, 1.0x, 2.0x, and 4.0x. Systems can be configured in larger measurement ranges on the X, Y, and Z axes, and be equipped with Q-axis rotary positioners for increased capability.
The L.S. Starrett Co.
IMTS 2022 Booth #135044
5-axis machining center

The PJ 303X 5-axis machining center offers maximum precision and versatility in processing of workpieces up to 230mm tall, 280mm in diameter, and 20kg (44 lb) weight.
The PJ303X is designed to accurately machine smaller parts, its X-, Y-, and Z-axis travels are 300mm, 325mm, and 200 mm, respectively while A-axis rotation is +40° to -100°, and the C-axis rotates 360°. High-speed linear motors move the X-, Y- and Z-axis, employing direct-drive motors. Rapid traverse speed for the X-, Y-, and Z-axis is 20m/min (66fpm).
A 50,000rpm, HSK-E25 taper spindle offers high-speed machining capability. An automatic tool changer stores up to 24 tools up to 40mm in diameter and 100mm in length.
To maximize precision, attachment surfaces of the ways and other critical areas of the machine are hand-scraped. Advanced spindle thermal displacement technology is standard, including a symmetrical gantry column structure that accommodates thermal deformation fluctuations and a thermal compensation mechanism for the machine spindle/head.
Mitsui Seiki
IMTS 2022 Booth #338700
Tool-grinding machines

The VGrind 260, VGrind argon, and VGrind neon grinding machines are suitable for machining rotary tools made from carbide, such as drills, milling cutters, or reamers.
Like the VGrind 340S and 360S models, the VGrind 260 can be configured individually. Customers choose direct-drive or belt-drive for the grinding spindles or equip the machine with a grinding-wheel changer for up to eight grinding wheel sets. The HP 160 pallet magazine offers space for up to 900 blanks or tools made from carbide and the HC4 chain magazine can be loaded with up to 158 shank-type tools or 39 HSK-A63 tool holders. The machine is also available with an internal pallet loader, offering space for two compact pallets with a capacity up to 300 blanks or tools. Random loading of different shank diameters is also possible. The VGrind 260S has kinematic properties with two grinding spindles situated above each other, with the grinding wheel set positioned at the C-axis pivot point for efficient multi-layer machining, reducing machining times due to shorter linear-axis travel distances. The VGrind neon and VGrind argon tool-grinding machines feature the double-spindle concept. They are equipped with an Internet of Things (IoT) gateway and internal wheel measurement system for measuring and monitoring wear. The VGrind argon has a four-wheel grinding wheel changer, an internal pallet loader, and is designed for fully automatic operation.
Vollmer Group
IMTS 2022 Booth #236834
Heavy-duty machine vise

The 5" heavy-duty machine vise is made of stress-relieved ductile iron and is flame hardened, providing very long usable life and predictable performance. The vises are easily moved and relocated by the operator due to the relatively small size and weight, while ensuring secure part holding and tight tolerances from general machining to high production. Additions include hardened jaw plates and a Ball Lock fixture plate quick-change kit. The vise is made in the U.S.A.
Jergens Inc.
IMTS 2022 BOOTH #432154
OEE data collection software
Downtime and production efficiency data from every machine – ranging from CNC machines to presses and fabricating machines – can be collected by ShopFloorConnect overall equipment effectiveness (OEE) and data collection software. Data is displayed in real-time and indispensable manufacturing reports are produced, including detailed OEE reports. The ShopFloorConnect PM Tracker tracks machine preventative maintenance (PM) items by run-hours or machine cycles, issues targeted alerts when an item requires PM, and tracks the maintenance work history for all machines.
ShopFloorConnect 6.0 features a Universal Interactive Application Program Interface (API) enabling users to quickly set up two-way data sharing with any enterprise resource planning (ERP) or manufacturing execution software (MES).
Wintriss Controls Group
IMTS Booth #135073
CNC gear deburring machine

The TM 250-CNC uses a rotary table with twin work spindles to minimize idle machine time and maximize productivity. Machining is performed on one work spindle while the other is simultaneously unloaded and loaded manually. This configuration allows the machine to easily adapt to an automatic loading strategy via robot, collaborative robot (cobot), pick-and-place, or other systems.
Setup personnel can store tool spindle parameters including radial, axial, and tangential positions, as well as tool speed, direction, and pressure. This allows a single setup per part number, reliably repeated simply by loading a program.
Helios Gear Products
IMTS 2022 Booth #236906
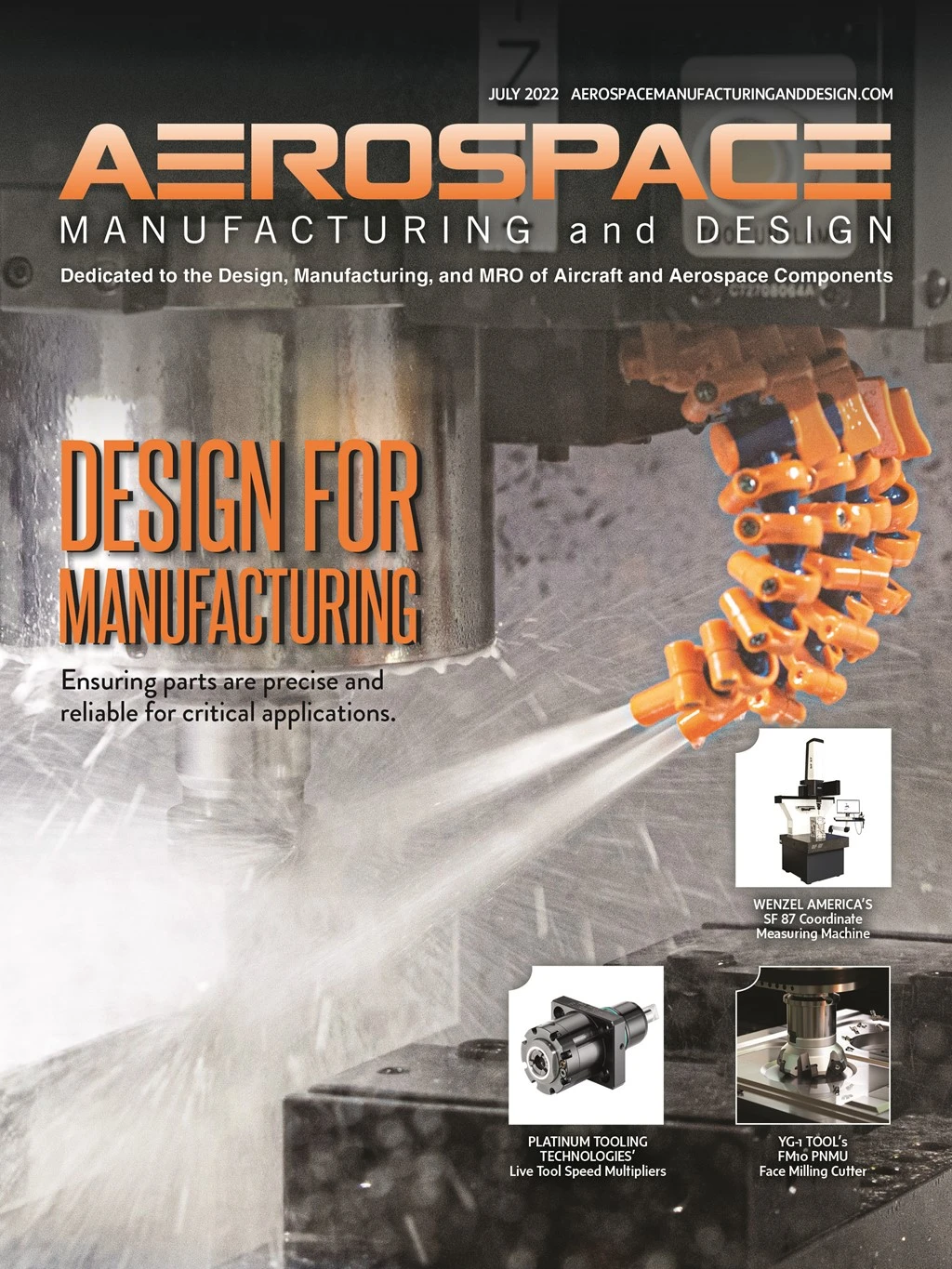
Explore the July 2022 Issue
Check out more from this issue and find your next story to read.
Latest from Aerospace Manufacturing and Design
- GE Aerospace secures Air Force engine contract
- Thomson Industries' online sizing and selection tool
- #53 - Manufacturing Matters - 2024 Leaders in Manufacturing Roundtable
- Join us for insights on one of the hottest topics in manufacturing!
- You can still register for March’s Manufacturing Lunch + Learn!
- Ohio creates Youngstown Innovation Hub for Aerospace and Defense
- Tormach’s Chip Conveyor Kit for the 1500MX CNC Mill
- How to Reduce First Article Inspection Creation Time by 70% to 90% with DISCUS Software