
Within all industries, reduced cost, improved quality, and faster time to market are primary goals. Digital transformation, a major trend for driving product and process innovation to meet these goals, leverages data and electronically managed processes to capture previously missed benefits. However, it can be a large effort requiring modification of data structures, processes, and applications to digitize (convert paper and electronic documents into data elements) to improve data capture and consumption.
Aerospace and defense (A&D) presents huge challenges at every point in the product life cycle. (See Figure 1.) Software can address these challenges, but it’s often implemented only within a functional area or department, resulting in a disconnect between functions and data consistency.
Certification issues
Aircraft have three different types of certifications: class of aircraft, production certification, and airworthiness certification (details in the sidebar). These certifications support the most basic aircraft, such as a 60-year-old Piper Cub, to a recently delivered wide-body aircraft (e.g., Airbus A350 or Boeing 777X). Without certifications, a plane can’t be sold or legally fly.
Certification is the result of verification and validation processes. Parts, sub-systems, systems, and the complete product and its maintenance and repair procedures must be tested to ensure they meet U.S. Federal Aviation Administration (FAA) or other organization requirements. The documentation must be available for audit to ensure every event was properly resolved.
Certification previously accounted for 25% of program cost, but now it’s quoted at 75% due to product and program complexity and more stringent regulatory regimes. Concentrating on certification and program management – including the handoff between functional areas – can improve program measurement parameters (cost, time-to-market, and quality).
The cost of certification is rising because of increasing complexity and regulatory requirements due to the inclusion of more software, which adds capabilities within and between systems, but grows exponentially the number of tests to ensure all variants are validated. Many tests require complex setup and configurations of sophisticated equipment. Keeping test schedules up to date with design releases, manufacturing schedules, and configuration changes is a challenge. Any change or error affects production and test schedules, and rescheduling adds to cost and the certification timeline.
Improving certification processes
Digitization and digital transformation can improve A&D certification processes by leveraging computer-based solutions to create and manage data, leading to better business performance.
Two recent solutions to address certification costs and timelines are virtual testing and integrated program scheduling and execution. These solutions are key elements of digitization and digital transformation programs.
Digital simulation and virtual testing
Finite element analysis (FEA), computational fluid dynamics (CFD), and other physics-based simulations – along with logic and software simulators – have been connected to 3D geometric models. This data and process integration defines complete, complex digital models of aircraft and their sub-systems and executes simulations mimicking real-world operation of sub-systems, systems, and even full products. The simulations are validated against traditional physical testing so results can augment or replace physical testing in some certification processes. With the emergence of the Internet of Things (IoT), it’s easier to capture physical test results in digital form and use data to validate and drive virtual testing.
The benefits of virtual testing are: shortened time-to-market, reduced cost, and improved quality. Since virtual tests run on digital models, multiple tests can run simultaneously using the same model. Use cases that would be destructive, time consuming, or too expensive can be run virtually, improving quality and ensuring design robustness. One simulation expert can run several virtual tests that typically require many hours with a team. Tests taking hours in real-time can be executed in minutes virtually.
Integrated program management, execution
The A&D certification process often operates isolated from product development, and project management and execution tracking are often disconnected from product and test data. Keeping project schedules up to date is a painful manual process resulting in gaps, usually because someone forgot to make an update. In many companies, testing isn’t tracked directly on the master program schedule, requiring results to be linked and updated via manual intervention. Something changed in a schedule that isn’t updated wastes time, causes errors, and delays certification.
Modern product lifecycle management (PLM) platforms have integrated project and program management capabilities. The solutions have common project management capabilities such as Gannt charts, activity and task management, and critical path calculations. The big differentiator with integrated solutions is activities and tasks having visibility to product data including 3D models, simulations, parts, bill of materials (BOMs), test plans, and results. Data will be automatically associated with their assigned activity.
Data authors must only update one system, because when a task is complete, associated data can close the assignment. Project managers have a more accurate view of the project status, and integrated solutions eliminate chasing people for that data. The solutions also provide an alternative structure to navigate product information. Computer-aided design (CAD) and BOM management systems can be complex for casual users, but project management solutions are usually easier to navigate, making self-service possible, shortening timelines and decisions.
Other common application areas include supply chain integration and improved integration with manufacturing, but all the areas shown in Figure 1 can benefit.
Conclusion
Getting certified A&D products to market is expensive and time consuming. A new aircraft program costs billions of dollars and can take five years or more from inception to first delivery. Major delays can put even the largest, financially sound companies in jeopardy. Certification, ensuring the product performs safely, greatly increases aircraft program cost and timelines. Billions of dollars have been invested in information technology (IT) projects to improve A&D business performance without achieving that goal.
Digital transformation is a modern approach to business and process improvement that better uses legacy investments and guides implementation of new technology and business process improvements. Modern PLM solutions can address business process issues and speed the certification process at lower cost. High-impact techniques such as virtual testing and program management within a digital transformation strategy allow companies to address primary market drivers of globalization, competition, product complexity, regulations, and pricing, to achieve their business goals.
.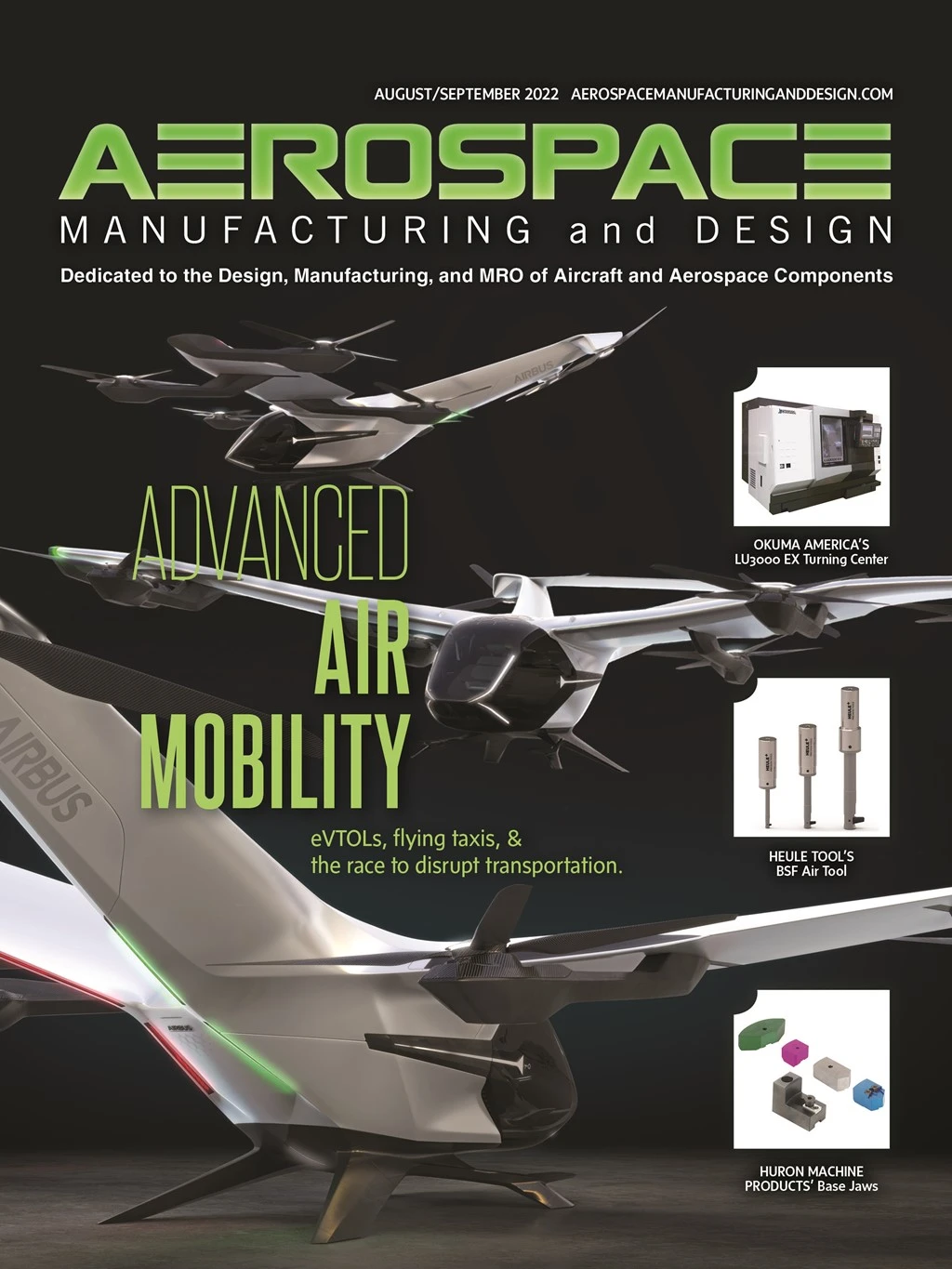
Explore the August September 2022 Issue
Check out more from this issue and find your next story to read.
Latest from Aerospace Manufacturing and Design
- Safran Defense & Space opens US defense HQ
- Two miniature absolute encoders join US Digital’s lineup
- Lockheed Martin completes Orion for Artemis II
- Cylinder CMMs for complex symmetrical workpieces
- University of Oklahoma research fuels UAS development
- Motorized vision measuring system
- Everyone's talking tariffs
- Boom Supersonic to launch Symphony engine testing in Colorado