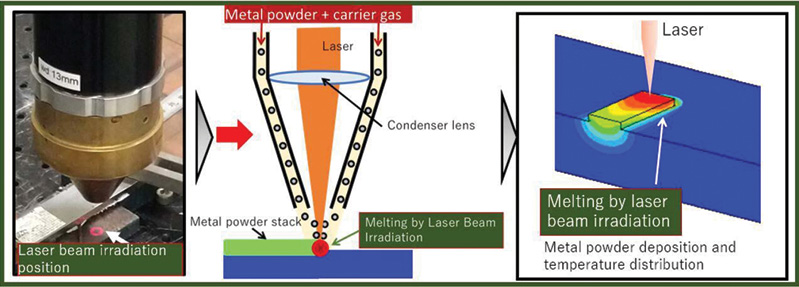
Japanese researchers have developed a mathematical model of laser-directed energy deposition (LDED) technology that automatically generates a metal powder deposition region, eliminating the guesswork needed to optimize production. The findings of their study, published in the Journal of Thermal Spray Technology, promise to make 3D metal layered metal fabrication by LDED repair technology more effective, with efficient resource management to improve its sustainability.
In LDED, metal powders are deposited at the focus of a laser beam, then melted and stacked.
“The thermal radiation-thermal conduction model and the viscoplastic-thermoplastic constitutive model are applied to the stacked elements that constitute the deposited region, so a wide range of state changes from melting to solidification of the deposited layer of metal powder can be simulated. By incorporating these models into a finite element analysis program, we have developed a new machining analysis system that’s never been used before,” notes Dr. Masayuki Arai from the Department of Mechanical Engineering, Faculty of Engineering, Tokyo University of Science (TUS), Japan. The team numerically simulated the restoration process to predict the forming process conditions, temperature distribution, deformation state, and residual stress distribution in advance and verified the findings through experiments. They found residual stresses in the deposited layer were much lower than those obtained via conventional repair processes.
This novel 3D machining numerical analysis system is a digital twin of the existing machining technology based on the fusion of metal in the area to be repaired. The numerical analysis method could be applied to various industrial applications in the future, such as repairing the thinning of the tip of a gas turbine’s rotor blade.
“Using our technique, the surface shape of a metal structure can be completely restored on-site, and the disposal of the metal powder required for repair can be significantly reduced. However, the optimum forming conditions required for the widespread application of this technology in industry had to be determined by a trial-and-error process,” explains Arai, who has been actively involved in the research of damage mechanics and repair technology.

Taken together, the features of automation and advance prediction of process conditions by the numerical machining analysis system make 3D metal layered metal fabrication by LDED repair technology more effective, with efficient resource management to improve its sustainability.
In addition to Prof. Arai, the researchers include Toshikazu Muramatsu, also from TUS, and Dr. Kiyohiro Ito from Department of Mechanical and Electrical Engineering, Suwa University of Science, Japan, in collaboration with the Thermal Spray Technology Development Laboratory of TOCALO Co. Ltd., Japan.
Tokyo University of Science, JapanReference
“Three-Dimensional Numerical Simulation of Repairing Process by Laser Direct Energy Deposition,” Journal of Thermal Spray Technology

Explore the March 2023 Issue
Check out more from this issue and find your next story to read.
Latest from Aerospace Manufacturing and Design
- Piper Aircraft receives its largest ever domestic trainer order
- Miniature, high force-to-size linear voice coil servo motor
- MagniX, Robinson to develop battery electric R66 helicopter
- Zero-point clamping modules
- Hartzell electric engine propeller earns FAA approval for AAM
- Thin profile flame and thermal barrier
- Guill Labs offer materials and extrusion testing
- High production vertical honing systems