
More than 90% of the digital data we have today has been created in the last two years. That astonishing statement comes from Jagannath Rao, senior vice president of data services for Siemens’ Digital Factory division. He was speaking at a Discover Global Markets event organized by the U.S. Commercial Service, U.S. Department of Commerce, in Cleveland, Ohio.
Digitalization is changing everything, Rao asserts, and rapidly. Five-and-a-half million things are connected every day, and 50 billion things will be connected by 2020. A lot of those things will be the machines, motors, controllers, gear boxes, and other devices used in manufacturing, as part of the Industrial Internet of Things (IIoT).
Rao sounds the now familiar alarm that the digital disruption is coming, whether you like it or not, and companies that do not adopt digitalization will be left behind. Other manufacturing leaders look to large companies, including Siemens, to define the digital protocols that will let machines talk to one another seamlessly and use a common data language (see EMO Hannover Roundtable, page 34).
Yet Rao sees customers now wanting to know what they can do to improve their businesses, operate more reliably and safely, and how to differentiate themselves from the competition through digital transformation. Wanting increased productivity, reduced operating costs, and improved reliability hasn’t changed – what has changed are the technologies that allow us to achieve those goals: computer power, connectivity, bandwidth, sensors, artificial intelligence, and machine learning. All have made great strides in the past 20 years.
Devices, systems, processes, and machines are producing tremendous amounts of data, so it should come as no surprise that this data will be subject to analytics generating insights that will change manufacturing, Rao states.
Improving asset performance starts with collecting and looking at data for patterns and trends. This can take 6 months to a year. Even without analytics, data can inform how much, how often, and where some event is happening. That insight can be used to predict asset performance, allowing one to proactively schedule maintenance to reduce downtime.
Analyzing Big Data with software tools to learn why something is not performing provides the insight that can optimize processes and improve productivity. I’ve seen this progression likened to a journey taken step-by-step or a ladder one climbs toward enlightenment and mastery; it’s applicable to any asset.
For Rao, the future of manufacturing is smart and connected, with machines talking to themselves, self-diagnosing their problems, and freeing humans to see processes in real time so they can think of ways to take business to the next level.
Rao warns that manufacturers who don’t adopt digital transformation are going to be left behind. Somebody will always be disrupting our current way of doing things. It’s much better if we are the ones doing the disrupting.
Rao believes America can be a leader in digital transformation. Are you adopting any cutting-edge digital technologies to make sure your business is a disruptor?
– Eric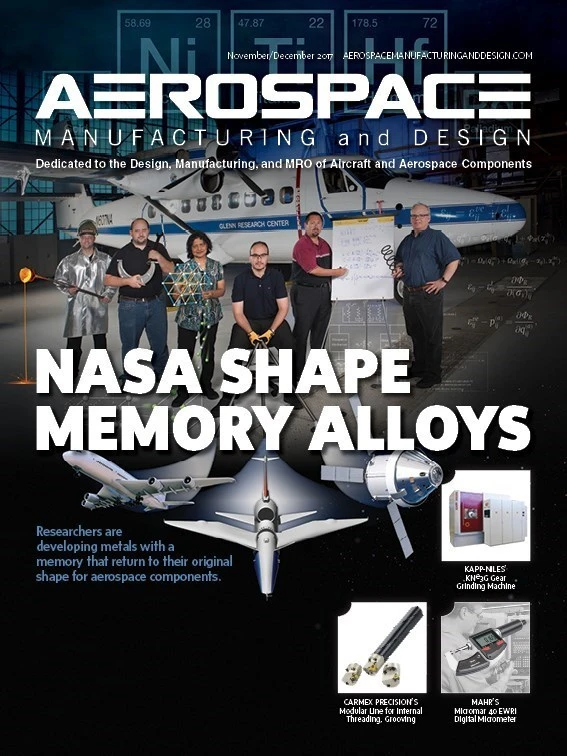
Explore the November December 2017 Issue
Check out more from this issue and find your next story to read.
Latest from Aerospace Manufacturing and Design
- AAMI project call submission deadline extended to May 12
- Jergens launches cast iron tooling column additions
- Airbus to acquire assets relating to its aircraft production from Spirit AeroSystems
- FANUC America's Cobot and Go web tool
- Chicago Innovation Days 2025: Shaping the future of manufacturing
- High-density DC/DC converters for mission-critical applications
- #59 - Manufacturing Matters: Additive manufacturing trends, innovations
- ACE at 150: A legacy of innovation and industry leadership