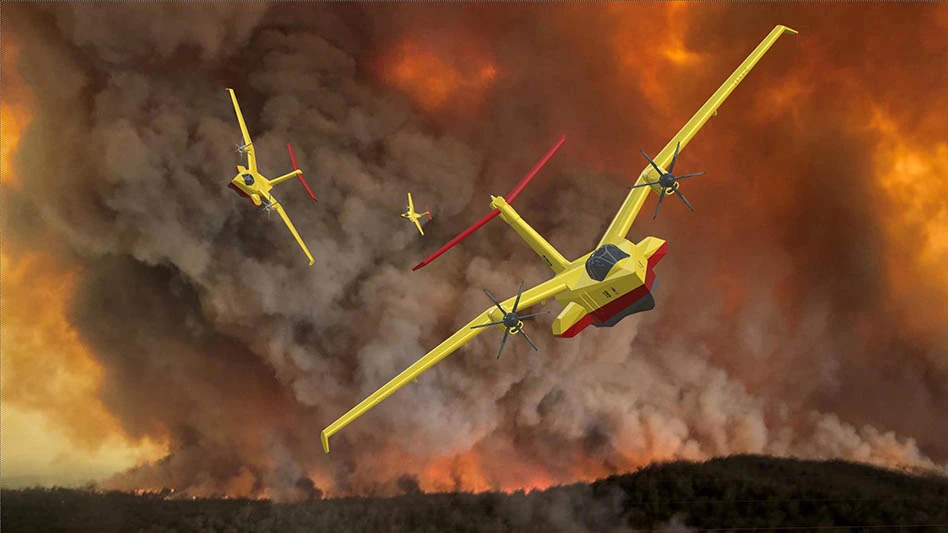

To help combat the growing threat of wildfires, Belgian company Roadfour is developing a next-generation, large-capacity amphibious firefighting aircraft using digital transformation technologies from Siemens Digital Industries Software. The Seagle aircraft will have a fly-by-wire flight control system, a modern cockpit with a canopy for greater visibility, and modern avionics that integrate water-drop targeting and navigation capabilities. The twin-engine amphibian will scoop, carry, and drop 12,000L (3,170gal) of water per run, double what the most widely used aerial firefighter now achieves.
The Seagle will also integrate structural system health monitoring to lower maintenance costs and ensure fleet readiness.
Urgent need
In 2022, Europe had the highest number of wildfires in addition to the most severe drought in Europe in 500 years, destroying homes, wildlife, natural habitats, and endangering people.
Between June 1 and August 31, 2022, those wildfires emitted an estimated 6.4 megatons of carbon gasses, the highest level in Europe since 2007. Current firefighting capabilities aren’t sufficient to counter the consequences of wildfires estimated to increase 30% by 2030.
The global market size for amphibious aircraft with large scooping capacity is now estimated at 300 aircraft between 2030 and 2050 including fleet replacements, fleet extensions, and new entrants to the market. Roadfour plans to deliver the Seagle by 2030. It’ll be the first water bomber in its segment designed and built in Europe.
Aerospace Manufacturing and Design recently spoke to Gaëtan Du Four, CEO of Roadfour and Thierry Olbrechts, director of Simcenter Aerospace Industries Solutions, Siemens Digital Industries Software, to learn more about the Seagle’s origins and development.
Aerospace Manufacturing and Design (AM&D): The Seagle is said to be the result of a collaboration between experienced aircraft engineers, firefighting experts, pilots, and aviation specialists from different countries. How did that occur?
Gaëtan Du Four (GDuF): In 2021, we went around Europe, the U.S., and Canada, to get their inputs. We heard dropping 6,000L of water is no longer sufficient.

As a new original equipment manufacturer (OEM), we reached out to Siemens to see what kind of collaboration they offered in digital tools, not only the CAD, but also simulation, aspects of producing instructions, and certification. They covered the whole thing in a digital thread from concept, requirements management, and specification, all the way to service operations in support of the aircraft.
Thierry Olbrechts (TO): At Siemens, we found this project very socially relevant with respect to the climate, and the problems related to wildfires become more acute. This aircraft is needed to address the problems. Engineering such a project requires design requirements management, answering questions such as how can you make sure the engineering processes are optimal? By using digital capabilities? We want to work together with that.
AM&D: Developing a new aircraft usually takes a decade or more. How do you expect the software to accelerate that process?
GDuF: You say it usually takes a decade; we say we can do it in seven years from where we are now to the potential of type certificate or entry into service. We didn’t compare it to doing it the old way or the classic way, because we assumed from day one we’d be mostly all digital or as much digital as possible.
AM&D: What are the features of Siemens Xcelerator software and what advantages does it offer to a startup?
TO: Siemens Xcelerator has wide capabilities. Siemens invests in making sure all the engineers are getting the right skill tools to fulfill their jobs within aircraft development. Xcelerator allows customers to speed up development by better exploiting the digital data available during the different steps of development.
When you want to exploit digital capabilities from the start, which is needed with respect to certification, the sooner you have a more integrated way of working on a digital tool, the better. That’s why we’ve defined start packages, where we give users easy access to the capabilities early in the program. We realize setting up such a program is a major challenge: you need to set up, you need to staff all the different functions, you need to provide the capabilities, and that requires a lot of flexibility. In that context, we want to make sure whatever Roadfour needs is available. We also want to be sure that we support them with training and template models that might be helpful. We also make sure the licensing schemes are flexible, with respect to capabilities to run on premises or run in the cloud. Xcelerator is being deployed more in the cloud. Also, access to high-power computing capabilities is part of that.
AM&D: How do you anticipate the software helping with aircraft assembly?
GDuF: Our industrial strategy is we’ll do the overall aircraft design. In our final assembly, we’ll be receiving basically plug-and-play big modules – wings, fuselage, tail.
The type certificate and all the certifications are under our scope, which is why the whole digital thread is so important for us, because we’ll be sharing so much data back and forth, whether it’s CAD models, requirements, specifications, or test results between the Tier 1’s and ourselves all throughout the design phase. Afterward, during pre-production or prototyping, we’ll need to keep track of all the design changes, the revisions. I can’t imagine doing it any other way than fully digital.

The product lifecycle management (PLM) system from Siemens allowed us to import all this data with the ability to still manage all the revisions, manage the version history. We can do the assembly of multiple data sources and interact with the interface management. That was a huge criterion for us going with Siemens.
TO: Many capabilities come as digital thread but it’s very open, a value point we want to keep, that openness. There’ll be a large supply chain that needs digital communications to run fluently.
GDuF: We’ve completed the feasibility study of the overall aircraft architecture, the requirements. We talked with all the customers or potential customers in Europe and North America, as to what is their wish list of what they’d want to see in a next-generation firefighting aircraft. I think we have a very good handle on customer operational requirements, flight performance, operational performance, and maintenance.
The next big milestone is to freeze the aerodynamics, the flight physics, the center of gravity, weight, and balance – the domain system specifications.
That’s our next phase, which we think will take about 12 months. Then we go into the preliminary design phase, where we start involving the Tier 1’s. We’ve gone through request for proposal (RFP) phases already with some. Then it’s up to the Tier 1’s to detail design and build. Roughly 12 months for the concept phase is ahead of us, probably another six months afterward to define all the preliminary design phases. Then the Tier 1’s have another 12-to-18 months after that to do the detailed design and start the tooling work. We want to get to the first prototypes by year five.
Get curated news on YOUR industry.
Enter your email to receive our newsletters.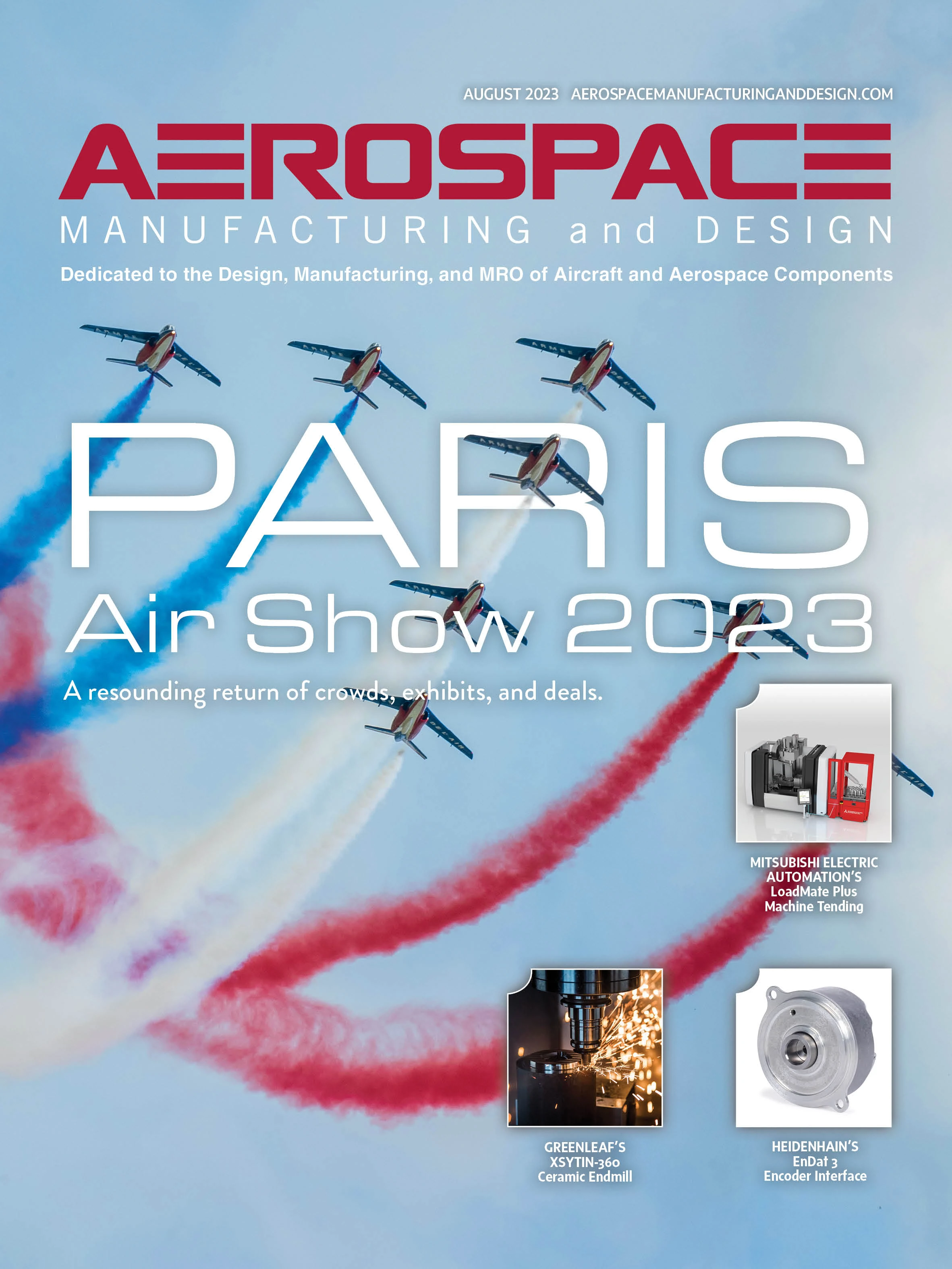
Explore the August 2023 Issue
Check out more from this issue and find your next story to read.
Latest from Aerospace Manufacturing and Design
- Beyond Aero refines its hydrogen-electric light jet
- Americase's advanced protective solutions
- GE Aerospace secures Air Force engine contract
- Thomson Industries' online sizing and selection tool
- #53 - Manufacturing Matters - 2024 Leaders in Manufacturing Roundtable
- Join us for insights on one of the hottest topics in manufacturing!
- You can still register for March’s Manufacturing Lunch + Learn!
- Ohio creates Youngstown Innovation Hub for Aerospace and Defense