

For decades, metallic titanium has been produced using the Kroll process to generate titanium chloride compounds, then porous metallic titanium sponge, which is purified, crushed, and pressed before it’s melted into an ingot under a vacuum. The ingots are often remelted to make them more uniform, but remelting adds to the cost. The low-output Kroll process also creates a large amount of CO2, chemical waste, and uses chlorine – contributing to environmental challenges.
Andriy Brodskyy saw an opportunity to rethink how titanium is produced. In three years of research and with $3 million in investments, scientists at Brodskyy’s research center developed, improved, and patented a titanium metal alloy production method, the Velta Ti Process, that consumes less energy, has fewer steps, and generates zero waste. As the process also creates saleable byproducts, the cost of titanium is reduced by a factor of four.
To tell us more about the company and its plans are:
Olena Lesnyak, A director and deputy CEO of Velta, is responsible for sales, marketing, and strategic development. She has more than 16 years of experience in sales and marketing of Ukrainian and international companies, 10 of them in the titanium industry.
Artem Yarovinsky, Velta’s sales and marketing director, has 7 years of international experience in the titanium industry. His research efforts include publications in international and domestic specialized periodicals.
Andriy Brodskyy is the founder and CEO of Velta and heads the building of a pilot plant for producing titanium powder and finished products in Ukraine. He has more than 15 years’ experience in the global titanium industry. He opened the Velta RD Titan research center, which developed and patented a new production method for titanium and its alloys.
Aerospace Manufacturing and Design (AM&D): What was the driving factor behind the formation of Velta?

Andriy Brodskyy (AB): Velta’s story began in 2006 when I acquired the license for the Birzulivske titanium ore deposit and began actively preparing the project for launch. Within five years, my team and I managed to do everything from exploration and approval of reserves to attracting funding and building the first private titanium mining and processing complex in Ukraine.
Olena Lesnyak (OL): Velta has been mining ilmenite titanium ore in the middle of Ukraine for more than 11 years. It’s been a partner for many European, American, and Asian companies producing titanium pigment, and now Velta provides about 2% of the world’s titanium feedstock. But being the feedstock supplier was never the final goal of the company. The company’s goal was vertical integration, especially in producing metal powders for 3D printing (3DP) and additive manufacturing (AM) in the medical and aerospace sectors. That prompted us to create our own R&D center that developed and patented innovative technology for production of titanium powder to produce titanium goods.
Many companies have been searching for an alternative method to produce titanium metal because the existing Kroll technology’s environmentally unfriendly and very energy consuming. This makes for a long, extremely costly process making titanium extremely expensive. With the great potential and the qualities titanium has, its high cost significantly decreases its potential use. Our technology allows production of titanium powder in a less expensive, leaner, faster way that’s also environmentally friendly. All the solid waste is turned into high-margin saleable byproducts. We have zero liquid waste, and 8x less CO2 emissions than the Kroll method.
The ultimate goal of our technology is to develop AM applications. We’re planning to build a plant to produce 10,000 tons of titanium powder and finished titanium goods in the United States. We believe there’s going to be a very fruitful and useful cooperation and synergy between the two countries, with Ukrainian technology and a U.S. facility able to provide titanium powder, produced locally, which hopefully will decrease dependence on obtaining titanium from Russia and China.
AM&D: Will you be supplying the raw materials for the U.S. factory?
OL: That’s the plan. In the U.S., there are few sources of ilmenite. But the material supply isn’t the critical issue, so Ukraine or Mozambique, Madagascar, or Africa, India, Australia, could be the source.
AM&D: Can you offer an overview of the vertical production chain Velta delivers?
Artem Yarovinsky (AY): We transform ilmenite into a form of titanium dioxide and subsequently transform it directly to titanium powder we can use for traditional powder metallurgy or spherical powder for AM. In the complicated, energy consuming, and costly Kroll method, the outcome is titanium sponge. Then you still need several melting stages until you can get titanium powder, and this only melts at very high temperatures. It also increases time, price, CO2 emissions, and energy consumption.
AB: Our Ukrainian scientists developed the Velta Ti Process in response to old technologies. We set two key indicators of the project success: making the technology green and opening maximum access to titanium implementation as a critical material. And we’ve succeeded. Initially, I strived to deal with civil titanium, but the war in Ukraine irrevocably changed titanium market priorities and now it’s all defense and aviation.
AM&D: Velta Holdings has received patents for its Velta Ti process for titanium powder and metal alloys. How does this process reduce the cost four-fold while being environmentally friendly?

AY: We eliminate the sponge stage, and from the ilmenite, we jump ahead to titanium dioxide and titanium powder, using fewer steps and less electricity. Our carbon emissions are more than 5x lower compared with the Kroll method. Also, we don’t use chlorine that’s harmful to the environment. We don’t have any solid waste, because we process that into sellable byproducts, and have zero liquid waste.
AB: Another advantage is access to lower-cost titanium parts production. The industry’s average buy-to-fly ratio for titanium parts production using Kroll’s sponge is 10:1. When using Velta Ti Process powder with powder metallurgy or additive technologies, the ratio is 1.5:1.
AM&D: Is there a target for how much titanium powder you make per year?
OL: We have the technology at the lab scale, producing in small quantities. In 2021, we started construction of a demonstration facility in Ukraine to show potential investors and final customers the technology, step-by-step, at a quarter production level, and produce samples for qualification and certification. When the war started, we had to stop everything, and dismantle the facility. We waited for about half a year, hesitating about what to do next. Finally, we decided to continue, but in a different country. We’re constructing a demonstration facility in an eastern European country, to be ready by the end of summer 2023. We’ll then start plant construction in the U.S. We’re in communication with several states now, choosing the best location for our plant. Hopefully, we’ll have settled on the location with all the paperwork done around the end of 2023 or early 2024, and will start construction.
AM&D: How does AM affect designing and manufacturing aerospace parts?
AY: AM makes it possible to produce very complicated parts. And it’s getting to be a greater percentage of applications in the aerospace sector. With the help of the titanium powders we’re making, AM could make complicated parts faster because they could be made at the end user’s facility.

AM&D: How is the Russian invasion impacting mining, production, and export?
AB: We needed to build a new supply chain, and we built it, continuing to deliver to Europe and the United States. Further, we needed to make a study of the rhythmic supply of components, especially Ukrainian ones, due to the occupation of various territories. The autumn challenge was power outages. Nevertheless, Velta fulfilled 62% of the 2022 plan, developed before the war. I consider this a worthy result and, taking into account all our achievements in 2022, I’m quite optimistic regarding 2023. We didn’t put off our American expansion.
OL: The first two weeks after the invasion were tough, when we had to realize what’s happening. After that, a lot of things we had to restructure, but we are continuing our daily operation. The toughest point was logistics, because of the blockage of the Black Sea. But we managed to overcome these complications, along with help from our long-term, traditional customers who are also our reliable partners. It puts pressure on our cost and economical conditions, but we managed to continue, and to pay taxes to support our government, the army, and our workers, paying them salary regularly to give them some stability over these uneasy times.
AM&D: Do you have financing for the U.S. expansion?
OL: We’re looking in different directions for that. We understand we’ll have to invest in the company, but of course we’re looking for co-investors and for governmental support at different levels. At the moment, we’re working for any possible support to realize this project, but we’ve got a lot of interest.
I believe we are well placed in today’s world for our project and ideas. Because aviation, and unfortunately, the military, requires a lot of titanium, and that gives us some good prospects.
Velta Holdings USA
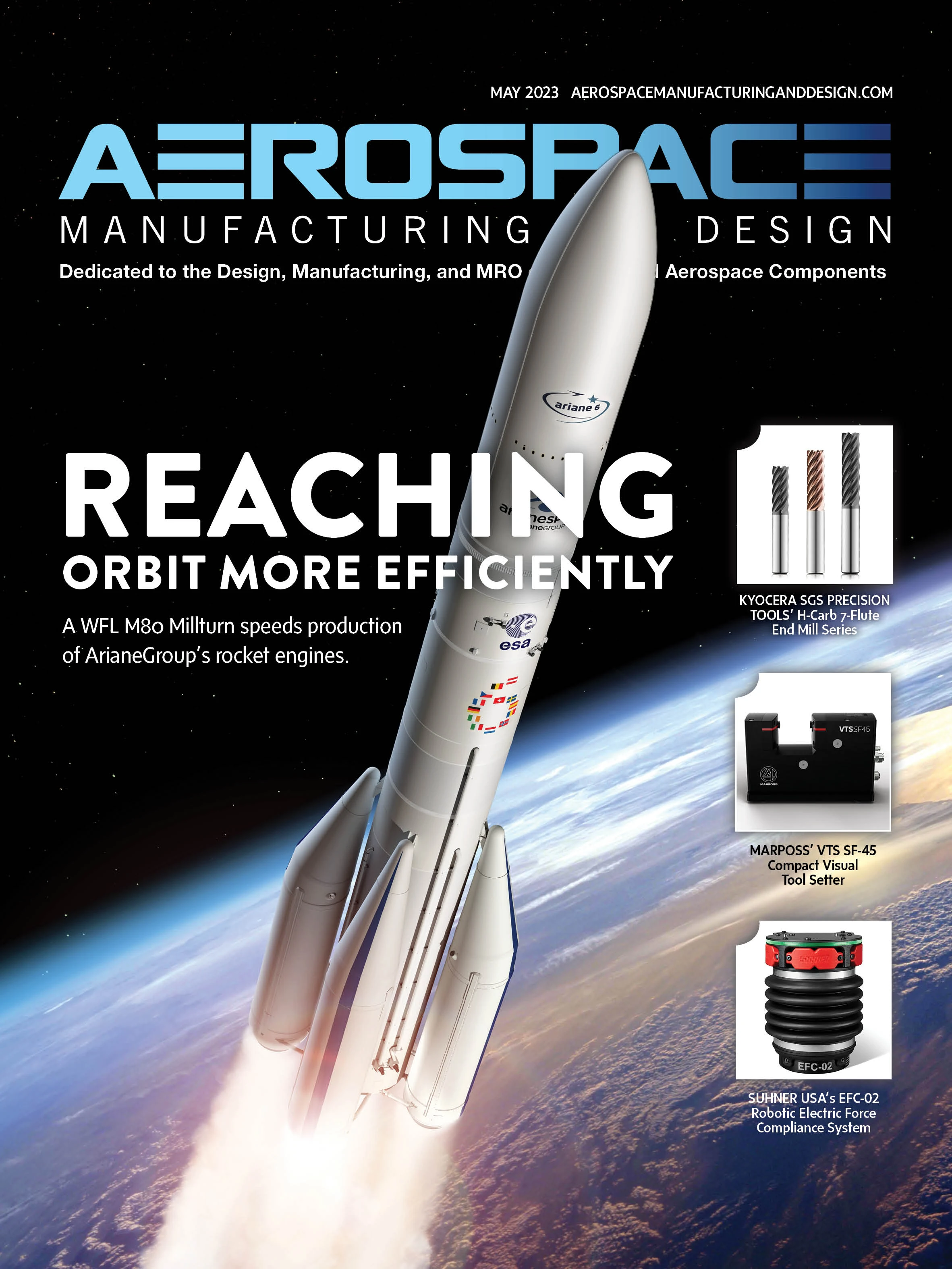
Explore the May 2023 Issue
Check out more from this issue and find your next story to read.
Latest from Aerospace Manufacturing and Design
- Increased efficiency for contour & surface roughness measurements
- Mazak MegaStir will show advantages high-speed friction stir welding at DISCOVER 2025
- Hypertherm doubles warranty length for Powermax series
- Precision measuring systems for free space optical communication
- Down the road: What really is next for electric vehicles?
- Lithuanian airline Jump Air orders 20 ERA aircraft
- Last call for July’s medical manufacturing Lunch + Learn!
- Piper Aircraft receives its largest ever domestic trainer order