
Shortening supply chains has become imperative because the pandemic and current geopolitics have strained manufacturers’ ability to bring products to market. One important supply chain is now virtually single source, making the products that depend on it extremely vulnerable. I refer to the supply chain for rare earth elements (REEs) – the 17 hard-to-pronounce metals essential in semiconductors, high-performance magnets for electric motors, lasers, aerospace alloys, jet engines, microwave filters, high refractive-index glass, and other high-technology products.
While the elements are globally dispersed, they aren’t easily extracted. Most processing plants that refine the ore to obtain the elements are presently found in one country – China, which has decreased production and export during the past decade. For continued industrial production, innovation in electrified transportation, and general national security, we need a reliable, domestic supply of rare earth elements.
USA Rare Earth LLC is one company trying to make that happen. The company already controls and operates the Round Top Heavy Rare Earth, Lithium, and Critical Minerals Project in Hudspeth County, Texas. USA Rare Earth plans to invest more than $100 million to develop a manufacturing facility in Stillwater, Oklahoma, to convert rare earth oxides into metals, sintered neodymium magnets, and other specialty materials. In 2020, the company acquired the only sintered neo-magnet manufacturing equipment in the western hemisphere. It plans to have the necessary operating permits for metal, flake, and magnet operations by the end of 2022, with initial production starting in 2023.
Thayer Smith, president of USA Rare Earth, says, “Our goal with this project is to advance U.S. manufacturing capacity by establishing the first vertically integrated domestic supply chain for rare earth elements, and we are excited to be working in Oklahoma.”
Why Oklahoma?
Brent Kisling, executive director, Oklahoma Department of Commerce, told Aerospace Manufacturing and Design the state’s cost of doing business is among the lowest in the nation. “Utility prices are the least expensive in the U.S., due in part to the abundance of natural gas and other resources,” Kisling says.
“Oklahoma State University is also in Stillwater, so the company will have a pipeline of students to hire, and the potential for research partnerships,” he adds.
REEs are a focus for many of Oklahoma’s economic drivers, including aerospace, automotive, and advanced manufacturing industries.
“We’ve worked closely with a number of large manufacturers looking to make batteries for the electric vehicle (EV) industry, and for them to be able to purchase REEs closer to home is very important,” Kisling notes. “Even though you don’t think of refining metals as part of the EV supply chain, it has become such.”
If successful, USA Rare Earth stands to become a major domestic supplier of the critical raw materials needed for EVs, green energy, defense, and other industries. Let’s hope it’s not the only one. – Eric
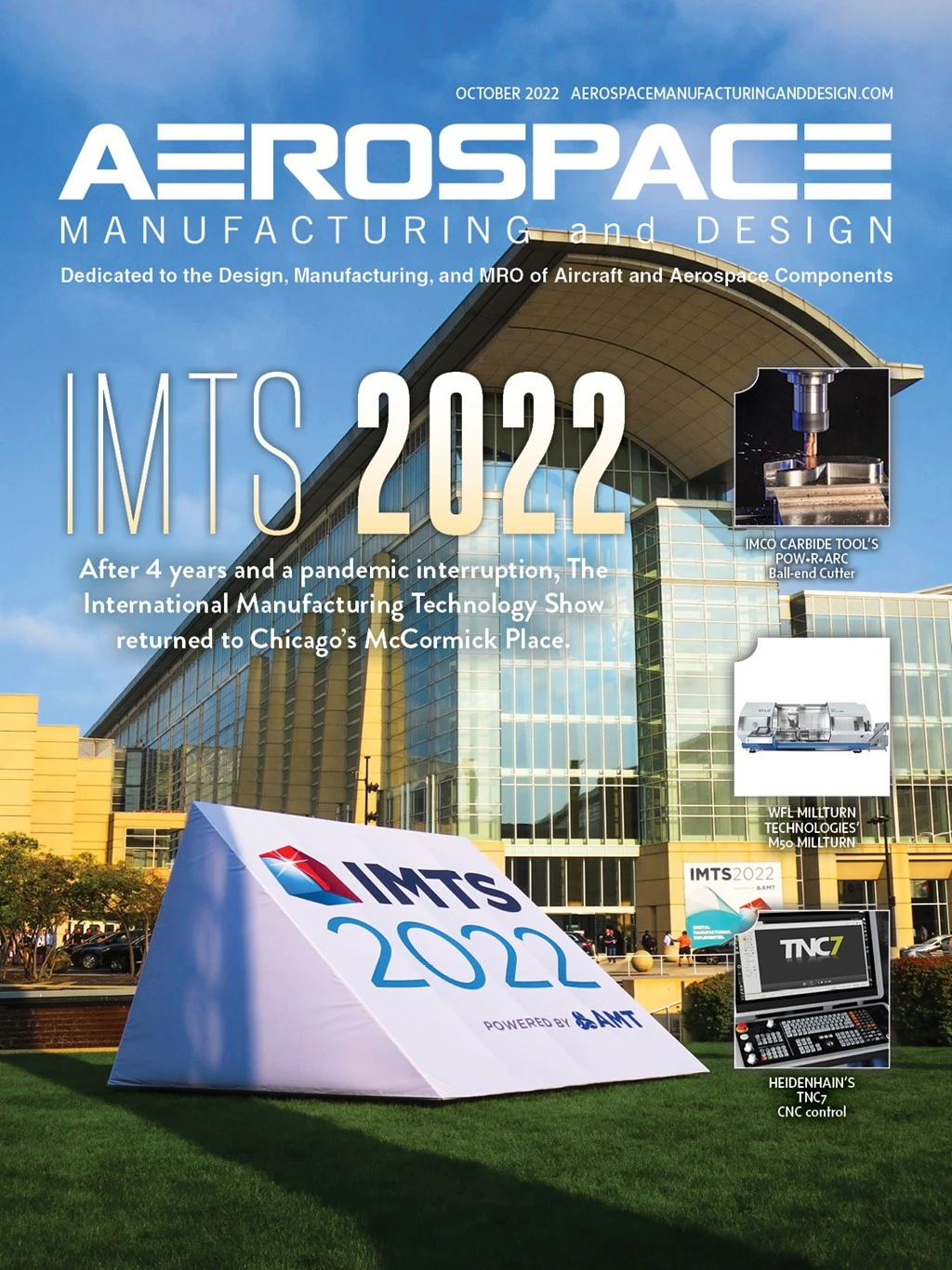
Explore the October 2022 Issue
Check out more from this issue and find your next story to read.
Latest from Aerospace Manufacturing and Design
- Heart Aerospace relocates to Los Angeles
- Fixtureworks introduces Stablelock Clamps
- Piasecki acquires Kaman's KARGO UAV program
- PI Americas’ long-travel XY piezo nanopositioners-scanners
- AAMI project call submission deadline extended to May 12
- Jergens launches cast iron tooling column additions
- Airbus to acquire assets relating to its aircraft production from Spirit AeroSystems
- FANUC America's Cobot and Go web tool