
“Designing antennas for 3D printing
Cathey and COO Rob Smith formed Optisys in West Jordan, Utah, with colleagues who share a combined 60 years’ experience that includes radio frequency (RF) design, satellite communications (SATCOM), mechanical engineering, and additive manufacturing (AM).
An industry void

The ability to consolidate parts with AM sparked the idea to form Optisys, Smith explains. “We had a high degree of intuition that 3D printing would solve many of the problems we fought in our past experiences with antenna manufacturing.”
Traditional manufacturing methods can harm radio frequency (RF) performance. Those problems add time and cost to traditional antenna manufacturing, as there are often 100 or more individual metal components in a conventional design – including hollow, rectangular waveguides that channel electromagnetic energy carrying data – joined together via brazing, plunge EDM, or multiple bolted joints.
Such assemblies can be large and long with unique shapes, creating internal geometric hazards that can interfere with
“Every joint, seam, or fastener creates the potential for a discontinuity that can result in RF losses as the signal travels through the antenna,” Smith says. “Even how tight you make the screws can add a lot of
Smith explains that when a hundred or more parts are joined together, “You have to inspect each piece independently, then put them all together and hope it translates to better overall RF performance. The tolerances of each part have to be very exact, and by the time you integrate so many pieces together, you can have significant tolerance
AM enables systems-engineering

By 3D printing, the engineering team took an antenna assembly with 100 parts and consolidated them into one by designing the product for AM. By viewing an antenna assembly as an integrated structure in which all the parts are combined into one, the team reduced lead times from 11 months to 2 months, cut weight by more than 95%, and lowered production costs up to 25%.
“We did testing to validate our assumptions, took parts to customers to get their responses, and then tested for answers to their questions,” Cathey says.
The team identified that the most convincing value proposition was that the smaller size of their additively manufactured products greatly shortened the overall distance that an RF signal had to travel within the system.
Directional, microwave antennas – used for most satellite and line-of-sight communications, aircraft, and unmanned aerial vehicles – operate in the 1GHz to
“We found a sweet spot for 3D printing where the technology provides many benefits and is also economically advantageous,” Cathey notes. “With our Ka-band
The Ka-band array was evaluated for bench and outdoor RF range performance. Similar designs have passed rigorous vibration testing for military ruggedness. Subsequent Optisys designs have reached up to 50GHz in RF capacity.
Designing for metal AM

Rather than start from a pre-conceived geometry, Optisys engineers begin with the RF requirements for the finished product.
“Because AM promotes parts consolidation, we have the freedom to work toward the goal of optimum RF output rather than derived requirements such as individual part tolerances,” Smith explains. “Passing inspection is a challenge because the critical geometry is internal and can’t be measured directly.”
For the next step, the group’s RF expert, Mike Hollenbeck, develops a microwave simulation using Ansys HFSS software to model the high-frequency electromagnetic field inside the air cavity of the proposed array.
Smith says, “Mike and I go back and forth a bit to identify the air-cavity design that best meets our requirements, then I import that file into SolidWorks to figure out the optimum thickness for the aluminum walls that I’ll wrap around that air cavity to create a design that can be printed as a single metal assembly.”
Smith uses his experience and intuition to create the ideal design topology, adding just enough extra material to form an integrated unit that will print consistently. He also adds support structures where needed, using Autodesk Within, merging the result using SolidWorks and Magics.
“These integrated support structures stabilize the geometry throughout the build, draw the heat away so we don’t get stress concentrations in shrinkage locations, and then provide the entire system with support when it’s in operation,” Smith says.
Benefits beyond the build

The final design is printed with a Concept Laser metal AM machine that uses the LaserCUSING process, a powder-bed-based laser melting of metals.
Aluminum, the preferred material for a build, stands up better than plastics to environmental stresses from ground level to outer space and has essentially the same properties as a solid piece of the same material.
Cathey is optimistic about Optisys’ growth. “Our competitive advantage is the integration of systems engineering, design, and additive manufacturing customized for this niche application. We haven’t pushed the RF boundaries as far as they can go yet, so metal 3D printing will continue to be pivotal in getting us there.”
Optisys LLC
www.optisys.tech
www.conceptlaserinc.com
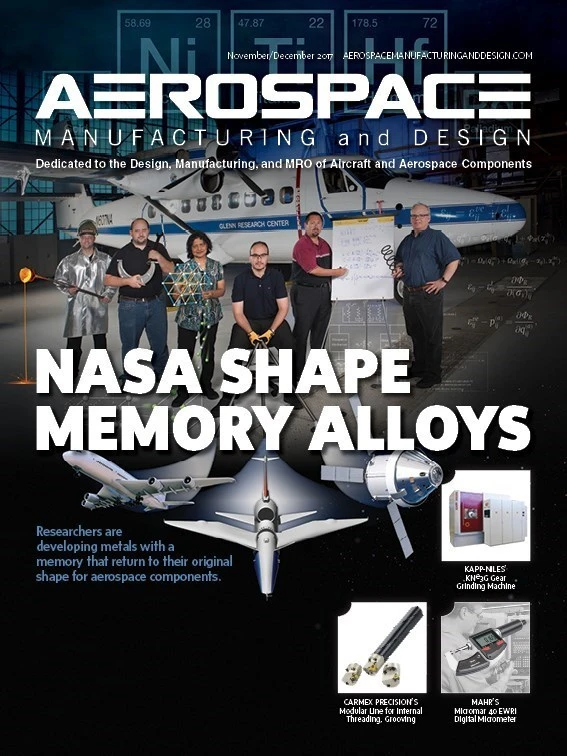
Explore the November December 2017 Issue
Check out more from this issue and find your next story to read.
Latest from Aerospace Manufacturing and Design
- Taiwan’s China Airlines orders Boeing 777X passenger, freighter jets
- Reamer re-tipping extends life of legacy tooling
- Revitalizing the Defense Maritime Industrial Base with Blue Forge Alliance
- Safran Defense & Space opens US defense HQ
- Two miniature absolute encoders join US Digital’s lineup
- Lockheed Martin completes Orion for Artemis II
- Cylinder CMMs for complex symmetrical workpieces
- University of Oklahoma research fuels UAS development