
Developing new fluid control components used to be an entirely manual process. Engineers conceived a design, detailed part and assembly drawings, and fabricated prototype parts. The component was assembled and tested, with the resulting performance compared to the desired specifications. The engineer and technician would then tweak or alter the dimensions of critical parts to align performance of the prototype to design specifications. It was often hit or miss, which consumed substantial time and cost until the prototype’s performance met the specifications. Once satisfied with the performance of the first prototype, several second-generation prototypes were assembled and evaluated. Frequently, their performance differed from the original prototype. More time and money was spent retesting the prototypes with modified or new parts until performance met specification.
In contrast, today’s virtual digital technology takes the guesswork out of the equation, greatly reduces the design and development timeline, and minimizes related costs in new product creation. Using digital iterative design accelerates the design process, controls costs, and yields a substantially better valve in performance and value. By the time a prototype is built, engineers are confident its performance meets spec or is close.
Valcor Engineering uses a virtual digital process known as model-based systems engineering (MBSE) that lets engineers execute a complex electromechanical systems design by creating a digital twin of the valve. MBSE can design and evaluate the performance of fluid control components before a single part is fabricated.
Historically, sophisticated mathematical modeling and simulation capabilities required high performance computing (HPC) systems such as Cray supercomputers available only to a few national labs, academic research institutions, and Fortune 500 companies. Today, the tools that enable MBSE are readily available to most companies; Valcor relies on these tools to design and create new fluid control components for demanding applications.

The design process
To create a new solenoid valve, Valcor engineers start by using SolidWorks CAD/CAE 3D solid modeling software by Dassault Systèmes. The software’s 3D modelling feature establishes the critical part dimensions the new valve requires and evaluates how they all fit together.
Once the parts are designed, engineers use Ansys finite element analysis (FEA) software for evaluation. The FEA process for each critical part of the assembly ensures that it’s robust and appropriate for service in the new valve. FEA identifies areas of unacceptable stress, as well as areas with dimensional weaknesses. The FEA process is used for thermal analysis and structural evaluation including stress, deflection, and distortion. Simultaneously, MathCad is used to perform preliminary vibration analysis and analyze a subsequent FEA model.
The engineering team then uses FEA to perform fatigue analysis on each part using the solid model generated by SolidWorks. Fatigue analysis determines the usable life of each part. The information derived can then be used to predict the need for periodic maintenance or replacement.
Several other tools within the Ansys product family assist in the design process. One tool for electromagnetic simulation is EMag. Using this module allows the engineer to virtually simulate the electromagnetic and electromechanical forces in the solenoid design by evaluating pull-in and response time characteristics related to material selection and part geometry. Response time is how fast the valve moves from one state to another. The module also evaluates magnetic flux related to bobbin and coil design. Valcor’s comprehensive database of analytics provides engineers with a high level of confidence that the new coil designs meet performance specifications prior to prototyping.
Computational fluid dynamics (CFD) software models flow characteristics of the new design. Ansys Fluent and CFX modules integrate the individual parts into a virtual working model of the new valve, allowing engineers to evaluate its theoretical performance against the customer’s specifications. Tweaking subcomponent tolerances and dimensions and evaluating performance changes yields a design that moves to the prototype stage.

Evaluation and modification
Valcor uses MATLAB/Simulink to further enhance the digital twin’s evaluation. These tools enable the engineering team to model response time, forces acting on critical components of the valve, pressures, flow rates, and determine the acceleration of a particular valve component. Simulink collects the data to analyze the design, and MATLAB controls the virtual model’s performance based on data inputs.
Once engineers are satisfied with the digital twin’s performance, they release the drawings for fabricating the parts needed to build prototypes. The prototype’s performance is tested and compared to the theoretical performance of the digital twin. Here, test results are plotted against the theoretical performance of the valve. By making changes to the critical part dimensions and profiles in CAD and running the simulation model again, the design moves closer to meeting spec. With relatively few iterations of the physical hardware, a design that meets specifications can be arrived at quickly, cost effectively, and moved into production with minimal effort.
As part of the value engineering process, Valcor also uses the digital twin to optimize manufacturability of the valve. Design changes can make the valve easier to assemble without affecting performance, minimizing the need for special fixtures and tools to efficiently build the production valve. Once the valve design performs to the customer’s specification, final drawings are released.
Valcor’s manufacturing team can generate computer aided manufacturing (CAM) programming for each part used in the valve assembly. Computer numerical control (CNC) programmers will review the programming, and occasionally modify it to suit the specific needs of the CNC machining centers. However, using the MATLAB-generated programming eliminates the task of developing from scratch the CNC programming for each part from scratch. The result is the manufacture of quality parts that meet print and are ready for assembly in the final product.
Once in production, Valcor relies on test data to create a feedback loop to the digital twin, which allows them to study the valve’s performance in its intended use, affirm the design’s suitability, and make modifications when application parameters change. The engineers anchor the theoretical model to the test data, helping them refine their tools that can be carried over to future analysis and product design.
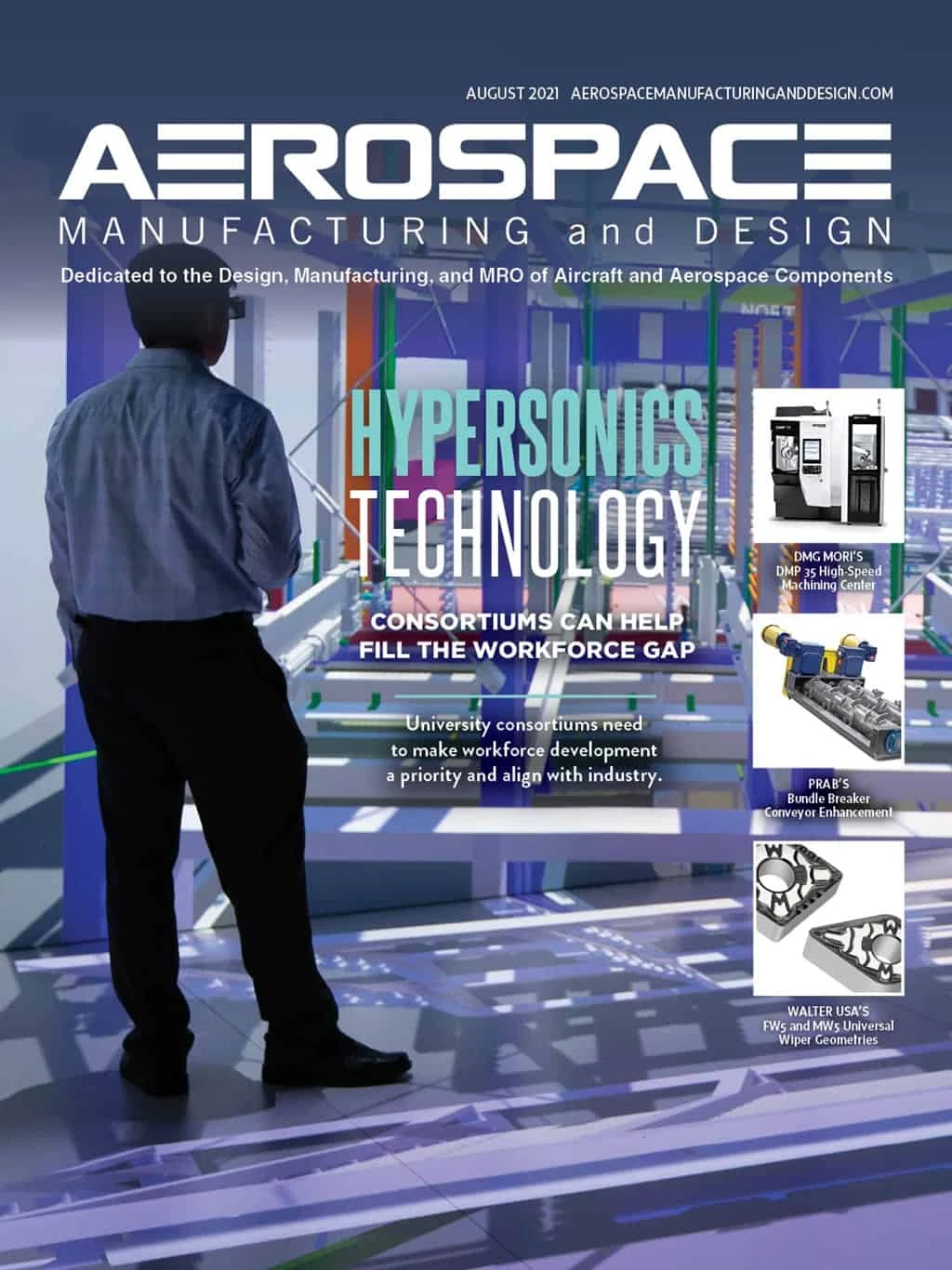
Explore the August 2021 Issue
Check out more from this issue and find your next story to read.
Latest from Aerospace Manufacturing and Design
- Lockheed Martin completes Orion for Artemis II
- Cylinder CMMs for complex symmetrical workpieces
- University of Oklahoma research fuels UAS development
- Motorized vision measuring system
- Everyone's talking tariffs
- Boom Supersonic to launch Symphony engine testing in Colorado
- Next-generation precision measurement solution
- #60 - Manufacturing Matters: What's ahead in manufacturing in 2025?