
StarHagen, a provider of production parts for aerospace companies, joined the Velo3D Contract Manufacturer Network with the purchase of a Sapphire printer. The system’s calibrated to print in Inconel 625, a nickel-based superalloy designed for high-strength and to resist high temperatures and corrosion.
StarHagen specializes in manufacturing with extreme precision for prototype and production volume manufacturing. The company operates CNC machines capable of 4- and 5-axis machining, providing complete turnkey parts for customers.
Velo3D also announced Pratt & Whitney, a Raytheon Technologies business, acquired an end-to-end solution to evaluate the Sapphire printer for manufacturing production jet engine components. This is the first Sapphire printer to be located at Pratt & Whitney; it previously used Velo3D’s Contract Manufacturer Network to produce printed and finished parts.
Pratt & Whitney and Raytheon Technologies are experienced users of additive manufacturing (AM) with extensive knowledge across various platforms and applications. Raytheon Technologies’ commitment includes seeking small- and medium-enterprise manufacturers’ involvement in more than 50% of its requests for quotes on products manufactured using additive technologies, seeking to simplify and accelerate the procurement process of AM parts.
The company’s Sapphire XC printer is calibrated to print in Inconel 718, made possible because of print preparation software, the Sapphire printers, quality assurance software, and underlying manufacturing processes. The system uses known recipes to achieve desired geometries without using supports, monitoring the build process layer-by-layer for high quality.
Patch antennas for next-gen satellites

3D Systems will collaborate with Fleet Space Technologies to produce RF patch antennas for use on its Alpha satellite constellation. Fleet Space’s unique design and the expertise of 3D Systems’ Application Innovation Group (AIG) allowed them to architect a complete additive manufacturing (AM) solution including process development and bridge production on its DMP Flex 350. This enabled moving from Fleet Space’s existing RF patch design to small batch production in three weeks. Fleet Space is bringing a DMP Flex 350 printer into service at its headquarters in Beverley, Australia, moving production of patch antennas in-house. The printer will create RF patch antennas for the Alpha satellites operating in a constellation in low Earth orbit as part of Fleet Space’s ExoSphere initiative.
Fleet Space’s engineering team designed the antenna to meet size, weight, and performance requirements while minimizing the need for post-processing. 3D Systems’ AIG developed print processes to produce the antenna on its DMP Flex 350 printer in two different materials – LaserForm AlSi10Mg and Al6061-RAM2. The vacuum chamber architecture of the DMP Flex 350, which maintains a low oxygen environment (<25ppm), was critical. Argon gas consumption is heavily reduced, and the vacuum chamber architecture produces a good surface finish with fine feature detail, minimizing signal losses. Additionally, the DMP Flex 350 also includes 3DXpert software supporting the AM workflow – from design to post-processing, to transition from a 3D model to successfully printed parts.
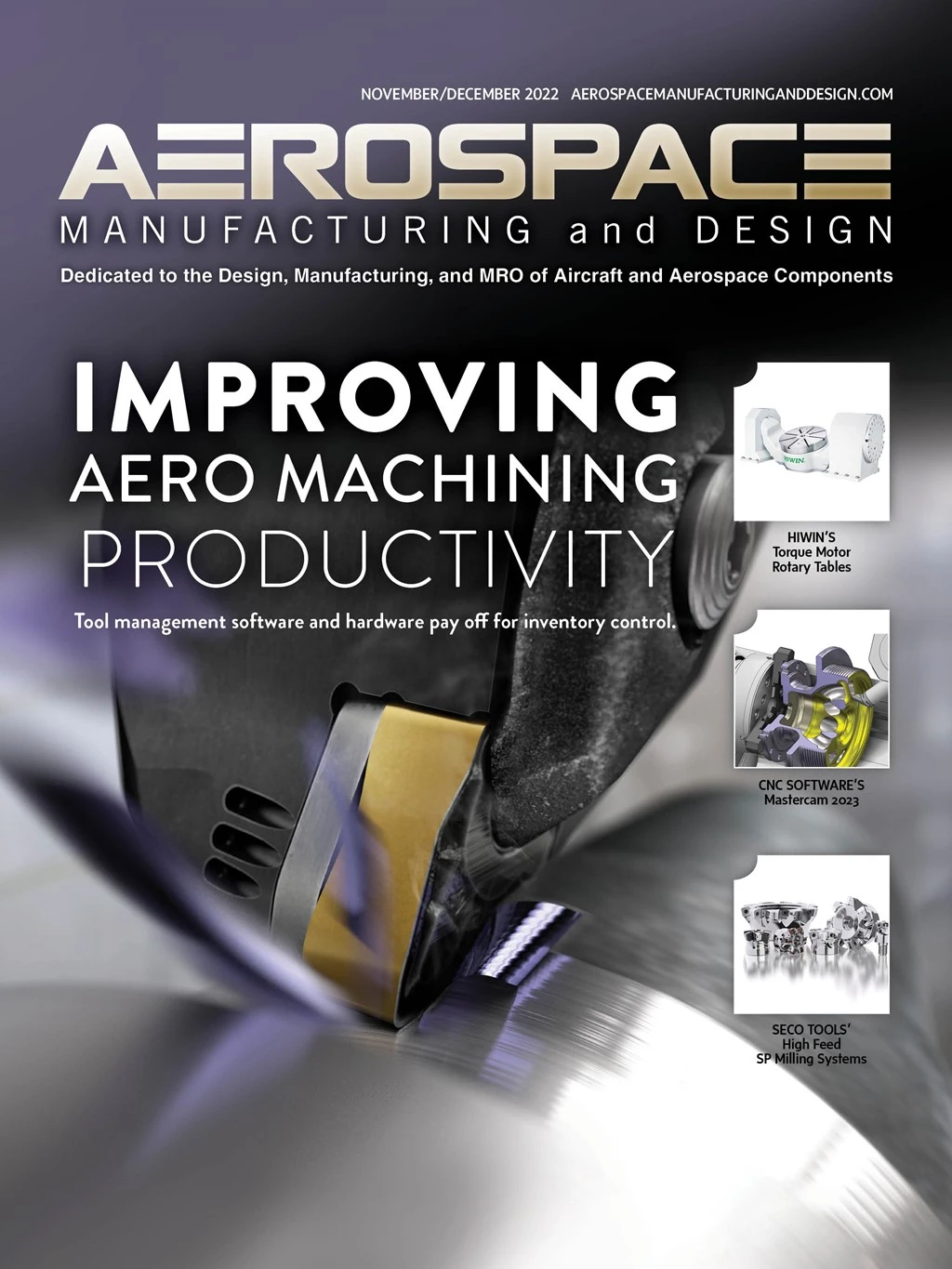
Explore the November December 2022 Issue
Check out more from this issue and find your next story to read.
Latest from Aerospace Manufacturing and Design
- Revitalizing the Defense Maritime Industrial Base with Blue Forge Alliance
- Safran Defense & Space opens US defense HQ
- Two miniature absolute encoders join US Digital’s lineup
- Lockheed Martin completes Orion for Artemis II
- Cylinder CMMs for complex symmetrical workpieces
- University of Oklahoma research fuels UAS development
- Motorized vision measuring system
- Everyone's talking tariffs