
Less than 72 hours before Labor Day in 2014, a jet bridge at the Honolulu International Airport (HNL) collided with a Japan Airlines (JAL) Boeing 787 Dreamliner, damaging an engine cowling and disabling the plane. Far from their home station, JAL’s maintenance, repair, and overhaul (MRO) team faced a tight deadline to remove the aircraft. Losing time and money, the team contacted UPS to transport a 3,500 lb replacement cowling that waited 2,600 miles away.
The challenge
JAL was one of the first airlines to fly the lightweight, fuel-efficient 787 Dreamliner, so spare parts – especially parts that weigh nearly two tons – weren’t readily available. Throw in the holiday weekend, and a solution seemed impossible.
“In most cases, we would have a spare aircraft available to substitute for the grounded one. But at a foreign airport, we were forced to cancel the flight,” says Takashi Ogata, logistic management staff manager for JAL Engineering.
“This kind of aircraft downtime means a significant revenue loss from flight schedule disruptions, cancelled flights, and additional expenses such as layover fees, hotel accommodation, and food and beverage expenses for passengers,” Ogata says. “But what worried us most was losing the confidence of our valued customers.”

On Saturday, Aug. 30, 2014, one day after the plane was grounded, JAL’s MRO team located a replacement cowling at a UTC Aerospace Systems facility in Chula Vista, California. Now, the team had to figure out how to get the cowling to Honolulu. Ogata called Yuichiro Asari, JAL’s UPS account executive in Tokyo. The clock was ticking as HNL wanted the plane removed within seven days.
Critical communication
Asari and Sachiko Wakui, UPS global Japanese sales manager, went to work. Although JAL was a fairly new customer to UPS, luckily, the situation wasn’t.
“We’d been shipping spare parts for [JAL] for about a year, but moving the cowling on such a tight deadline was a much bigger job,” Wakui says.
JAL’s MRO team had to work with UPS to prioritize the project and provide precise measurement and weight data for transporting the cowling and detailed delivery instructions for speedy repair.

“The size of the cowling and requirements to move it as soon as possible made this challenging,” says Mark Lombardo, general manager for UPS Supply Chain Solutions. The first step was to secure a lift to Hawaii. Then, the UPS crew could arrange ground transportation.
UPS’ charter group knew that a nose-loading Boeing 747 was the best option for transporting the cowling.
Early in the morning of Friday, Sept. 5, 2014, one day short of the deadline, a flatbed truck transported the engine from Chula Vista to the San Diego International Airport (SAN). The 16-mile drive required special permits and an escort vehicle for the oversized load.
“Our team has deep experience working charters. We knew what to expect when the ground transportation was scheduled,” says Lombardo.
For UPS to arrange this transportation, it needed urgent information about the cowling from JAL’s MRO team. Lombardo says understanding the dimensions were just as vital for the ground move as they were for the air. Ground transportation required a special trailer and several permits, there were curfew hours during which the load would not be allowed on the road, and UPS had to follow a prescribed route. UPS employees worked under these strict requirements for an on-time delivery, communicating constant updates to JAL.
Special delivery
UPS worked with UTC to understand the cowling’s design specs for transport and to insure the cowling was built properly on the pallet.
“There could not be any negotiation with this move,” Lombardo says.
Following a successful ground transport, workers at SAN loaded the cowling onto the special Boeing 747 and departed to Honolulu.

The next morning, JAL’s MRO team stood by when the 747 charter landed in Hawaii to install the cowling. The newly repaired 787 Dreamliner then departed Honolulu for Narita International Airport in Japan.
UPS then shipped the damaged cowling by ocean freight to the U.S. mainland for its long road trip for repairs at a UTC Aerospace Systems facility in Alabama.
“Our team acted quickly, relying on our vast multi-modal expertise,” Wakui says. “It was a delicate operation that put our logistics skills and ingenuity to the test.”
“Having an experienced MRO team involved was critical,” says Lombardo. “We also believe our strong relationship with JAL and UTC were key.”
Japan Airlines
UPS
About the author: Arielle Campanalie is an associate editor for AM&D and can be reached at 216.393.0240 or acampanalie@gie.net.
Get curated news on YOUR industry.
Enter your email to receive our newsletters.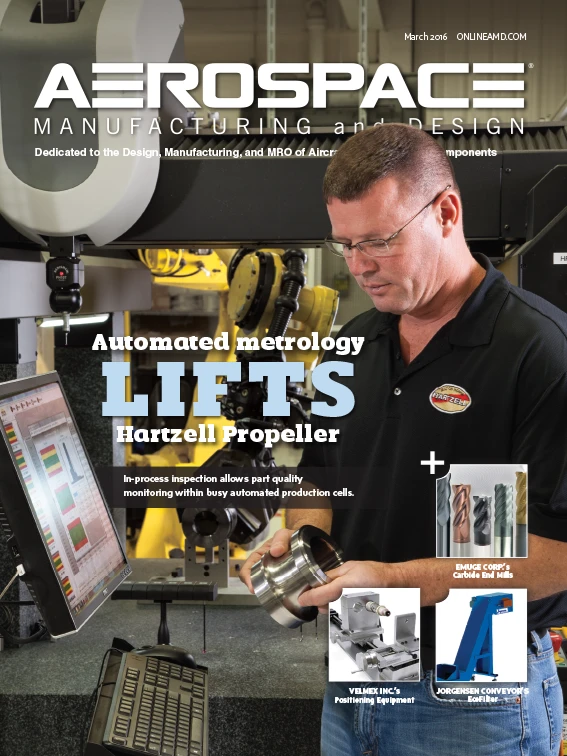
Explore the March 2016 Issue
Check out more from this issue and find your next story to read.
Latest from Aerospace Manufacturing and Design
- Address the challenges of machining high-temperature aerospace components
- Elevate your manufacturing operations with April’s Manufacturing Lunch + Learn
- America Makes announces IMPACT 3.0 Project Call worth $4.5M
- Updated parting and grooving geometries from Sandvik Coromant
- AIX showcases the future of air travel
- Sunnen Products' PGE-6000 gage
- #41 Lunch + Learn Podcast - SMW Autoblok
- Revolutionizing aircraft design without sacrificing sustainability