
The aerospace industry significantly contributes to global carbon emissions and manufacturers are required to do their part to reduce the industry’s carbon footprint. There are measures such as composites, recyclable materials, and additive manufacturing (AM) to support the cause.
Another manufacturing process, deep drawing, can help aerospace manufacturers with sustainability goals. Deep drawing offers many benefits including limitations on material waste. Alpha Metalcraft Group (AMG) employs the environmentally friendly process for producing aerospace components.
“Deep drawing is environmentally friendly with a very limited amount of material waste,” says Alec Searle, AMG’s CEO. “Machining results in large amounts of scrap that need recycling or proper disposal.”
Precision parts
Deep drawing produces complex geometric and highly precise shapes quickly and efficiently. The process offers several advantages compared to machining, especially when machining hard and exotic metals that are produced in low volume with relatively long cycle times. Machined products are often more expensive and not as strong as products manufactured with deep drawing due to their uniform grain structure.
Deep drawing stretches metal beyond its elastic limits – but not beyond its plastic limits. No heat is applied to the metal during the drawing process to make it more ductile, as it’s stretched at ambient temperature enough to remain in its stretched shape but not rupture or tear beyond its plasticity.
Tooling with a punch and die starts the process. The punch and die are designed and produced to the necessary geometry to yield the desired part geometry.
A metal blank is cut (pierced or waterjet cut) and is traditionally circular in shape with the part’s desired wall thickness. It’s large enough in diameter to accommodate the part’s draw depth (height).
A single draw is performed to achieve the desired flanged can depth without rupturing or thinning the blank. If a single draw isn’t sufficient, a secondary or tertiary draw may be performed.

On many occasions, thermal heat treatment of the metal – an anneal process – is required to allow ductility back into the material for further draws. A thermal heat treatment process is sometimes required to further harden the part.
Final machining, such as turning and milling, is frequently required to yield proper geometry and tolerance and remove the flange and bottom of the can if desired.
“Deep-drawing parts are made to exacting tolerances,” Searle says. “It’s also a repeatable process, so there’s no need to reset or sharpen tools. Even for harder materials such as copper and superalloys, it’s a superior metal forming process.”
Benefits
Deep drawing offers many benefits such as delivering tight tolerance and complex-shaped components economically.
“No other process for shaping and stretching metal matches the speed of deep drawing,” Searle says. “The process involves a mechanical or hydraulic press, and draw speeds vary based on material and complexity of the shape. The speed helps us deliver products with the urgency customers demand.”
Another advantage is the ability to produce heavy walls. Hydroforming is a similar, cold-working metal forming process using different types of tooling and presses. While it can produce highly complex geometries, it can’t produce heavy walls or match the depths of deep drawing. Due to the advancements in materials and equipment, deep drawing can now draw heavier walls and deeper depths.
“Deep drawing allows us to manufacture large and heavy components with exotic metals,” Searle says. “Most of the time no additional processing is needed. Machined parts need some additional processes to match the quality of a deep drawn part. That’s a significant reduction of manufacturing time.”
The challenge many manufacturers find is producing precise components in high volume.

“Deep drawing produces parts of complex geometries, but it’s also a very efficient process and can produce components in large quantities,” Searle says.
Deep drawing’s limitation of material waste is another critical benefit, especially when sustainability objectives are a top priority.
Components produced with DD
Piccolo ducts, klystrons, and magnetrons are among the products AMG produces with deep drawing.
Piccolo ducts, bleed air ducts, and exhaust ducts are found on commercial and military airplanes and are associated with high-pressure ventilation and exhaust ducting. Piccolo ducts are a central element for supplying ventilating air into an aircraft cabin. They’re lightweight and have low installation space volume. Piccolo ducts are often used as an anti-ice tube for the wings of an aircraft.
Magnetrons are power tube components used in high and medium applications. Magnetrons were used in early radar systems and now are used in radar transmitters and mostly for weather radar in civil aircraft. Components used in Klystrons and thyratrons are also deep drawn products.
Outlook
According to a September 2023 report, the outlook for the deep drawing press market is expected to grow by a 7.4% compound annual rate until 2030 due to advancements in technology and increase in consumer demand for presses and parts made with deep drawing. According to the report, “the increasing number of applications with the growing awareness of the benefits of using hydraulic deep drawing presses” is contributing to growth.
While hardly a new process, producing complex configurations with exotic and customary metals makes deep drawing extremely valuable and important, especially for the exacting demands of customers in the aerospace markets.
NEWS AND PRODUCTS
Thread checker with inspection capabilities

ThreadChecker is a non-contact application-specific sensor for rugged, reliable verification of thread presence or absence in electrically conductive material. ThreadChecker is a teachable eddy current inspection tool, used for thread detection, material sorting, plating presence, and absence of heat treatment. Any physical property difference relating to material conductivity is readily detected.
Consisting of a single electronics module compatible with most probe/material combinations, it can check threads regardless of part cleanliness.
With proven eddy current technology at its core, ThreadChecker is designed specifically for in-die use. It features four internal probes, ranging from 4mm to 10mm and two external probes – 6mm and 8mm. Available with a DIN rail mounting option, ThreadChecker is CE-compliant and features IP-67 rated probes and electronics.
ThreadChecker is available with switched and analog outputs. With the switched output option, the sensor is wired to a PLC or other controller, programmed to alarm when no thread is detected. As an alternative, users can monitor the analog voltage and program the PLC or other control device with limits suitable for the application.
Universal Robots’ strong end to 2023

Universal Robots reported Q4 2023 revenue of $103 million, up 21% on Q4 2022. The quarter was the company’s largest revenue quarter to date. 2023 annual revenue was $304 million, down 7% from 2022.
In 2023 Universal Robots experienced strong demand for the first of its heavy payload cobots, the UR20, particularly for palletizing and welding applications. In November it launched the second model in the new series of cobots, the UR30, which offers new automation possibilities. The UR20 and UR30 represented 30% of Q4 revenue.
Universal RobotsRemote monitoring and control of industrial robots

Olis Robotics announced a partnership with Kawasaki Robotics Inc. to offer customers the ability to restart production faster, reduce troubleshooting and downtime costs up to 90%, and gain access to expert support quickly.
Olis users connect directly to their robots through an on-premises device via a secure connection, avoiding the risks and complexities associated with cloud-based systems. The system handles multiple SKUs of unstructured products and is equipped with remote error recovery software alerting users when the robot unexpectedly stops, and when picking or placing a part fails. After a system failure, the Olis runs a tool inspection routine and performs remote error recovery, allowing the robot to resume its cycle and get back to work.
Kawasaki Robotics
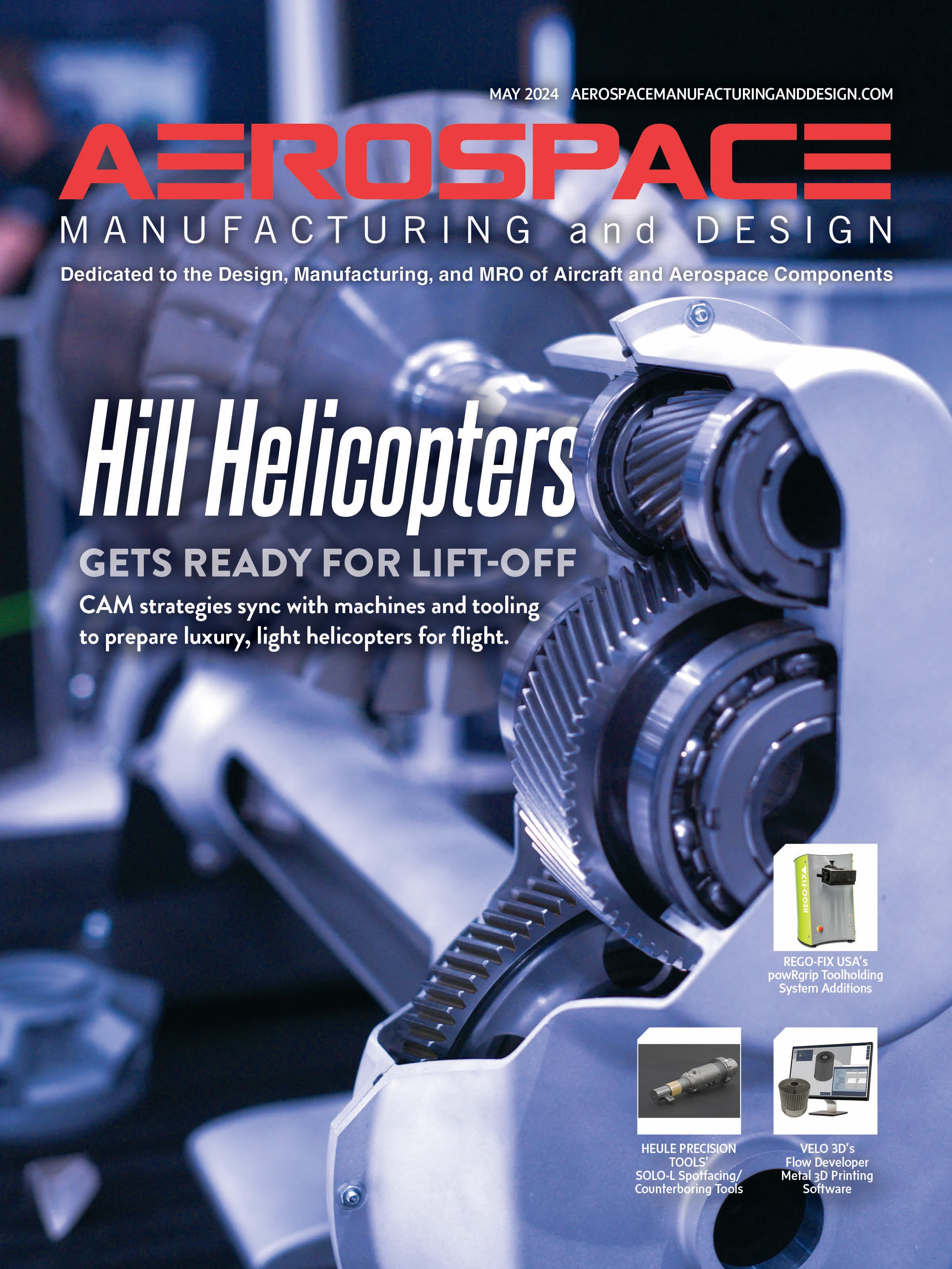
Explore the May 2024 Issue
Check out more from this issue and find your next story to read.
Latest from Aerospace Manufacturing and Design
- NASA-supported technology outfits Venus Aerospace hypersonic engine
- To the Smoothest Surfaces, Finishes, and Beyond | Okuma GA26W
- Extraordinary Starts Where Limits End | Okuma
- Satair, Champion Aerospace sign multi-year distribution agreement
- EMUGE-FRANKEN USA expands N. American solid carbide drill program
- AURA AERO unveils INTEGRAL R to the US market
- Creform Tite-Space AGV fleet
- Cyient Group, Deutsche Aircraft finalize multi-year contract