Engineers and managers use measurement data collected by aerospace machinists and inspectors on shop floors and quality labs across the globe to satisfy customer requests, comply with Federal Aviation Administration (FAA) requirements or other government mandates, and monitor product quality and manufacturing performance.
However, manually collecting and retaining dimensional data is inefficient, can lead to costly errors, and carries expenses associated with storing and maintaining paper records for product life as required by the aerospace industry. Therefore, aerospace manufacturers are steadily reducing paper records in favor of quality data management software that can capture and store information digitally.

Digital thread
Aerospace relies heavily on its extended supply chain to produce quality products, but the massive volume of parts, part numbers, and suppliers involved in building aircraft makes it difficult to track products. Aerospace manufacturers highly support improving the supply chain so they can improve part quality, profit margins, and the overall safety of air travel.
This can be achieved by adopting the digital thread – digital information that can be tracked through every part’s life cycle. Quality data management software plays a significant role in an enterprise’s ability to support the digital thread. Software contains essential information such as the part’s tolerances and as-measured values. Process capability statistics calculated from these measurements can generate performance charts for the manufacturing process. When necessary information isn’t accessible to those who need it, or to other software that can use the data, the extended enterprise is not being as efficient as it could be.
Manufacturers who implement the digital thread must choose interoperable software that uses a communication standard such as quality information framework (QIF).
Aligning QIF standard
Released and accepted as an ANSI standard in 2013, QIF has been submitted by the Digital Metrology Standards Consortium (DMSC) to ISO/TC 184/SC 4 Industrial Data as ISO/DIS 23952. Once accepted, the standard should become more widely adopted.
Adopting the QIF standard should give aerospace manufacturers clearer insights into all parts and products received. QIF stores product information in documents written in extensible markup language (XML). Since XML is commonly used, QIF documents can be easily transferred across tiers of suppliers to the aerospace manufacturer through their enterprise resource planning (ERP) software, all of it potentially different.
However, when software application developers create proprietary communication protocols, or if private organizations create their own standards, the entire industry takes a step back. Information is no longer shared effortlessly. Because organizations can’t agree on which protocol to adopt, the enterprise eventually resorts to spreadsheets and PDFs to share information. If a proprietary format is agreed upon, it becomes costly to adopt since it was developed by private organizations that have their own interests in mind.
QIF, however, is free. The XML format is easily adoptable and can allow companies to choose applications that best suit their needs rather than applications that only work with a particular machine or software.

Tracking serialized parts
For serialized aerospace parts, conventional characteristic naming systems, including balloon IDs, are being supplemented with universally unique identifiers (UUIDs), a standardized format ISO/IEC 9834-8:2005. Conventional characteristic naming systems are being supplemented because they cannot provide unique identifiers across the enterprise.
QIF results files are serialized and ideal for long-term archiving and retrieval (LOTAR) (http://lotar.prostep-ivip.org), eliminating problems related to managing, tracking, and locating measurement data for specific parts or characteristics.
For example, a database search for “Diameter_28,” would return thousands of results for that characteristic from numerous parts and assemblies. However, a characteristic search in one or many QIF documents finds a specific UUID that returns immediate and exact results for an ID that will not be duplicated.
Close the loop
In a machine cell, a QIF document containing measurement results and statistics can feed information back to a machining center for controllers to make tool offsets, ensuring high-quality manufacturing.
Machine tool controllers are becoming more intelligent every day, and many can manage tool wear, estimate cycle time, and report machine condition. However, all these functions require information. To adaptively compensate for tool wear, the information needed by the machine tool controller must be actionable, which, in this case, is measurement results and statistics. For example, measurement data coming from a coordinate measuring machine (CMM) measuring newly machined parts can be calculated into useful process capability statistics by the quality data management software. The machine tool controller can then read the information from a QIF results and statistics document to make necessary corrections on the next part automatically. Closed-loop manufacturing keeps costs low, parts in tolerance, and process capability high. It also frees up operators to do other tasks and only requires them to get involved with tool offsets during critical situations.

Manufacturing future
The future of manufacturing lies in the smart factory – more data, more sensors gathering the data, and a more interconnected manufacturing space.
A smart factory requires aerospace machine and software suppliers to be able to communicate and share part and measurement data with one another by leveraging QIF and using the digital thread. Part quality can be confirmed, and manufacturers can be more responsive to real-time issues impacting delivery.
Manufacturing plant interconnectivity between different software applications and machines, and information sharing with partners and suppliers through the entire supply chain, will be integral to profitable aerospace manufacturing.
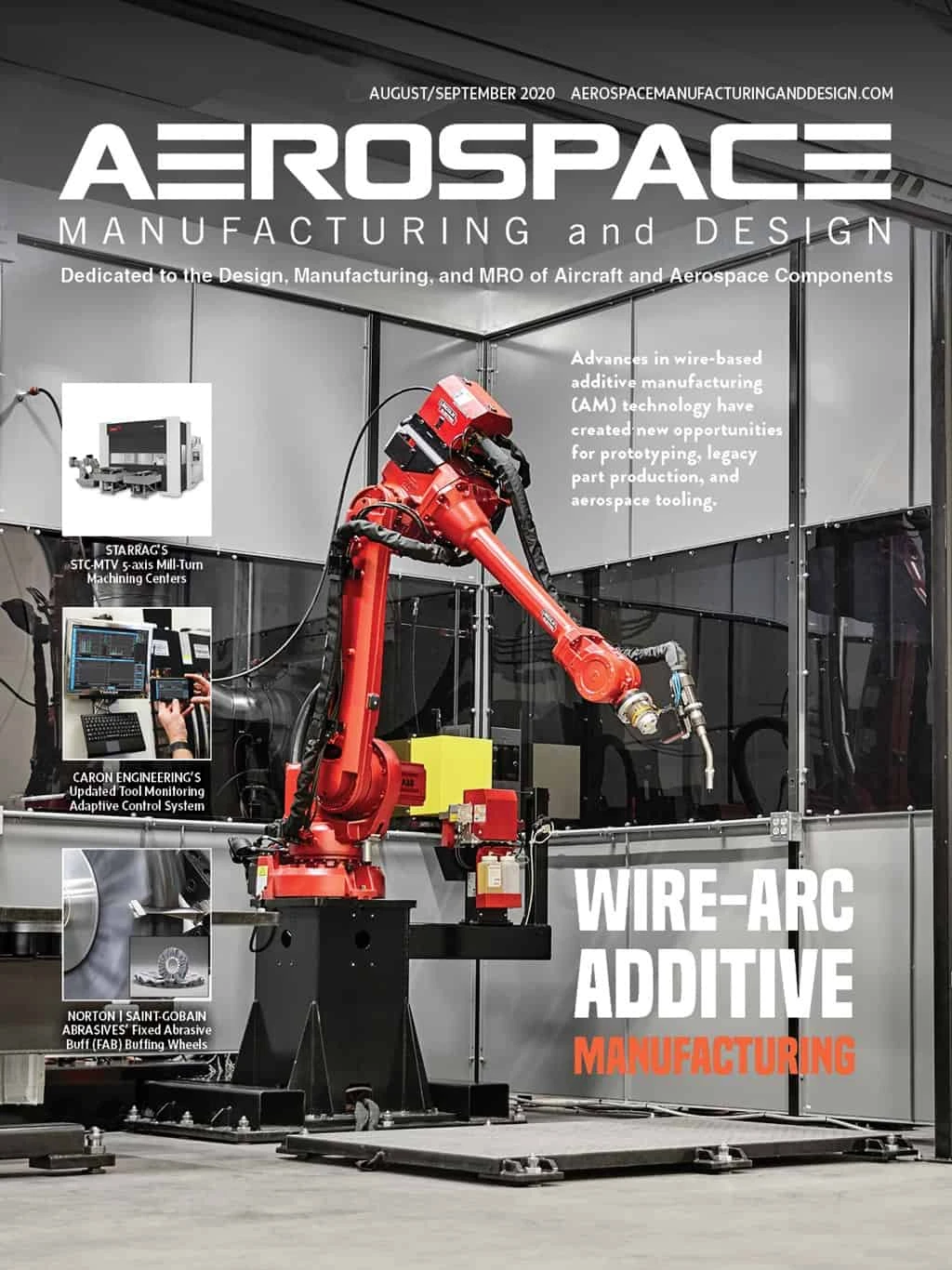
Explore the August September 2020 Issue
Check out more from this issue and find your next story to read.
Latest from Aerospace Manufacturing and Design
- Safran Defense & Space opens US defense HQ
- Two miniature absolute encoders join US Digital’s lineup
- Lockheed Martin completes Orion for Artemis II
- Cylinder CMMs for complex symmetrical workpieces
- University of Oklahoma research fuels UAS development
- Motorized vision measuring system
- Everyone's talking tariffs
- Boom Supersonic to launch Symphony engine testing in Colorado