
Danville Metal currently produces parts for commercial aerospace, defense, and stationary power generation. Their customers demand high quality, tight tolerance parts often constructed of expensive and exotic materials, such as Inconel. With the use of AutoForm Forming R8, they were able to streamline the process, shrink lead times, and save costs by eliminating production issues in advance.
First, Danville was able to optimize a process where the tools had already been built. A four-operation process, which included an annealing station, was reduced to a two-operation process. This was made possible by quick simulation turnaround of different processing strategies. Once the tooling was changed, the time to manufacture the part shrunk from 2 weeks to 2 days. In the future, difficult decisions such as whether an anneal, restrike, or secondary processing are required can be made with confidence.
Second, lead-time was able to be reduced. This was essential when spring-back compensation was required. According to Danville’s engineers, a single operation used to take one to two days to compensate and generate new tools. By utilizing simulation, this time was reduced to 5 minutes. This time saver was essential, because part tolerances are regularly measured in thousands of an inch, rather than hundredths of an inch. The flexibility allotted by these shorter timelines allows for closer adherence to tolerances. The compensations were tested with physical tooling, shown in the image above.


Third, the ability to quickly simulate and optimize different blank sizes/shapes/locating techniques greatly reduced the amount of trial blanks used during tryout. Considering the material utilized, individual blank shape iterations reached upwards of $4,500. These shape change results saved both time and money during the initial design, and also for re-designing current processes to be more efficient. Shown in the image below is the workflow used to generate a blank shape for the part. At first a very basic shape was used. Further in, the blank was optimized with simulation.
After adopting AutoForm R8 software just over a year ago, Danville has proven it useful in helping to reduce lead times, generate quotes with higher confidence and accuracy, re-design current processes, and strategically design new processes much more efficiently. Following their company mission, Danville Metal continues to advance the industry by using “state-of-the-art technology… to manufacture parts in a timely and cost-effective manner from process planning to delivery.”

AutoForm Engineering https://www.autoform.com
Danville Metal http://danvillemetal.com
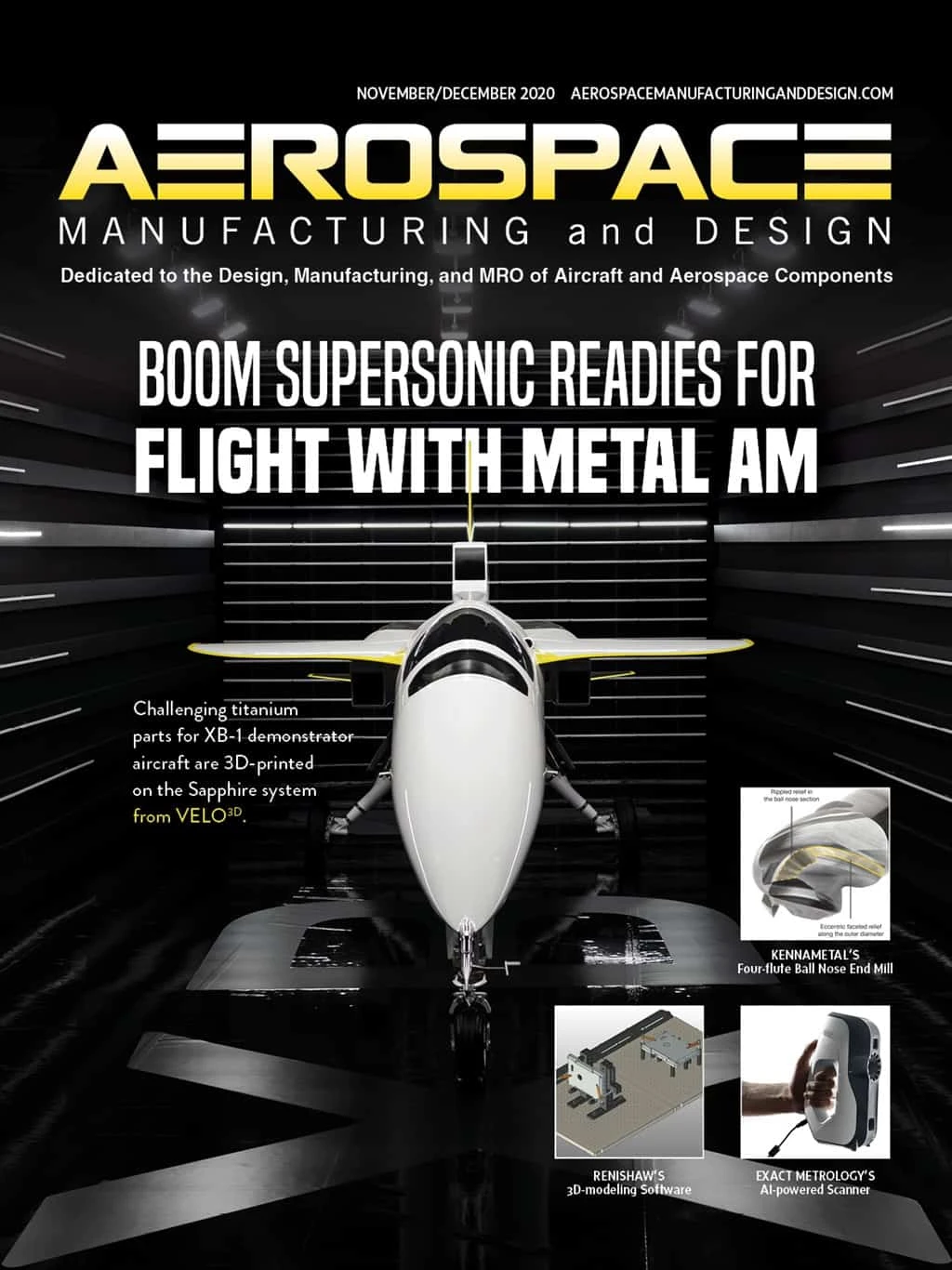
Explore the November December 2020 Issue
Check out more from this issue and find your next story to read.
Latest from Aerospace Manufacturing and Design
- Talking machine tools with the professionals who build them
- Tools and strategies for improving your machining processes
- America Makes announces QTIME project call
- Innovation meets precision for 40% faster machining
- Upcoming webinar: Pro tips from a supply chain strategist
- Heart Aerospace relocates to Los Angeles
- Fixtureworks introduces Stablelock Clamps
- Piasecki acquires Kaman's KARGO UAV program