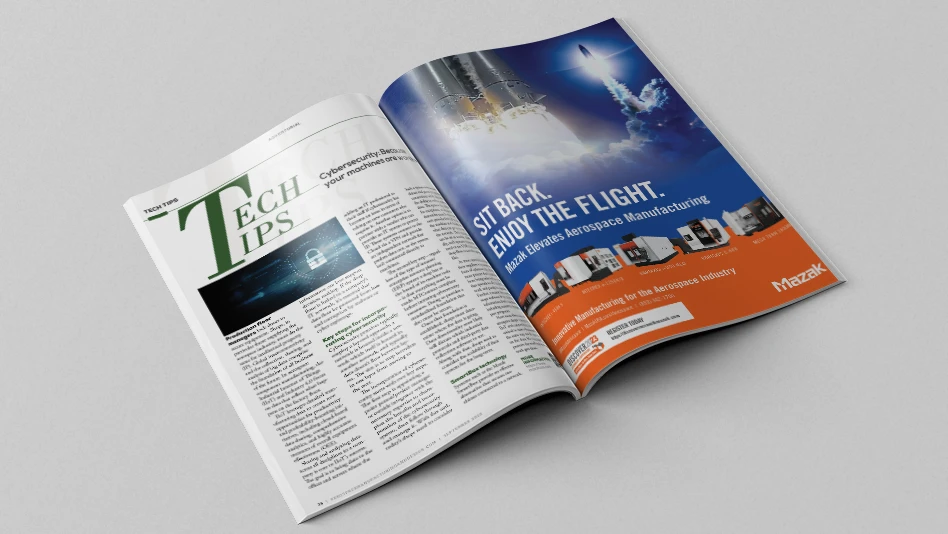

Production floor managers lock doors to secure equipment. Shops, in particular those supplying the aerospace industry, must do the same for intellectual property (IP). Global interconnectivity and the collection, sharing, and analysis of big data comprise the foundation of all business of the future. In aerospace component manufacturing, the Industrial Internet of Things (IIoT) and Industry 4.0 focus on data that reflect what happens on the factory floor.
IIoT leverages detailed manufacturing data to create new opportunities for productivity and profitability-boosting initiatives, including cloud-based data sharing, comprehensive analytics, and highly accurate measures of overall equipment effectiveness (OEE).
Sharing and analyzing data across all disciplines in a company is core to IIoT’s success. The goal is to bring data to the offices and servers where the information can best support decision making. If the shop floor is linked to a company’s IT network, it’s essential that data flow be protected from loss and corruption by malware or cyber espionage.
Key steps for incorporating cybersecurity
Cybersecurity practices typically employ a layered approach: a network is housed inside a network which itself is housed in another network, and typically data doesn’t flow between layers. The aim is to stop intruders in one layer from moving to the next.
The incorporation of cybersecurity starts with two key steps. The first step is appointing a point person/project manager or outside integrator with the necessary expertise to champion the benefits and incorporation of the cybersecurity system, then follow through and manage it. With this said, today’s shops need to consider adding an IT professional to their staff if cybersecurity has become an issue in terms of taking on new customers who require it. Another option is to partner with a vendor who can provide an IT system to protect IP. These systems connect to the Cloud via a VPN and provide an independent network that pushes data out, so the system isn’t connected directly to machines.
The second key step – regardless of the type of intranet/enterprise resource planning (ERP) system a shop has or the brand of its machine tools – is that everything must be made MTConnect compliant before initiating cybersecurity measures. Doing so provides a standardized foundation that also must be secure.
Once that foundation is established, shops must determine where the data is going. Data directionality most likely will dictate which industrial protocols and third-party data collection software to use. Along with that, shops need to consider the scalability of their system for the long-term.
SmartBox technology
Systems such as the Mazak SmartBox provide an effective alternative that secures machines connected to a network. Such a system isolates machines and prevents unwanted connections while also retaining the ability to collect read-only data. The system also allows for exceptions, so shops can determine exactly who can and can’t pass the firewall to access the machine and decide exactly what data can go in or out of the network. These exceptions can be set as needed. Additionally, such systems eliminate the need to use USB ports on the shop floor to transfer program files.
As more customers require their suppliers to provide some form of cybersecurity, shops must prevent their machines from being infected by a virus that spreads to the facility’s network and paralyzes operations. Further, a secure data system stops malware from stealing information from machines, including customer designs and part programs.
Now more than ever, as aerospace shops commit to IIoT and connectivity, it’s critical to view cybersecurity the same way we all view a lock on the door. It’s a necessity that protects the work and how the work gets done.

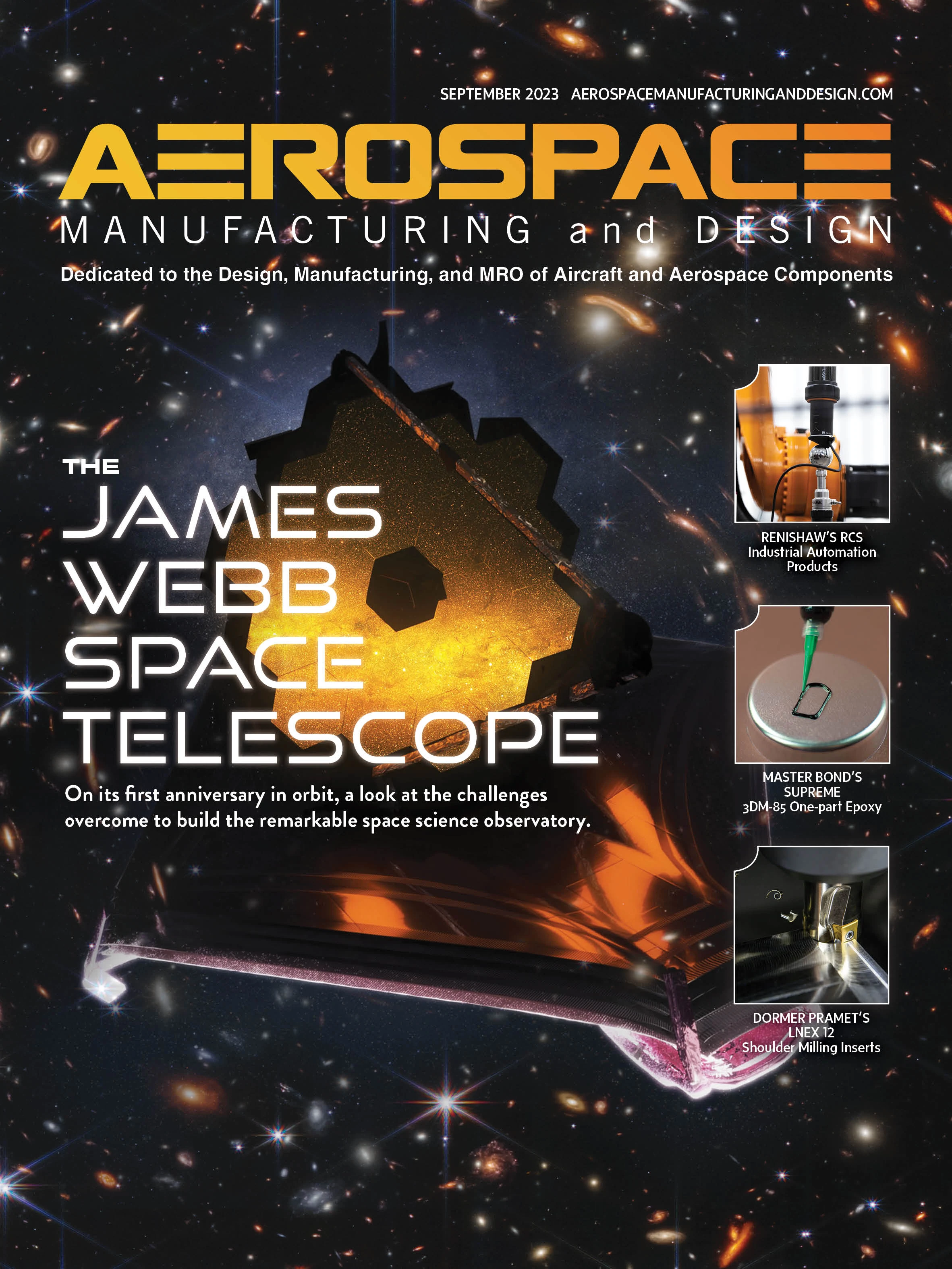
Explore the September 2023 Issue
Check out more from this issue and find your next story to read.
Latest from Aerospace Manufacturing and Design
- You can still register for March’s Manufacturing Lunch + Learn!
- Ohio creates Youngstown Innovation Hub for Aerospace and Defense
- Tormach’s Chip Conveyor Kit for the 1500MX CNC Mill
- How to Reduce First Article Inspection Creation Time by 70% to 90% with DISCUS Software
- Jackson Square Aviation orders 50 Airbus A320neo aircraft
- Beckhoff's motion control automation solutions
- #40 - Lunch & Learn with Fagor Automation
- Air Methods to purchase up to 28 Bell helicopters