
Mitutoyo America Corp.

The complex and varied nature of aerospace assemblies means an ineffective measurement process will slow production time and compromise accuracy. Given the critical nature of aerospace manufacturing – every element in an engine or turbine must meet precise tolerances to ensure reliability – less-than-perfect performance simply isn’t an option.
The norm is 100% inspection and electronic data collection, and metrology solutions must keep pace. As regulatory requirements become stricter and production cycles become shorter, this is becoming a significant challenge. Consequently, the aerospace industry must find ways to validate designs ahead of final assembly.
Today, engineers rely on metrology techniques such as 3D modeling or CAD comparison to prevent expensive rework and speed final production without compromising accuracy. More recently, advances in form measurement are also helping aerospace-focused parts manufacturers better meet production and quality goals.
The form measurement challenge
From commercial airliners to high-tech fighter jets and space exploration vehicles, aerospace industry manufacturers must produce large, intricate parts to extremely high tolerances. Beyond dimensional measurement, proper hardness, contour, and surface roughness must also be verified.
Form measurement of these additional three aspects on a part usually requires a sizable investment in capital and floor space for three dedicated machines. In addition to equipment-related costs, form measurement is time-consuming and tedious, requiring large, heavy components to be moved and positioned on each machine.
Now, next-generation automated form measurement systems can measure a part’s surface, contour, and roundness tolerances on a single cross-functional machine – and do it with faster setup, greater accuracy, and repeatability.
The introduction of cross-functional form measurement technology has come just as aerospace companies are rebounding from the downturn from the COVID-19 pandemic. Many are looking to adopt new smart factory automation processes to speed time-to-market and make it right the first time to meet ramped-up parts demand. Manufacturers are also challenged to improve processes for high-precision measurement of tensile strength, hardness, and intricate, tight-tolerance components made from exotic alloys. This intricacy, plus the large size and weight of aerospace parts, comes into play when selecting a form measurement solution for surface, contour, and roundness.
From analog to automated
Advanced cross-functional form measurement machines have abandoned manual processes and analog technology for electronic sensors and meters controlled by PC-based software. Instead of a physical needle moving on the face of a meter, the measurement values appear on a PC interface, making the process more advanced and easier for form measurement operators to use.
One advantage of this approach is the setup of the part being measured, and the overall measuring process, can be completed faster with less risk of human error.
Operators create a program in the system’s software for parts encompassing surface, contour, and roundness measurements. Then, the program controls the cross-functional machine to automatically make each of the on-contact measurements. It automatically adjusts centering and leveling, and reorients the detector orientation, if necessary, without stopping the program mid-process.
This automated approach replaces three dedicated machines, eliminating the need for operators to move parts to a different machine and reposition them for a different mode of measurement, virtually eliminating outside variables that could affect measurement accuracy. Automated, cross-functional machines also show potential in improving several other critical areas.

Reduced cycle time
Advanced form measurement machines are designed to save time throughout the entire process. For example, the positioning distance from the start of measurement to data acquisition is reduced to 0.05mm, even for edges and narrow parts where it’s difficult to attain sufficient measurement distance. In addition, the measuring system can automatically detect the workpiece contact, then immediately move into standby mode for the start of measurement approximately 3x faster than a conventional model, significantly improving overall measuring efficiency.
Data analytics support process improvements
The software driving automated cross-functional form measurement systems makes it easy to generate reports exportable to analytics software or other data collection systems. Manufacturers can analyze the results of every measurement made by the machine, take an average, and chart it so they can ensure their processes are precise and highly efficient. Analysis of collected data through time makes it easier to identify bottlenecks or problem areas that could be improved.
Deciding between cross-functional and standalone machines
Despite their potential benefits, cross-functional machines aren’t right for every aerospace parts manufacturer. Consider these factors when choosing either a standalone or multi-functional form measurement machine:
Some components may be too large or too small to be placed on a cross-functional machine. In this case, a standalone machine dedicated to a single tolerance measurement may be a better option.
The choice of machine can also depend on the parts being produced. Certain components require only surface analysis, which could be performed with a dedicated machine. However, cross-functional form measurement machines cover all three disciplines, plus automated measurement capabilities, which would be the best option for manufacturing parts needing surface, contour, and roundness measurement or if a company plans to expand into new products.
The future of form measurement
The more advanced, highly automated precision machines have the potential to provide cost savings by reducing part setup time and increasing repeatability. In addition, manufacturers can reclaim factory floor space by using only one measurement machine instead of three, as well as assigning just one system operator to better use manufacturing line staff.
The choice of a form measurement system – whether standalone or cross-functional – depends on the company’s specific needs, what parts they are producing, and their vision for the future. With the recent emergence of more advanced cross-functional machines, aerospace parts manufacturers have more options.
Mitutoyo America Corp.Get curated news on YOUR industry.
Enter your email to receive our newsletters.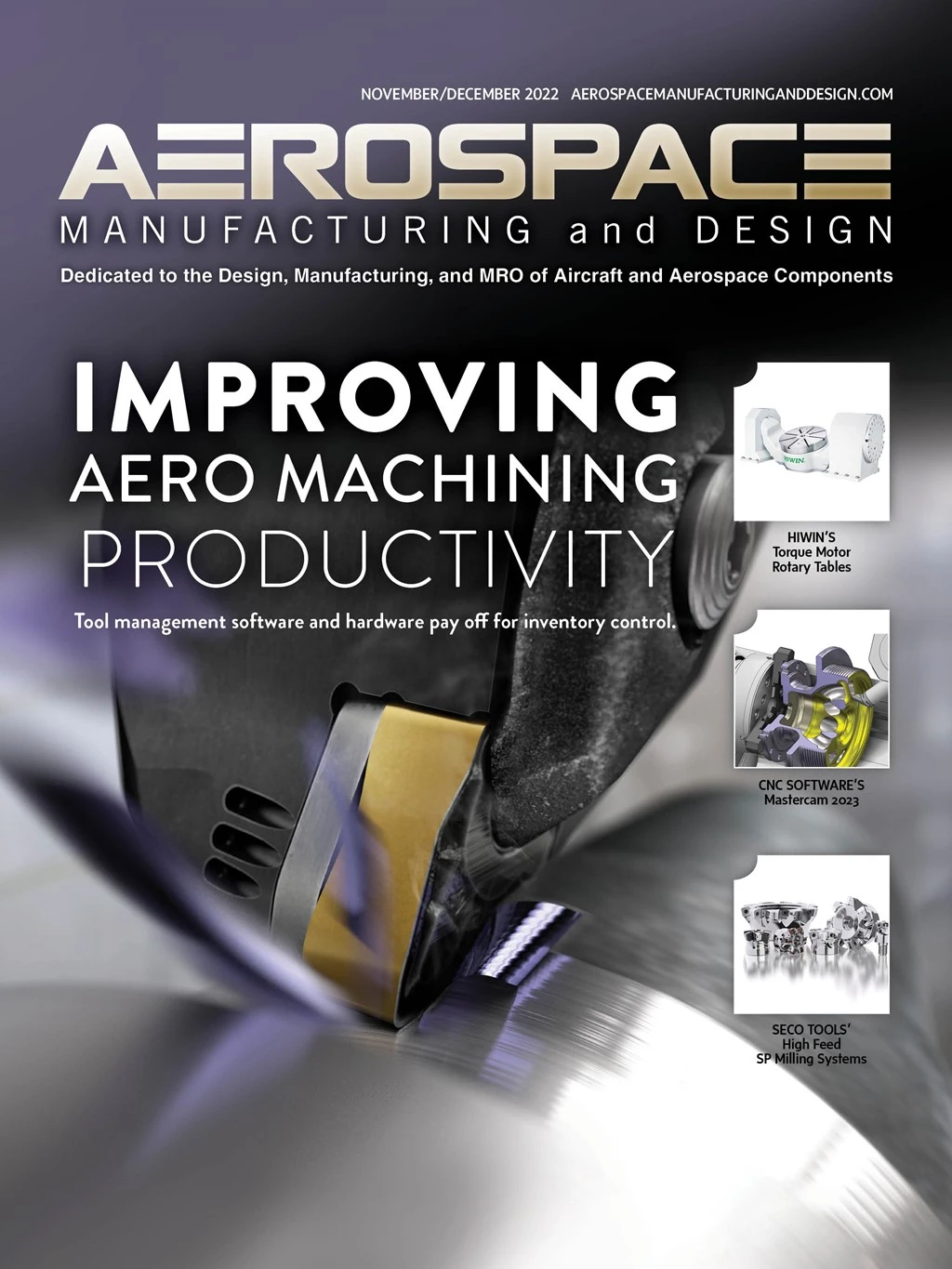
Explore the November December 2022 Issue
Check out more from this issue and find your next story to read.
Latest from Aerospace Manufacturing and Design
- Pemamak's PEMA Vision 3D software
- Aerospace Industry Outlook - Spring 2025, presented by Richard Aboulafia
- Panama’s National Air and Naval Service selects Embraer Super Tucano
- Model 5770 Linear Abraser
- #42 Lunch + Learn Podcast - Quell Corp
- RECARO Aircraft Seating showcases advanced comfort solutions at AIX 2025
- Mitutoyo America’s MiSTAR 575 Shop Floor CNC CMM
- Korean Air finalizes Boeing widebody order