
Whether maneuvering out to an oil platform or transporting executives around the city, rotorcraft safety depends on many critical fluid systems, components, and processes working together. Extreme temperature protection and vibration reduction must be addressed before a rotorcraft can leave the ground. De-icing and freeze protection technologies, temperature valves and heaters, linear and rotary actuators, and fluid valves handle these issues, increasing the lifespan and dependability of rotorcraft components.
De-icing technology – Ice buildup on air inlets or rotor blades can have devastating impacts to a helicopter’s performance. To ensure optimal performance, safety, and efficiency, electrical heaters can be designed to a customer’s unique requirements. Engineers can employ the latest materials and the precise circuitry design to get the optimal amount of heat where it’s needed with the minimal amount of aircraft power.
Fluid valves – A top priority should be finding products with enhanced safety, reliability, and efficiency that fit a robust, highly engineered solution. Motor-operated valves designed for enhanced reliability through features such as contactless switching on the opto actuator use optical sensors instead of mechanical switches for position indication and motor control. Removing contact from the design can eliminate mechanical wear, improving safety and reliability for critical applications.
Fuel and hydraulic valves designed for zero external leakage under high pressures are ideal for critical applications and can help prevent catastrophic events. Designed with a layer of redundancy, shrouded valves divert any fuel leaking from the primary line to a secondary line surrounding it. In the event of a system failure, shutoff valves close the line and prevent failure propagation from additional fluid leaking downstream.
Thermally induced pressure buildup must be relieved in fuel and hydraulic lines to avoid serious system issues. Growing pressure on one side of a closed valve can damage equipment and rupture lines. Valves that contain pressure-relief features allow fluid in the line to drain across or outside of the valve, depending on the requirement.
Electromechanical actuators – Designed for the most demanding applications and harshest environments, linear actuators with rugged housing designs are able to withstand high-load requirements. They must employ robust environmental seals, ensuring the sensitive electronic components are not compromised by exposure to cleaning or de-icing fluids, humidity, or extreme temperatures. Dual-motor rotary actuators, designed with redundant power/control inputs and gear-train features for flight-critical applications, can continue to function as designed in the event of a component failure in the actuator or in the equipment surrounding it.
For complex applications requiring additional levels of control, a combination of linear and rotary actuators can respond to the drive logic for precise positioning. Ideally, choose these products without software-based electronics to avoid the associated reliability concerns and costly certification efforts.
Crucial for safety
Rotorcraft safety is imperative to passengers and operators, on and off the ground. De-icing heaters prevent damage and risk from ice buildup and avoid performance degradation such as decreased air speed and reduced lift capability. Valves are critical for performance, safety, and efficiency in aircraft operation. Linear actuators are capable of withstanding high loads in harsh environments, so the rotorcraft can operate wherever it flies. Dual-motor rotary actuators offer the enhanced reliability of redundancy, ensuring the safety of passengers and operators. Be sure that these components feature the latest designs and advances in technology when evaluating any rotorcraft. Doing so will provide a heightened level of safety and optimal performance.
ITT Control Technologies
About the author: Thomas Zilch is sales manager for ITT Control Technologies’ Aerospace Controls division. He can be reached at thomas.zilch@itt.com or 661.295.4000.
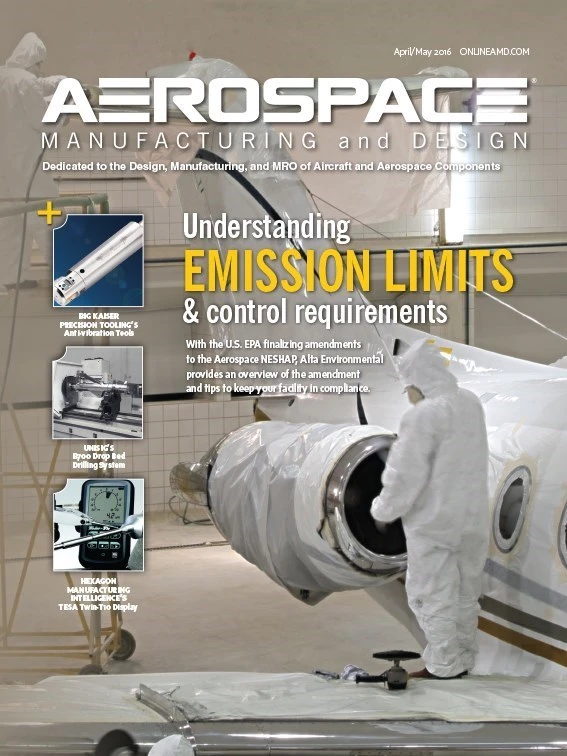
Explore the April May 2016 Issue
Check out more from this issue and find your next story to read.
Latest from Aerospace Manufacturing and Design
- Revitalizing the Defense Maritime Industrial Base with Blue Forge Alliance
- Safran Defense & Space opens US defense HQ
- Two miniature absolute encoders join US Digital’s lineup
- Lockheed Martin completes Orion for Artemis II
- Cylinder CMMs for complex symmetrical workpieces
- University of Oklahoma research fuels UAS development
- Motorized vision measuring system
- Everyone's talking tariffs