
Improved computed tomography (CT) techniques could better recognize manufacturing flaws and structural damage to aerospace composites, improving future aircraft.
Andrew Makeev, professor in the University of Texas at Arlington’s (UTA) Department of Mechanical and Aerospace Engineering, received a $900,000 grant from the Army Research Lab to advance structural diagnostics and life assessment in composite aircraft parts.
Makeev, who also directs UTA’s Advanced Materials and Structures Lab, will lead the project to improve reconstruction algorithms and software techniques to produce breakthroughs in computed tomography (CT) scanning.
The effort will focus on developing effective tools for high-resolution, one-sided CT-based non-destructive inspection (NDI).
Currently, composite aircraft structures are susceptible to damage precursors such as porosity, voids, and sustaining fiber-waviness. Those discontinuities may evolve into structural damage in the form of cracks and delamination or composite layer splitting.
X-ray CT provides reliable micro-resolution NDI data that allow automated interpretation of the inspection results including the listed flaws. However, current micro-focus CT technology is based on scanning 360° around the object, limiting the technology to small cross sections, preventing accommodation of large structures.
Even small objects that can be scanned in existing micro-CT facilities don’t always allow for sufficient magnification of the micro-structure during full scanning, and available limited-angle reconstructions lose definition and often become erroneous during one-sided inspections.
“We believe that to advance composite aircraft structural certification, the analysis must capture manufacturing complexity and variability of flight-critical components and structure,” Makeev says. “Recent improvement in computing power and advances in X-ray CT reconstruction make it possible to develop high-resolution, one-sided CT inspection technology breaking through the object size limits of X-ray CT. It also offers the long-sought automation for composite aircraft structures.”
Get curated news on YOUR industry.
Enter your email to receive our newsletters.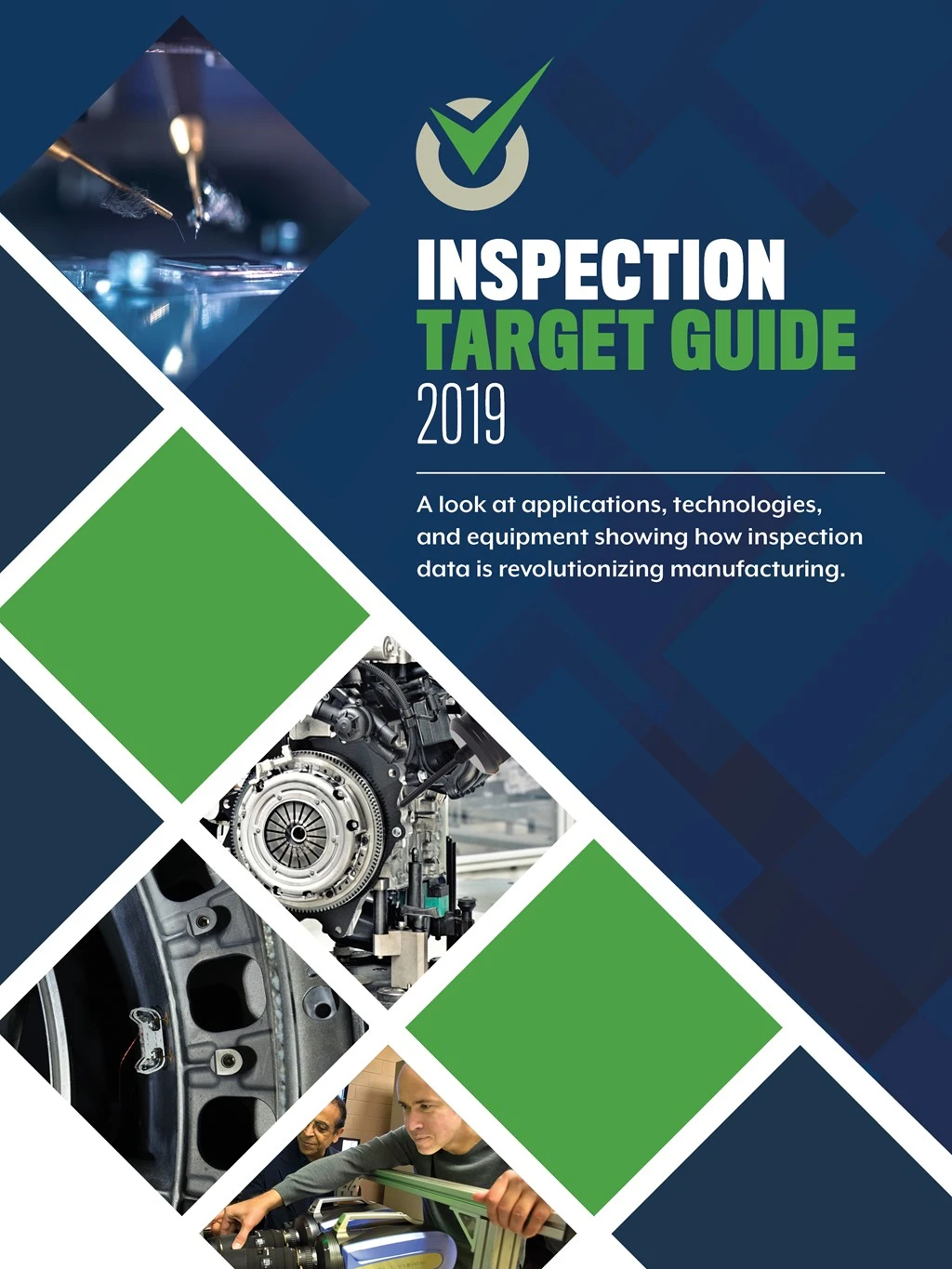
Explore the Inspection Target Guide Issue
Check out more from this issue and find your next story to read.
Latest from Aerospace Manufacturing and Design
- Piper Aircraft receives its largest ever domestic trainer order
- Miniature, high force-to-size linear voice coil servo motor
- MagniX, Robinson to develop battery electric R66 helicopter
- Zero-point clamping modules
- Hartzell electric engine propeller earns FAA approval for AAM
- Thin profile flame and thermal barrier
- Guill Labs offer materials and extrusion testing
- High production vertical honing systems