
Why do we need coolant? How should we apply coolant to our machining operations?
These are questions that every manufacturing company asks, and the reality is coolant is necessary. It provides lubricity to the machining process, reduces heat, and cools the cutting tool, allowing machines to run faster. Coolant improves cycle times and, in many cases, improves overall quality of the parts being produced.
When asking how to apply coolant, also determine if you need high pressure or volume. Most machine tool builders provide low-pressure, low-volume coolant pumps on machines as standard. However, there’s also an option to add higher pressure pumps for purchase.
Let’s explore volume for a minute. If you are milling on a vertical machine, chip removal is very important. High volume coolant flow is critical for removing chips from the cutting area because chips can’t be removed, there’s the possibility of re-cutting chips, which creates problems for the inserts in the cutter and the part’s surface finish. Volume of coolant flow helps wash the chips from the cutting area and move them away so the chip conveyor can remove the chips from the machine. Removing chips protects cutting tools and parts, so coolant flow volume is very important.
That explains volume but what about pressure? What is high pressure? This subject is debatable. I have seen how high-pressure coolant changes the machining process. In many machines 1,500psi is considered high pressure. Not only do you need pressure, but you must also have flow rate. Many of today’s systems provide 3gpm-to-5gpm flow rates as standard, which helps provide additional chip control, lubricity, and heat removal from the chip formation area.
As previously noted, I have personal experience viewing machining high-temperature alloys with high-pressure coolant. We were machining titanium with flat-top carbide inserts at 400sfm. With coolant pressure of 3,000psi and a flow rate of 9gpm, we were able to achieve excellent chip control and double tool life.
Coolant is crucial to the machining process. The question of volume vs. pressure isn’t going to be answered here today. However, I believe that you’ll need both depending on the type of machine, material, and process used to machine your products.
Work with your machine builder, tooling supplier, and your coolant provider. They will make sure you have exactly what you need to successfully machine your tough-to-cut materials.
CMR Consultants
miker2468@aol.com
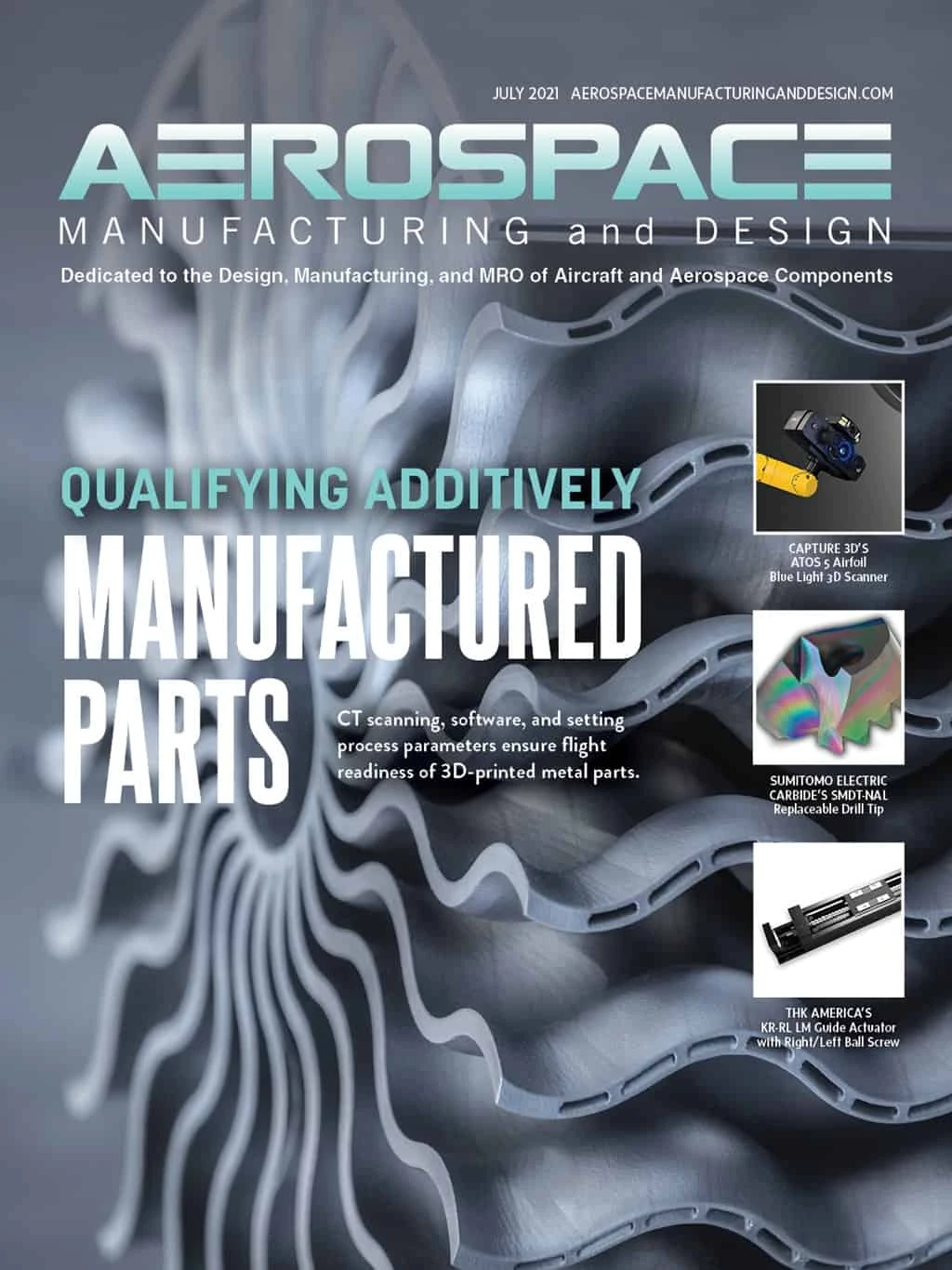
Explore the July 2021 Issue
Check out more from this issue and find your next story to read.
Latest from Aerospace Manufacturing and Design
- UT researchers receive Air Force grant for wind tunnel
- Monticont's linear voice coil servo motor
- FAA certifies Pratt & Whitney GTF engine to power the Airbus A321XLR
- Wevo's silicone gap filler
- Daher Learning Center inaugurated
- HEMCO Corporation's UniFlow CE AireStream fume hoods
- IMTS 2024 Booth Tour - Niigata
- PNAA announces ADVANCE 2025