
Aerospace maintenance, repair, and overhaul (MRO) service providers grind, sand, saw, or drill various materials that generate airborne dust and particulates. The issue becomes problematic when dangerous materials such as hexavalent chromium, lead, cadmium, or other heavy metals are involved, as well as materials such as aluminum, ceramic, fiberglass, and carbon fiber. Toxic dust and debris can lead to illness and even death. Some are potentially explosive, can damage aircraft components, or cause catastrophic failures.
To mitigate these safety risks, the industry needs more effective techniques and tools to capture dust and debris at its source during repairs. This involves a complete system approach that addresses everything from the abrasives used to the tools, hoses, and vacuums that safely capture and handle potentially harmful particles at each step of the process.
According to Mike Donnelly, an aircraft composite repair specialist in Britain, the angled die grinders he uses rotate at very high speeds, often with a 3" 60-grit abrasive and occasionally a more abrasive 40-grit disc. As a result, they kick up a considerable amount of respirable dust and debris.
“High-speed, unshrouded, composite grinding can produce a substantial amount of fine airborne dust,” Donnelly says. “Fortunately, this type of conventional grinding equipment is now very much a thing of the past.”
Since grinding, cutting, sawing, and drilling operations launch dust into the air, shrouds attach to the tool body to contain dust at the source. However, traditional grinding shrouds were not really designed with the aviation composite repair specialist in mind, and are more suited to masonry or heavy metal bench work.
“Because grinding shrouds are typically very restrictive and cumbersome, they can actually cause operators to further damage a composite panel if fine, precise damage removal is required,” Donnelly explains.
Traditional grinder shrouds are not fully 360° articulated and 100% rotationally free of the grinder body, so they are unsuitable for advanced, composite-damage removal, according to Donnelly.
“Precision composite aircraft repair is similar to open heart surgery in that you have to be very dexterous with your fingers, hands, and arms,” Donnelly says. “When you use grinding tools, they almost have to be an extension of your hand or arm with absolutely no movement restrictions whatsoever.”
Another issue is that typical shrouds are opaque or metallic and much larger than the grinding disc rotating inside it, making it difficult to see the edge of the disc inside.
“This vastly reduces the composite repairman’s view of what he or she is grinding, so it’s easy to remove too much stock and make the repair much larger than intended,” Donnelly notes.
Clayton Associates, Lakewood, New Jersey-based supplier of source capture tools and vacuum sanding equipment that has developed a new grinder shroud design. When used with an appropriate vacuum, the shroud enables the capture of respirable composite dust at its source and improves operators’ hand control and view of what they are grinding.
“Before Clayton Clear Revolution grinding shrouds were introduced in Europe, it was virtually impossible to use a die grinder with high precision for composite repair without making a lot of dust,” Donnelly says.
The Clear Revolution dustless grinding shroud system has been designed to be unrestrictive to the user. It is not bolted to the die grinder body or transmission as with traditional units, instead, it is a standalone shroud with a pair of internal precision sealed bearings, on which a mandrel rotates, with the mandrel shaft locked into the grinder collet. In use, a vacuum dust collection hose attaches to the shroud body, allowing the operator to use the hose as an effective hand-steady, enabling two-handed grinder operation when precision is required.
“Because of the shroud’s design, when mounted on the grinder it can rotate 360° on two internal precision bearings so the vacuum hose never gets in the way,” Donnelly explains. “The shroud is made of clear, tough, durable Lexan, which allows you to see through it. Since the shroud head’s outer diameter is no larger than the abrasive disc rotating beneath it, you can always see exactly what you’re grinding.
“With the grinding shroud, you can do very minor surface work, inter-laminar stock removal, or even dig deep to remove damaged honeycomb core 2.5" below the panel surface, as I discovered when I did extensive testing of the equipment,” Donnelly adds.
Clayton Associates
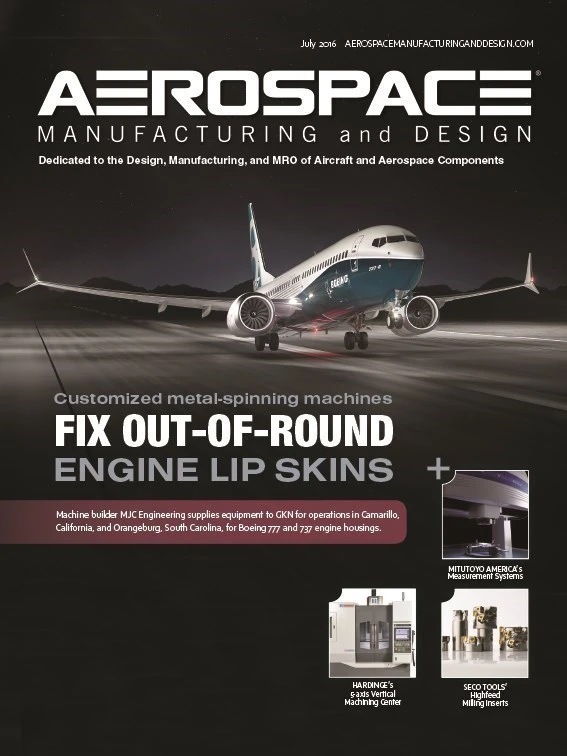
Explore the July 2016 Issue
Check out more from this issue and find your next story to read.
Latest from Aerospace Manufacturing and Design
- Demystifying Controlled Unclassified Information (CUI)
- Simplify your shop floor operations while ensuring quality parts
- Happy Independence Day - July 4th
- Bombardier receives firm order for 50 Challenger, Global jets
- Automatic miter bandsaw
- SAS orders 45 Embraer E2 jets with options for 10 more
- Height measuring instrument
- Shopfloor Connectivity Roundtable with Renishaw & SMW Autoblok