
In 2010, Parrot launched the AR.Drone, a smartphone-piloted quadcopter equipped with an embedded camera. Since then, Parrot has expanded the civil drone industry with a range of drones and minidrones, launching the Bebop 2 in 2015.

The Parrot Bebop 2 offers robustness and reliability in a lightweight, compact drone. With stability and maneuverability, even in extreme conditions, Bebop 2 can be piloted with no prior training. An onboard computer analyzes and merges data collected from seven sensors.
A front-facing camera allows 180° angle adjustment using the piloting device’s touchscreen. Digitally stabilized in three axes, images are bright, stable, and distortion-free.
Flight safety systems include emergency engine cut-out, emergency propellers shut-off, limiting the altitude and flying perimeter, automatic return home, and a light emitting diode (LED) at the back of the machine to see the direction of flight.
Collaborating with CRP Technology
The first Bebop 2 structure was built on injected parts made with polyamide-based glass reinforced composite material.

Then Parrot moved to selective laser sintering (SLS) technology in collaboration with CRP Technology to optimize structural performance without developing long lead time and high-cost injection tooling, accelerate iteration generation, improve manufacturing time, and facilitate series production.
The structure has been developed according to finite-element (FE) modeling aimed at improving video quality that can be altered by vibrations during flight and using a smart design to reduce weight. Parrot validated that natural frequencies of parts manufactured with Windform GT material were similar to injected parts made with polyamide-based glass reinforced composite material. FE analysis, additive manufacturing with SLS, and using Windform GT material have dramatically reduced development time, allowing small production batches with acceptable mechanical properties in functional products for the team to evaluate characteristics such as flying performance.
CRT Technology provided fast response time to new requirements, cooperation with its engineers and computer-aided design (CAD) designers, and best output quality with unique proprietary processes. The requirements were fast iteration process, best ratio between structural strength and weight, acceptable consistent results, and the opportunity to combine multiple functionalities obtained from one unique part.
CRP Technology Srl
Parrot
Windform
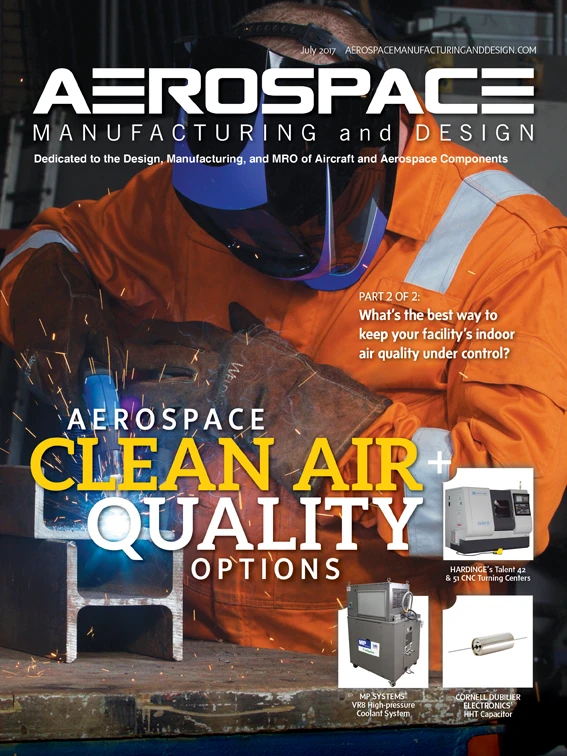
Explore the July 2017 Issue
Check out more from this issue and find your next story to read.
Latest from Aerospace Manufacturing and Design
- Revitalizing the Defense Maritime Industrial Base with Blue Forge Alliance
- Safran Defense & Space opens US defense HQ
- Two miniature absolute encoders join US Digital’s lineup
- Lockheed Martin completes Orion for Artemis II
- Cylinder CMMs for complex symmetrical workpieces
- University of Oklahoma research fuels UAS development
- Motorized vision measuring system
- Everyone's talking tariffs