
As the aerospace manufacturing industry faces rising demand for new aircraft, major players and their suppliers seek to leverage automation as they test and adopt new materials and processes. This includes increasing use of composite materials including thermosets, thermoplastics, ceramic matrix composites, and dry fabrics.
Factors driving the need for new materials and greater automation include:
- Environmental sustainability, including lightweighting to reduce emissions, fuel consumption; implementing eco-friendly production practices
- Cost control, especially amid tariff uncertainties, fluctuating fuel and raw material costs, intense competition
- U.S. unemployment rate in the single digits, associated labor shortages
- Heightened risk aversion in aircraft design, engineering, manufacturing
- Productivity pressure to meet delivery goals
Validating solutions
As automation options are considered, aircraft original equipment manufacturers (OEMs) and their suppliers need to evaluate ways to format and process composites. From the formatting perspective, will the materials need to be slit and spooled, chopped, or cut into plies? Regarding processing, will the formatted materials be laid up robotically or manually, consolidated in situ, cured in an autoclave, pressed in an injection mold, or braided?
A composites formatter needs a deep understanding of an aircraft program’s design parameters and cost, throughput, and quality requirements to build a solution designed for manufacturability, including:
- OEM’s use of factory automation
- Spools of slit tape for robotic automated tape laying (ATL) or automated fiber placement (AFP)
- Ply kits handled by humans, robots, or hybrid configuration
- Preforms that go straight onto a tool for curing
- Some other format altogether
The answers often require trial runs and testing to determine the best plan of action. For example, Web Industries Inc. has a Development Center for Composite Automation and a Thermoplastic Development and Qualification Center in Atlanta, Georgia, along with a Composite Center of Excellence in Nantes, France.
These centers allow formatters to conduct chemical and mechanical tests on composite materials and perform trials of different composite formats on various processing equipment. The National Composites Centre (NCC) and the Thermoplastic Composites Research Center (TPRC) are industry consortiums that provide additional settings to test new ideas and concepts on the latest automated equipment. At the TPRC, this includes the ability to perform advanced simulations of how a thermoplastic composite will fit over a mold and perform under different scenarios, allowing adjustments before making an expensive mold.
Scaling up production smoothly
The time and resources devoted to trials should pay off when materials and processes have been qualified, put through their paces, and into production. A composites formatter can partner with aircraft OEMs and suppliers to meet goals without compromising quality, safety, productivity, or profitability. However, the formatter must have the right capacity, systems, and technology to help mistake-proof scale-up to high production volumes. This is of utmost importance amid pressure to maintain productivity, safety, and quality.
A formatter can help simplify the supply chain by delivering a combination of composite materials, in the needed formats, into the value stream at the right time. For example, Web Industries’ SpoolKit is a specialized logistics solution allowing the formatter to deliver various composites in different formats in a single container. The composites, whether on spools, plies, or other formats, are positioned in the container so they can be unpacked and put right into use on the aircraft manufacturing line. Another technology, PlyScan, helps manufacturers streamline production and prevent errors. Every ply is labeled and sequenced in the proper order for layup, reducing the risk of incorrect installation which can waste materials and cycle time.
In addition, formatters can offer materials management technology to keep the aircraft or component manufacturer from getting bogged down in the details of out-time tracking, freezer capacity, or inbound materials receiving. With predictive analytics, automated track-and-trace systems, and radio frequency identification (RFID)-enabled advance ship notices, the formatter can:
- Track inventory levels
- Replenish formatted materials
- Manage material records
- Alert the manufacturer of materials in-transit for delivery
With these automated systems, the formatter and manufacturer work together to achieve a leaner material flow and prevent costly and potentially dangerous errors. For example, without automated out-time tracking, there is greater risk for a prepreg thermoset carbon fiber material to expire before it is processed.

High-volume precision formatters use advanced shape-nesting technology, computer-numerically controlled (CNC) cutters, 5-axis machining centers, and high-speed slitters. All are necessary to format composites, rapidly and at scale, to meet precise aerospace specifications, with optimal yields and minimal waste. But like their customers, formatters also are looking to invest in greater levels of automation, particularly for material handling. For example, robots will likely play a growing role in picking and kitting composite plies as well as creating preforms and other tasks.
Summary
Automation will continue to gain prominence in aerospace design and manufacturing. Robotics and other automated processing techniques are being developed and refined for working with diverse composite materials. Leading composite formatters are deploying systems and specialized services and solutions to support aerospace customers’ new materials and process automation. In collaboration, composite formatters, aircraft OEMs, component manufacturers, advanced materials suppliers, and automated equipment developers can meet the challenges and opportunities of tomorrow’s aerospace industry.
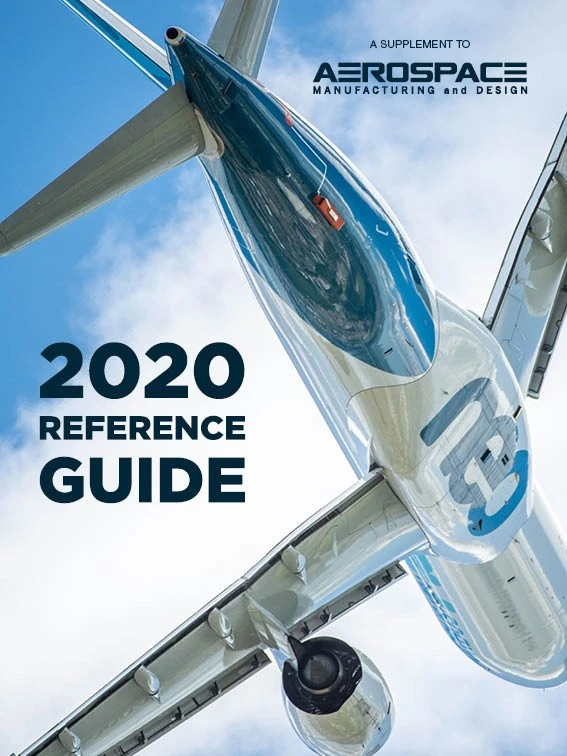
Explore the AMD Reference Guide 2020 Issue
Check out more from this issue and find your next story to read.
Latest from Aerospace Manufacturing and Design
- Lockheed Martin completes Orion for Artemis II
- Cylinder CMMs for complex symmetrical workpieces
- University of Oklahoma research fuels UAS development
- Motorized vision measuring system
- Everyone's talking tariffs
- Boom Supersonic to launch Symphony engine testing in Colorado
- Next-generation precision measurement solution
- #60 - Manufacturing Matters: What's ahead in manufacturing in 2025?