
The visual tool setter (VTS) family is expanding with the VTS SF-45 Compact, suited for non-contact, optical measurement of small, complex-shaped tools in constrained working spaces. It’s installed inside the machine to monitor tool working conditions without contact, allowing the tool to rotate at full spindle speed (up to 80,000rpm) during data acquisition.
The device acquires tool length, static and dynamic tool diameter, run-out, and cutting-edge radius using shadow projection. With a resolution of 0.1µm, the VTS can measure tools with diameters as small as 10µm with repeatability of 0.2µm, providing greater accuracy than touch probes or lasers in small applications. A frontal light illuminates the surface, allowing cutting edge integrity to be evaluated on a PC monitor.
Pneumatic shutters protect the optical lens when VTS isn’t in use, plus an air flow rejects chips and coolant drops, keeping the shutter side clean and protecting the optical lens when the shutter is open.
Marposs Corp.
EASTEC Booth #5232
7-flute end mill series grows

The H-Carb 7-flute high-efficiency end mill series now includes 72 new tools featuring 2.0mm, 3.0mm, and 4.0mm corner radius sizes in 2.5xD, 3xD and 4xD lengths of cut. Ti-NAMITE-A or Ti-NAMITE-M coatings make them suitable for dry machining in numerous carbon steels. The chip breaker profile is standard with a wide range of square end and corner radii options for various machining specifications and use in high-temp alloys and titanium alloys ≤45 HRc.
H-Carb Series 77 end mills excel in high-speed machining and deep axial trochoidal applications such as deep pocketing and slotting. The core and flute design improve rigidity and chip flow while reducing deflection.
Kyocera SGS Precision Tools
Robotic electric force compliance system

The fully electric EFC-02 delivers precise, constant force throughout robotic grinding, sanding, and deburring for consistent surface quality.
As end-of-arm tooling, the EFC-02 connects a grinding machine – angle grinders, orbital sanders, angle polishers, straight grinders, more – to the robot.
Light and small, the unit can be used for material removal or surface finishing in tight or narrow spaces. High-frequency measurements monitor force and acceleration throughout the process while an advanced control algorithm dynamically adjusts force and automates grinding processes based on pre-programmed parameters.
Features
- Simple robot programming using intuitive web-based interface or fieldbus communication
- Industry 4.0 functionality – LED shows grinding wheel surface contact and when stroke is at 50%; indicates when maintenance is needed
Suhner USA Inc.
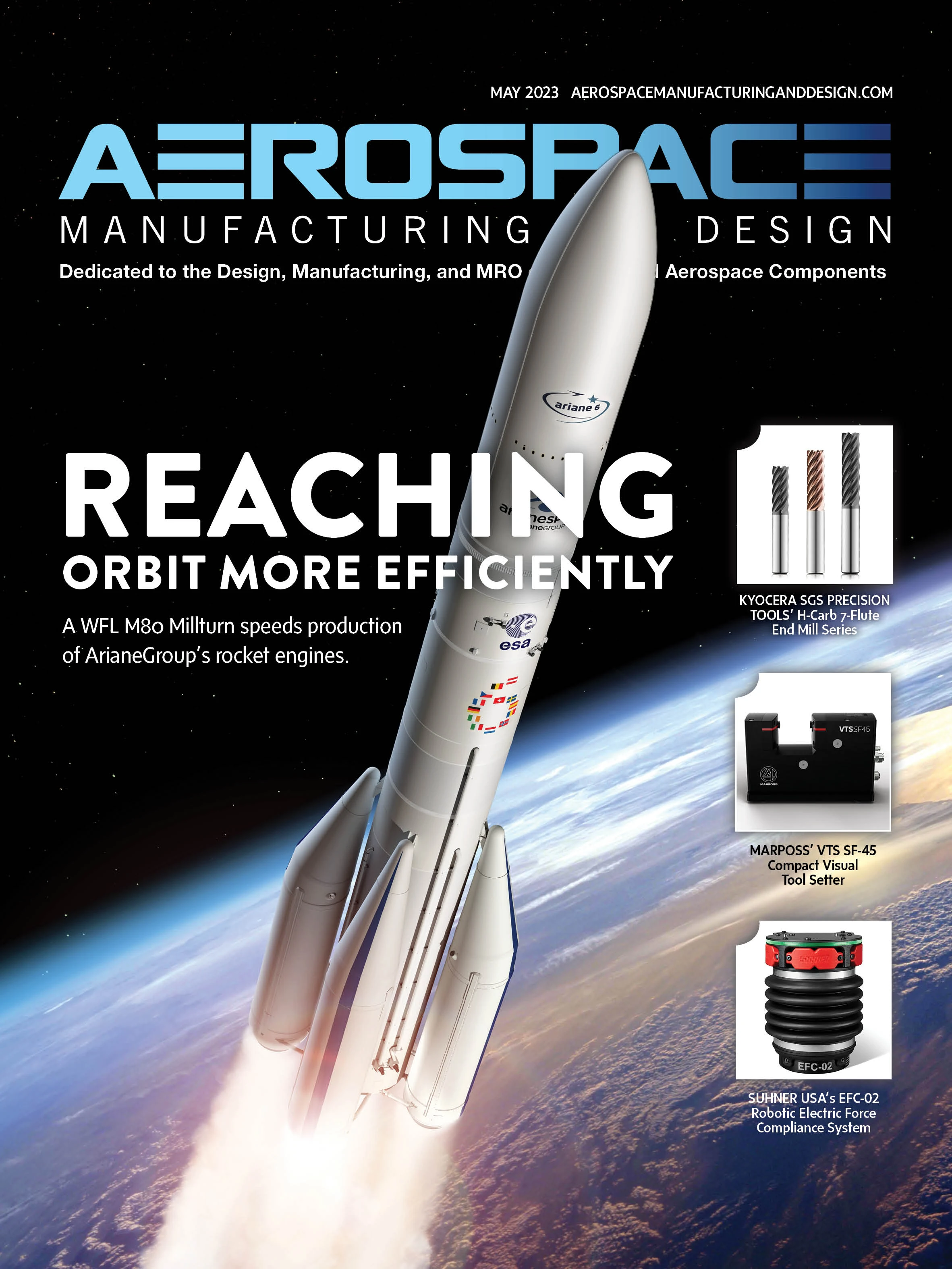
Explore the May 2023 Issue
Check out more from this issue and find your next story to read.
Latest from Aerospace Manufacturing and Design
- Revitalizing the Defense Maritime Industrial Base with Blue Forge Alliance
- Safran Defense & Space opens US defense HQ
- Two miniature absolute encoders join US Digital’s lineup
- Lockheed Martin completes Orion for Artemis II
- Cylinder CMMs for complex symmetrical workpieces
- University of Oklahoma research fuels UAS development
- Motorized vision measuring system
- Everyone's talking tariffs