
While a smartphone has just a few sensors providing data, a machining center can have several hundred. Add to that several thousand data points, derived from the dynamic behavior of control and regulation systems, and in total, there are countless possible sources for large-scale data analysis – with huge potential for more productive, more efficient, and faster production through connection to an Internet of things (IoT) platform.
The cloud-based version of Chiron’s RemoteLine digitalizes and transforms relevant IoT data into productive business results. Designed for industrial applications, it provides remote access in the event of servicing and connects products, systems, and machines.
With the RemoteLine cloud application, data produced by edge computing or sensors directly on the machining centers can be used for comprehensive analyses and digital services.
Each machine produces real parts and large volumes of data, meaning shop owners and managers must decide what data are worth collecting and analyzing. Machine manufacturers must answer several questions – how these data can be correlated, how advantages for individual customers can be developed based on data, and who should evaluate data.
“It’s not about collecting random information Big Data style and then deciding where to start,” says Peter Albrecht, platform connection coordinator at Chiron. “We know which data are of interest for our customers in a world of increasingly digitalized production. In the control system world at Chiron, a great deal of data describes the maintenance condition, part quantities, or the status of the NC axes. This is the invaluable information that we are preparing for our customers and making available in the cloud, on the IoT platform.”
RemoteLine in the cloud
There are many IoT platforms for developing digital services. For the next step in RemoteLine – cloud connection – Chiron will work with Siemens MindSphere.
“The open IoT operating system well-suited to the requirements of machine manufacturers and operators, is currently at the highest stage of development and offers the highest degree of flexibility for the future,” says Dr. Ulrich Heller, head of software development, Chiron Group.

Making use of data
The full exploitation of data occurs through data transfer between the customer and Chiron. Further processing and long-term evaluation of the data take place in the cloud, and a dashboard clearly displays collected information. This enables users to view machine conditions anytime, anywhere in the world, on a PC, laptop, or smartphone.
Key advantage of IoT applications is that companies can use the added value from data simply, quickly, and at reasonable costs. For instance, an app from Chiron for condition monitoring or tool management can be bought through the App Store, installed in the customer’s MindSphere via plug-and-play, and instantly ready to use. Users can start with the full version or download a limited trial version. Besides condition monitoring and tool management, there are other applications that promote the operation of machining centers in a cloud environment, including visualization of the machine location, overall equipment efficiency (OEE) considerations, and access to future innovations.
Data security
All companies must consider the security of their highly sensitive data. Transfer data into the Chiron area within the cloud platform takes place with the highest possible degree of security via SSL encryption. Customers can define the rights for data transfer and access. To guarantee security even further, Siemens continuously monitors the entire system and regularly updates security standards. In contrast to many other storage locations, the data stored in the cloud are extremely well protected against unauthorized access.

Mobile access
In addition to remote access in the event of servicing, Chiron also offers Manage My Machine – an app that can be used to display and manage machine data from all systems connected with MindSphere in the customer’s environment in the local or global machine park. An alarm monitoring system notifies the user of critical machine data, combines this data for more detailed analyses, and provides the basis for increased productivity, reliability, and availability of machining centers.
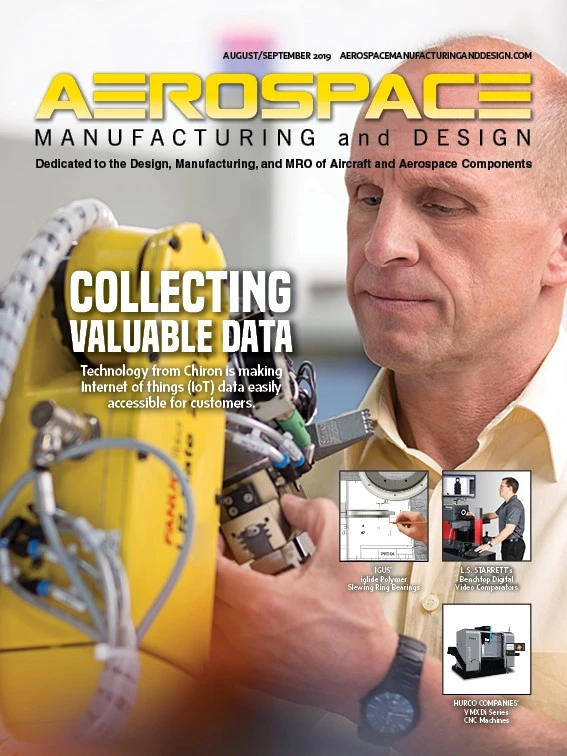
Explore the August September 2019 Issue
Check out more from this issue and find your next story to read.
Latest from Aerospace Manufacturing and Design
- Piasecki acquires Kaman's KARGO UAV program
- PI Americas’ long-travel XY piezo nanopositioners-scanners
- AAMI project call submission deadline extended to May 12
- Jergens launches cast iron tooling column additions
- Airbus to acquire assets relating to its aircraft production from Spirit AeroSystems
- FANUC America's Cobot and Go web tool
- Chicago Innovation Days 2025: Shaping the future of manufacturing
- High-density DC/DC converters for mission-critical applications