
Introduced in North America at IMTS 2022, the TNC7 CNC control supports users from initial design to final machining, one-off jobs to serial production, and simple slots to complex contours.
Along with easy and intuitive operation, users get support from a virtual simulation of the machined part and work envelope. Users can adapt their screen content through personal favorites and their own home menu on the 24" HD touchscreen monitor.
The TNC7 enhances Klartext programming with smart functions and newly developed graphical programming. Users can draw contours directly on the touchscreen and convert them into dialog-guided TNC Klartext programming code. Cycles and older contour programs can still be used, including existing NC programs. Additional smart programming includes a package of functions, intelligent probing cycles, and graphical guidance for determining the position of clamping devices.
Ball-end cutter

The POW•R•ARC ball-end cutter is designed for contouring and chamfering at the fastest possible speed and feedrate in most materials. It cuts smoothly in workpieces with dissimilar materials – no digs or hand work needed. Available with 6 or 8 flutes, the ball-end cutter features advanced geometries and next-generation coating for faster feed rates, greater lubricity, reliable chip ejection, and double the tool life compared to tested competitors.
It cuts and finishes in one pass in hardened metals up to 62HRc, aluminum, stainless steel, low carbon steel, and super alloys such as high nickel alloys, cobalt chrome, and titanium. It’s effective in low-speed, high-speed, and 5-axis machines. Order with long necks for working in deep pockets and easier maneuvering around mold guide pins.
Turning-boring-milling center

The M50 MILLTURN / 3000mm multifunctional turning-boring-milling center machines complex chuck and shaft parts up to 670mm swing over bed. Turning, milling, drilling, hobbing, shaping, gun drilling, and ID machining can be performed under any tool angle. Interpolation up to 5 axes enables machining of any geometrical profile. In addition to HSK or Capto tool systems, prismatic tool holders can access machining areas requiring long tools.
iControl, a process monitoring system, manages signals coming from the machine or external sensors, such as coolant flow rate, coolant pressure, vibration sensors in a boring bar, or the clamping force of a clamping jaw.
- myWFL Cockpit records machine states monitoring override positions and logging program runtimes for a constant overview of the machine’s productivity, runtimes
- myWFL Energy measures, logs machine energy and compressed air consumption by individual tools or process steps
- myWFL Condition Monitoring lets users move spindles and axes by running an idle program at cyclical intervals to record forces, vibrations; long-term evaluation can show if there’s an imminent change in the bearing or guide systems to avoid unforeseen downtime, plan machine maintenance
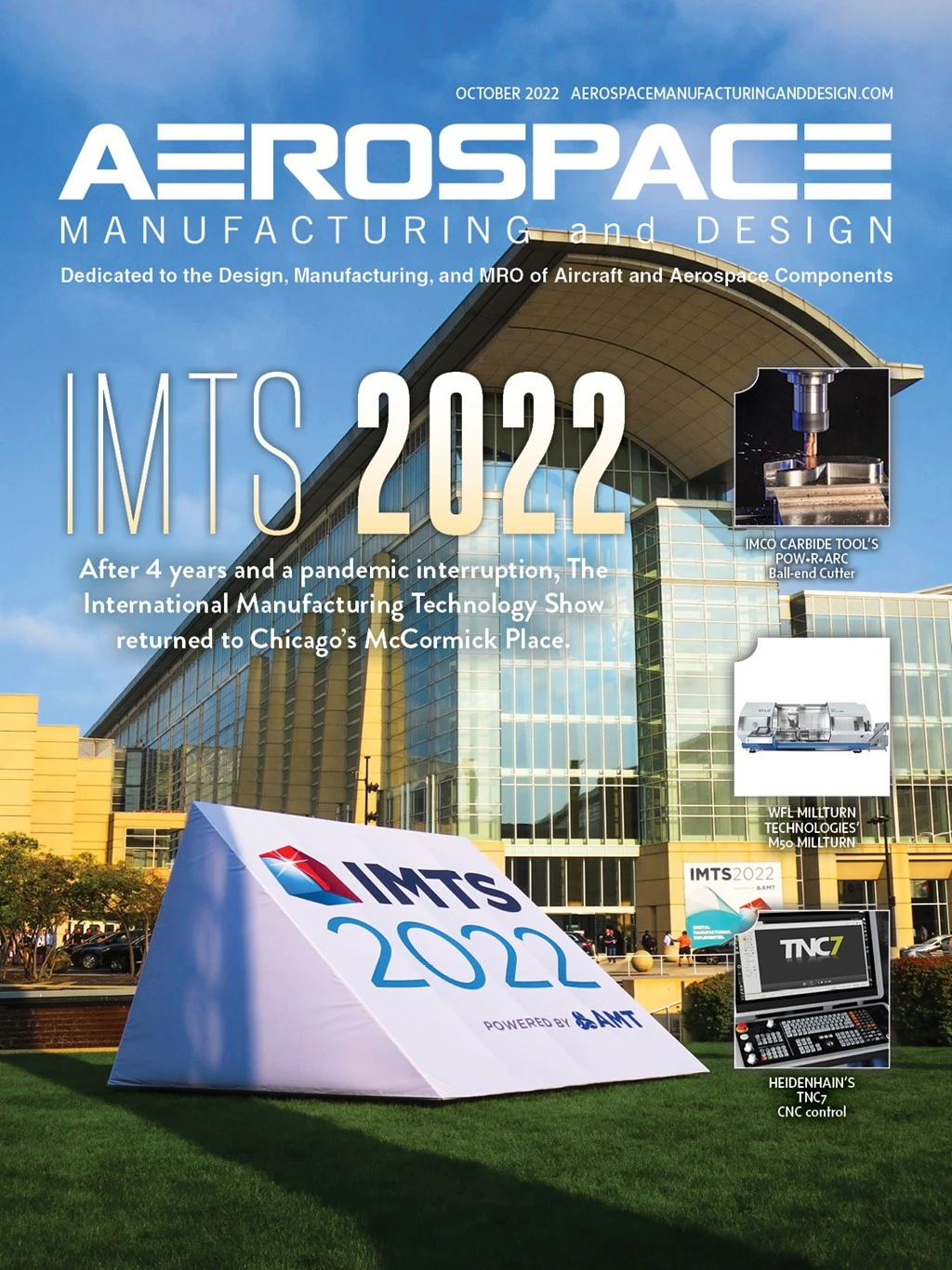
Explore the October 2022 Issue
Check out more from this issue and find your next story to read.
Latest from Aerospace Manufacturing and Design
- BOC Aviation orders 120 Airbus, Boeing jetliners
- Mazak’s INTEGREX j-Series NEO
- Embraer tests wing for new technologies demonstrator
- Mitutoyo America’s SJ-220 portable surface roughness tester
- #55 - Manufacturing Matters - A Primer on Defense Contract Manufacturing
- Registration is open for April’s Manufacturing Lunch + Learn!
- Natilus begins search for new home to build world's most efficient commercial aircraft
- Aerospace Industry Outlook webinar is back by popular demand