
The aerospace industry demands the utmost precision in every component. Even minor deviations can have catastrophic consequences. This is where coordinate measuring machines (CMMs) come into play. CMMs are critical tools ensuring the dimensional accuracy and geometric conformity of aerospace parts, directly impacting aircraft safety and performance.
Every aerospace component, from the seemingly insignificant seatback tray to critical engine parts, plays a role in overall aircraft efficiency, fuel consumption, and safety. That’s why every single dimension and characteristic of an aerospace component is checked to ensure it meets design specifications.
Addressing complex part challenges
CMMs are the workhorses of dimensional measurement in aerospace. These high-tech machines use advanced sensors and computer-controlled systems to precisely measure the geometric characteristics of complex parts. Their capabilities go beyond simple measurements, allowing for intricate analysis of size, shape, and position.
Complex aerospace parts present unique challenges in manufacturing. CMMs overcome these challenges by offering:
- High-precision measurement: CMMs deliver exceptional accuracy, ensuring parts meet stringent aerospace tolerances. These machines can measure features within microns, a level of precision crucial for the tight tolerances demanded in aerospace components.
- Versatility: CMMs can manage a wide range of part sizes and geometries, accommodating everything from small engine components to large fuselage sections. This versatility makes CMMs a one-stop solution for various measurement needs in aerospace manufacturing.
- Detailed data: CMMs provide comprehensive data on a part’s dimensions, form, and location, allowing for thorough quality control, ensuring parts meet design specifications and function as intended within the larger aircraft assembly.
- Improved efficiency: Automated measuring programs and non-contact probing techniques offered by CMMs streamline quality control, saving time and resources.
There are different types of CMM probes for different applications. Scanning probes are ideal for intricate aircraft measurements, while tactile probes offer high-precision point-to-point measurement. Laser scanning probes create detailed point clouds of a component’s surface, allowing for comprehensive analysis of even the most complex features.

For example, CMMs measure the dimensions and ensure the geometric conformity of complex wing structures, a critical factor in aircraft performance and fuel efficiency.
Similarly, the intricate geometries of aerospace engine components require high-precision measurement for proper assembly and function, which CMMs deliver.
And the immense forces exerted on landing gear during takeoff and landing necessitate precise measurement of these components. CMMs help manufacturers ensure the structural integrity and functionality of landing gear systems.
Serving increasingly complex needs
CMM technology is constantly evolving to meet the ever-increasing demands of the aerospace industry. Current trends driving improvements in the sector include:
- Model-based measuring: This approach automates part programming, reduces operator influence, and ensures consistent measurement based on the design intent. By eliminating manual programming variations, model-based measuring contributes to greater accuracy and repeatability in the measurement process.
- 5-axis capabilities: Advanced CMMs offer greater flexibility and precision for complex geometries. With five axes of movement, these machines can access and measure intricate features on complex parts that might be inaccessible to traditional 3-axis CMMs.
- Integration with design software: CMM programs can be directly linked to CAD models, ensuring measurements align perfectly with the intended design specifications.
- Integration with AI: Artificial intelligence (AI) can analyze vast amounts of measurement data, identify trends, and optimize future designs. Data-driven decision making will optimize production processes and predict maintenance needs even as it facilitates continuous quality and efficiency improvements.
- Sensor advancements: Expect improvements in laser technology to overcome limitations with contrasting materials and enhance accuracy.
CMMs evolve beyond quality control
The role of CMMs in aerospace manufacturing is expanding beyond traditional measurement and quality control functions. Here are some emerging applications:
- Reverse engineering: CMMs can capture the precise geometry of existing parts, facilitating the process of reverse engineering. This technology is valuable for creating replacement parts for older aircraft or for replicating components no longer in production.
- First-article inspection: CMMs play a crucial role, ensuring the initial production run meets the design specifications before full-scale manufacturing starts. This proactive approach prevents costly production errors and delays.
- Real-time feedback and in-process inspection: Integrating CMMs directly into the production line allows for real-time dimensional verification throughout the manufacturing process. This continuous monitoring, enhanced by AI, helps identify and immediately address issues, minimizing the risk of producing defective parts. This improves overall quality and reduces waste and associated costs.
- Predictive maintenance: AI-powered analysis of CMM data can predict potential equipment failures before they occur. By analyzing historical data and identifying patterns, AI can anticipate maintenance needs, allowing for proactive maintenance schedules. This minimizes downtime and extends the lifespan of CMM equipment, saving costs.
Challenges on the horizon

The next frontier in improving CMM in aerospace is figuring out the best way to maintain measurement accuracy through time. Regular calibration optimization based on environmental considerations and other factors is crucial for sustained high-precision measurement. Ensuring a controlled environment to minimize the impact of external factors on measurement precision is also key.
Getting AI integration right is also a key issue to resolve. While AI offers immense potential to improve manufacturing and measurement of aerospace parts, some level of human expertise will always be essential for interpreting data and making critical decisions. As CMMs become more connected, robust cybersecurity measures will be crucial.
For example, while AI excels at analyzing data, it can’t grasp the intricacies of design intent. Human engineers with understanding of design goals and functions are irreplaceable in interpreting measurement data and identifying potential issues. They can analyze the data from a holistic perspective, considering the individual component and its role within the larger aircraft system.
The data collected by CMMs and analyzed by AI can be vast and complex. Human judgment is crucial for making critical decisions based on this information. If a measurement falls slightly outside the tolerance range, an experienced engineer can weigh the potential impact on performance and safety and determine the appropriate course of action, such as adjusting the manufacturing process or conducting further analysis.
While AI can be trained on vast datasets, unforeseen situations can still arise in the measurement tasks and other areas of the manufacturing process. Human creativity and problem-solving skills are essential for adapting to these situations and ensuring production continues smoothly.

Optimizing the human-machine collaboration in aerospace manufacturing via CMMs will require enhanced operator training. As CMM technology becomes more sophisticated, the role of the human operator will shift toward data analysis and process optimization. Operators will require specialized instruction to understand the capabilities of advanced CMM systems, interpret the vast amount of data generated, and identify potential issues based on their newly acquired expertise.
As the aerospace industry pushes the boundaries of design and materials, CMMs – integrated with AI and guided by human expertise – will remain the backbone of quality control in aerospace manufacturing. Their precision, versatility, and continuous technological advancements will play a vital role in the production of safe, reliable, efficient, and high-performance aircraft.
Mitutoyo America Corp.IMTS Booth #134117
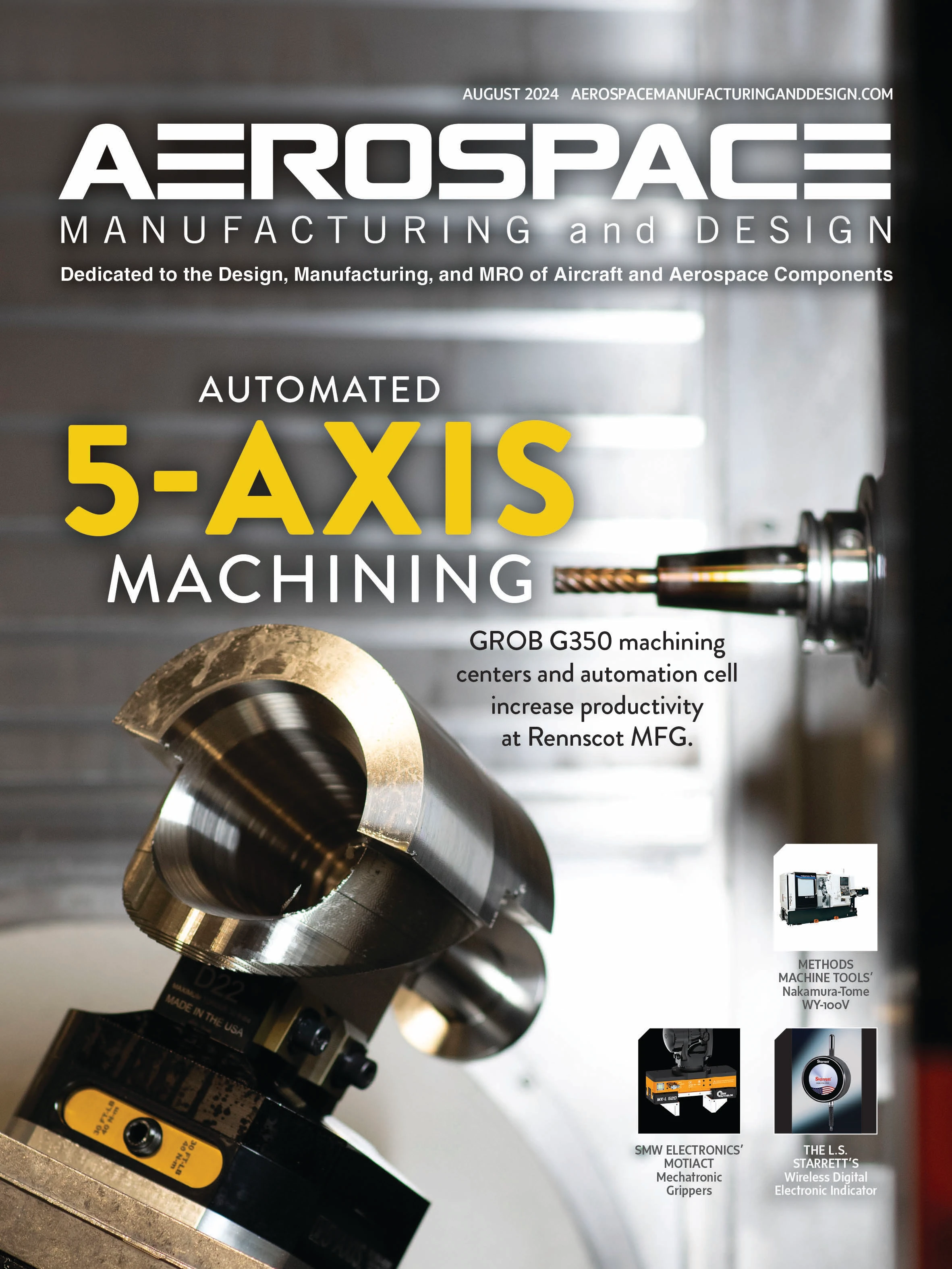
Explore the August 2024 Issue
Check out more from this issue and find your next story to read.
Latest from Aerospace Manufacturing and Design
- Guill Labs offer materials and extrusion testing
- High production vertical honing systems
- July Manufacturing Lunch + Learn webinar with OPEN MIND Technologies
- July Manufacturing Lunch + Learn webinar with Techman Robot
- Hexcel and NIAR expand collaboration
- Open aperture XY alignment stage
- Close out July with our Lunch + Learn on medical machining solutions
- Build your Controlled Unclassified Information (CUI) toolkit