
Liquidtool Manager monitors metal cutting coolant using plug & play technology and a cloud-based platform for intelligent, automated, and reliable measurement.
Its sensor is magnetically mounted on the machine to be monitored, connected to the company’s WLAN or LAN, and operated with the corresponding app via tablet, smartphone, or PC. The sensor, compatible with various coolants, regularly takes coolant from the machine tank and measures the sample with a built-in refractometer and thermometer. Users can add values such as pH, nitrite, and water hardness manually. Sensor data stored and analyzed in the cloud-based manager are displayed directly via graphics, statistics, and reports – allowing deviations to be detected early. Users can also exchange experiences among members worldwide in the Liquidtool community.

Large FOV vision system
The AVR300 multi-sensor vision system has been enhanced with a 0.14 magnification lens featuring the largest field of view (FOV) on the AVR series at 2.36" x 1.90" (60mm x 48mm). X, Y, Z travel is 12" x 8" x 8" (300mm x 200mm x 200mm).
Superimage technology allows multiple images to be stitched together so more of the part can be viewed in one larger image. Together with the system’s touch probe technology, the AVR-FOV 0.14X can accurately inspect features on large or complex parts, as well as on multiple small parts.
Equipped with the M3 software package from MetLogix, a traditional mouse and touchscreen make user interaction intuitive. Auto part recognition creates a part measurement program of the desired part features for inspection, which can be saved automatically in the system or to a network.
High torque/speed live lathe tools
Live lathe tools with 5:1 and 1:5 gear boxes for high-torque and high-speed machining applications are now available.
Speeders improve surface finish and reduce cycle times when machining small holes and soft materials, without lengthy acceleration ramps. Reducers optimize the lower speed, higher torque requirements of large holes and tough materials without sacrificing horsepower.

In-line holders use ER-style collets and are available on extensions to machine between chuck jaws. Designed to fit popular lathe models, angle head versions machine in bores down to 5/8" diameter. Secondary ID machining operations such as oil grooving and keyway cutting can be integrated into turning operations. Heads and drivers are modular, and available in face and OD mount configurations.
Get curated news on YOUR industry.
Enter your email to receive our newsletters.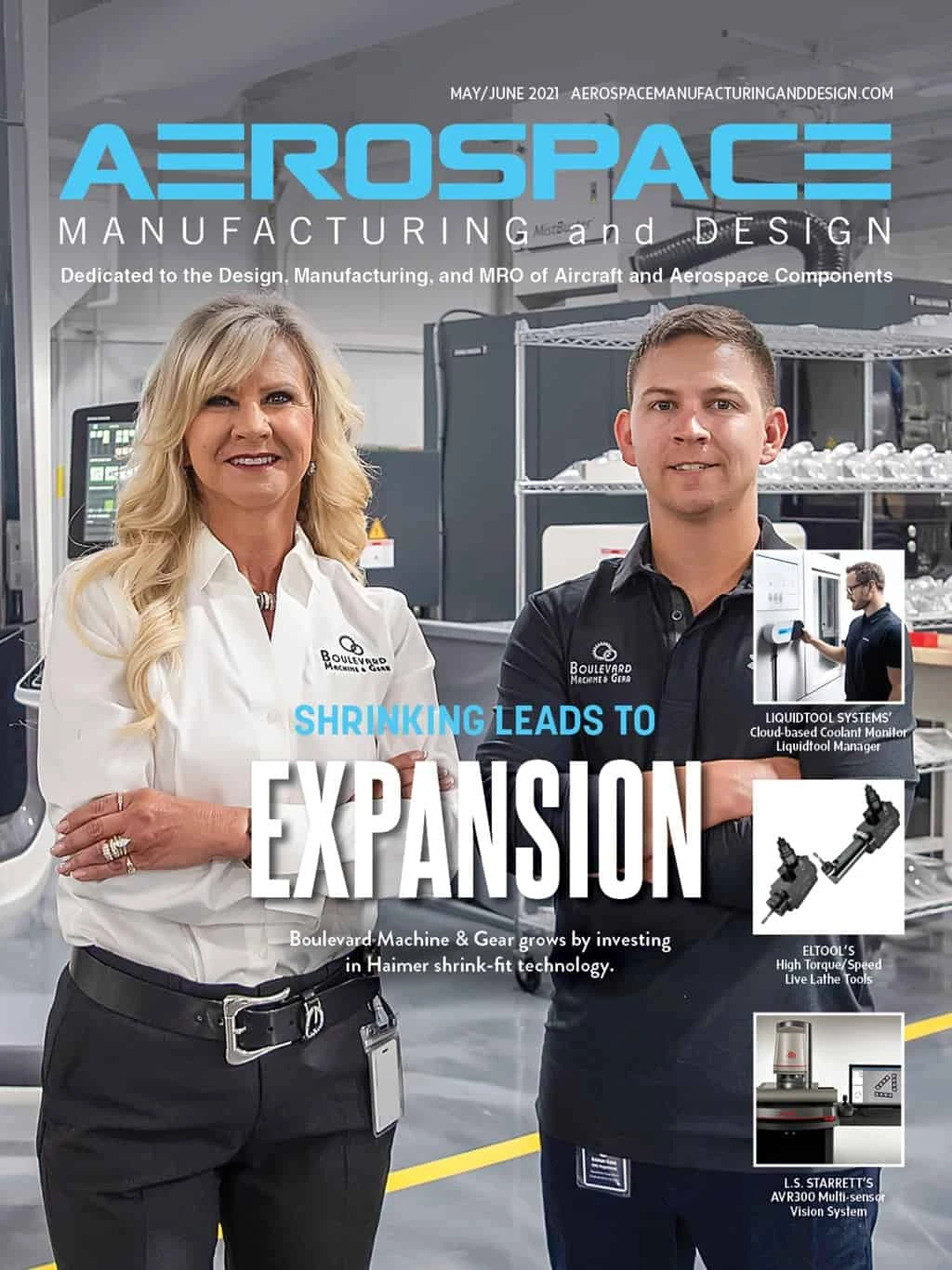
Explore the May June 2021 Issue
Check out more from this issue and find your next story to read.
Latest from Aerospace Manufacturing and Design
- AAMI project call submission deadline extended to May 12
- Jergens launches cast iron tooling column additions
- Airbus to acquire assets relating to its aircraft production from Spirit AeroSystems
- FANUC America's Cobot and Go web tool
- Chicago Innovation Days 2025: Shaping the future of manufacturing
- High-density DC/DC converters for mission-critical applications
- #59 - Manufacturing Matters: Additive manufacturing trends, innovations
- ACE at 150: A legacy of innovation and industry leadership