
AMAZEMET has adopted solutions from the Siemens Xcelerator portfolio to help build its closed-loop production chain for metal additive manufacturing (AM) materials and supporting post-processing equipment.
AMAZEMET is focused on commercializing ultrasonic atomization to provide laboratory-scale units for in-house manufacturing of powders with a tailored chemical composition suitable for applications including AM. Its team aims to broaden the scientific possibilities in materials development and metal AM – and its engineering team relies on Siemens Xcelerator to help bring its products to market.
At the core of AMAZEMET’s product range is rePowder, an ultrasonic atomizer producing metal powder from any alloy in any feedstock form and quantity. AMAZEMET also developed post-processing solutions including inFurner, a high-vacuum laboratory furnace for heat treatment processes. To accomplish this, the AMAZEMET team has adopted Siemens’ NX software for product engineering and Teamcenter X software for cloud-based product lifecycle management (PLM) and collaboration.
AMAZEMET
Siemens Digital Industries Software
Laser-based powder bed fusion solution


The Manufacturing Technology Centre (MTC) will have first access to a new industrial laser-based powder bed fusion solution, equipped with dual variable spot size nLIGHT lasers. This will allow the MTC to evaluate novel applications with materials that have previously been difficult to reliably process.
The MTC team specializes in developing advanced manufacturing processes and technologies to produce complex and large-scale AM components. The MTC wanted a system that was flexible, industrially scalable, and pushed boundaries to enable step changes in the development and productivity of new materials.
AMCM provides customized solutions based on industrialized EOS systems. The AMCM M 290-2 FLX incorporates two nLIGHT AFX lasers, offering a variable laser spot from 85µm Gaussian to 210µm donut shape, enabling a wider and shallower melt pool with more uniform temperature distribution, resulting in faster printing with improved process stability and reduced soot and spatter. The system also offers a full field overlap, meaning both scanners can reach all spots on the build plate and full flexibility is possible for build orientation.

The MTC is also developing ways to increase the speed of AM production and the size of output components. Efficient exposure processes are needed to reduce time and cost. The variable spot sizes of nLIGHT can be switched within 30ms to print contours and fine structures with maximum precision and infill hatching with accelerated throughput.
AMCM systems also feature unique long term stable atmosphere control at <50ppm. MTC will use the AMCM M 290-2 FLX for a comprehensive evaluation of pure copper printing, which is a challenging material when aiming for industrial quality and reliability. The AMCM system can also heat the build platform up to 500°C, enabling the MTC to evaluate a wide range of high-end applications, such as those in the aerospace and defense industry.
AMCMManufacturing Technology Centre
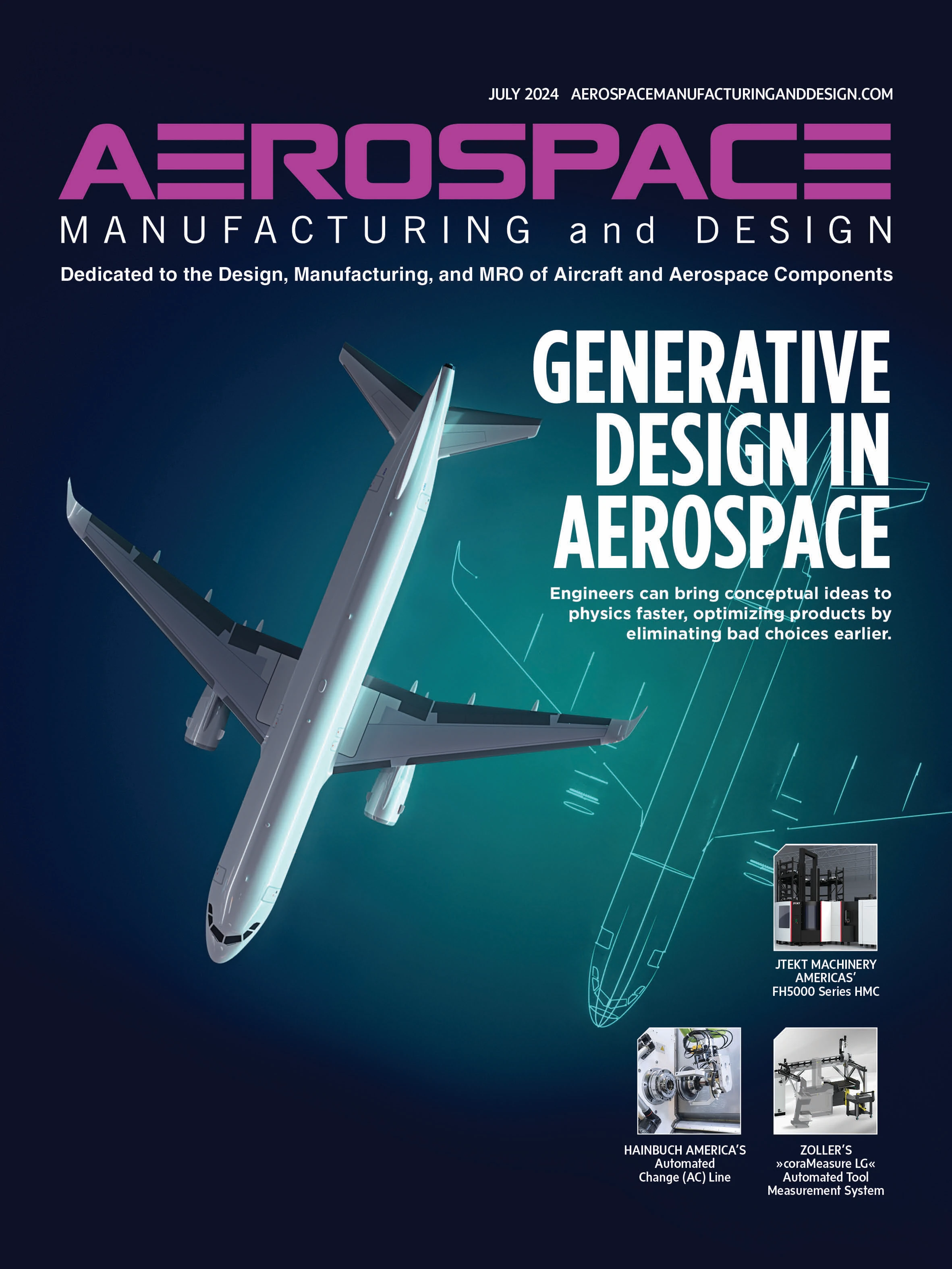
Explore the July 2024 Issue
Check out more from this issue and find your next story to read.
Latest from Aerospace Manufacturing and Design
- DEMGY Group acquires Tool-Gauge
- OES’ dual-axis yaw pitch stages
- Mastering high-temp alloys with Kennametal Inc.
- Boeing to sell portions of digital aviation solutions
- SMW-Autoblok’s KNCS-matic 3-jaw power chuck
- 3 Questions with an Expert with Allied Machine & Engineering
- Electra raises $115M to pioneer Ultra Short aircraft
- Walter’s WT26 partial- and full-profile thread turning inserts