
The only chair on an airplane without a seatbelt, lavatory structures have stringent safety requirements. Keeping passengers safe in these tiny private rooms requires extensive testing, something that has traditionally been a manual process. The Interior Systems Business of Rockwell Collins in Everett, Washington, primarily produces lavatories for commercial aircraft. Before the lavatory units can be installed in aircraft, they must be structurally tested to standards specified by the Federal Aviation Administration (FAA) in conjunction with Rockwell Collins’ customer.
“The FAA mandates a number of load cases that you have to meet,” says Jeff Whitaker, Rockwell Collins test engineering supervisor.
To test the integrity of the structures, Rockwell Collins’ test group executes a protocol that will push or pull on one or more lavatory surfaces simultaneously (see Figure 1, above). The tests ramp the force up to more than 10,000 lb max. loads, applied in different configurations by a series of hydraulic or pneumatic cylinders acting on the lavatory surfaces through mechanisms called whiffletrees, which distribute force from a single cylinder evenly across a surface through bars, poles, and linkages.
The need for improved controls
Historically, running the tests at Rockwell Collins was a very manual process, relying on the skill of a human operator who had to operate multiple hydraulic or pneumatic cylinders simultaneously.
“It could take 20 minutes to run a test, with the results recorded on a PC via LabVIEW software,” Whitaker says.
Besides being time-consuming, the human element reduced precise repeatability from one test to the next. Figure 2a (page 65) shows the forces applied by four cylinders in a typical test when
The test group wanted to better control the hydraulics and settled on the idea of closed-loop control via an electronic motion controller. The advantage would be
Selecting a motion controller
To fulfill these requirements, the Rockwell Collins test group selected the RMC150 8-axis motion controller from Delta Computer Systems Inc. of Battle Ground, Washington (see Figure 3, right). The motion controller gets a force feedback reading from a load cell attached to each cylinder. Precise hydraulic or pneumatic control of the force is accomplished by the Delta motion controller via proportional servo valves connecting directly to the RMC150.
During a structural test, the motion controller slowly increases the load being applied
“So far, the largest number of cylinders that we’ve controlled in a single test is nine,” Whitaker says. “We can go up to 8 axes with a single RMC150, so we had to use two RMC150s for that test.”

Tuning the motion
To program and tune the motion, the Rockwell Collins team used RMCTools – development software from Delta Computer Systems. RMCTools includes Plot Manager, allowing the user to view key motion parameters in real time as the system operates (see Figure 2b, top right). This is helpful for motion tuning, as actual values obtained from the transducers can be plotted against target values generated by the motion program, to show an error that can be reduced by tuning.
“It’s easier to tell from a graphical reading that something’s wrong,” Whitaker says. “If there’s a problem, it shows up on the plot first.”
The RMCTools development package also includes graphical Tuning Wizard software which simplifies the task of setting the control loop gains for optimal operation.
“When we switch between hydraulic and pneumatic components, we use a different set of gains for the control loop parameters,” says Thor Stenfjord, Rockwell Collins test engineer. As Figure 2b shows, the force plots with Delta’s RMC150 in control allow actual forces being applied to precisely match the target forces (target and actual plot lines overlap).

Visualizing results
“We previously depended on LabVIEW for handling data collection and control,” Whitaker says. “Now with the Delta motion controller managing the motion axes, LabVIEW is primarily used for data acquisition.”
RMCTools’ display capability is useful as an HMI during test operations, in addition to being a development environment. The Rockwell Collins test operator station includes two displays, one for the LabVIEW screen and one for motion plots the Delta software generates.
“Improved testing speed, efficiency, accuracy, and repeatability are the advantages of using closed-loop control of our test operation. With closed-loop control of the force loading system, the time required to run a typical test is reduced from 20 minutes to approximately three minutes,” Whitaker concludes.
Delta Computer Systems Inc.www.deltamotion.com
Get curated news on YOUR industry.
Enter your email to receive our newsletters.
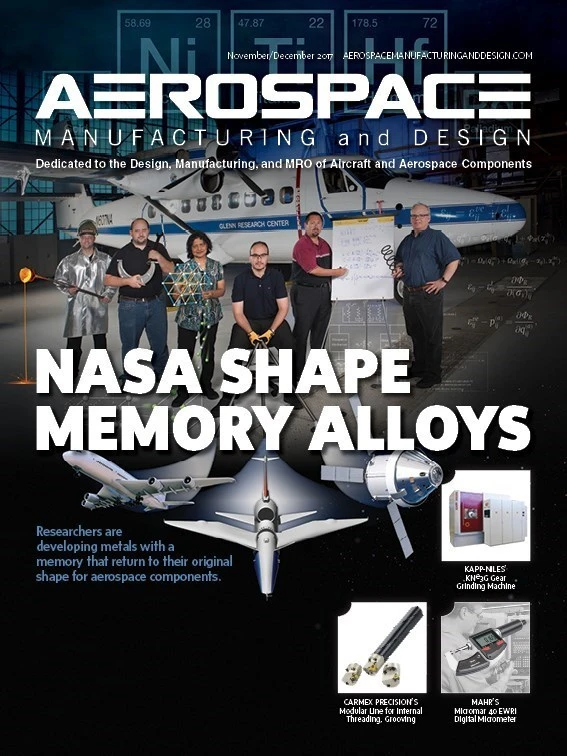
Explore the November December 2017 Issue
Check out more from this issue and find your next story to read.
Latest from Aerospace Manufacturing and Design
- AIX showcases the future of air travel
- Sunnen Products' PGE-6000 gage
- #41 Lunch + Learn Podcast - SMW Autoblok
- Revolutionizing aircraft design without sacrificing sustainability
- GE Aerospace awarded subcontract for FLRAA next phase
- KYOCERA Precision Tools publishes 2025-2026 Indexable Cutting Tools Catalog
- BOC Aviation orders 120 Airbus, Boeing jetliners
- Mazak’s INTEGREX j-Series NEO