
©Konstantin L - stock.adobe.com

Fiber optic connectors in military aircraft applications must be extremely durable since they are often exposed to punishing temperatures, high moisture, harsh wind, and excessive shock and vibration. However, as rugged as these connectors are, they still require careful cleaning before connecting the end-faces.
Dirty connector problems
End-face contamination can come from salt fog residue, hydraulic fluid, jet fuel, atmospheric dust, penetrating oils, and vehicle emissions. Even removing protective dust caps from the factory that cover end-faces may cause contamination. These contaminants, if left between the mated termini pairs, will normally spread across end-face surfaces, altering signal paths and changing the refractive index, causing signal degradation. Severe contamination could cause complete system failure.
Friction causes contamination
One pervasive source of end-face contamination is wear debris caused by aircraft motion while in operation. Constant vibration creates surface-to-surface wear between individual components of mated connectors, creating dust contaminants. Commonly used MIL 38999 cylindrical connectors with MIL 29504 termini are most often used for cable-to-panel input/output (I/O) applications in aerospace. Spring loaded termini maintain the physical contact when exposed to high vibration, impact, and shock motions. However, the strong contact force that holds pair mated termini together also will grind dust particles into ferrule surfaces, scratching end-faces.
End-face contamination worsens due to electro-static charge buildup on ceramic and composite ferrule materials. Ferrules and glass fibers are dielectric and act as an electrical insulator, holding a static charge. Charged dust particles will be attracted to oppositely charged fibers and ferrules. MIL 38999 and MIL 29504 allow end-face geometry to be a convex curve, concentrating electro-static charges at the apex of the mated connectors and physically drawing dust contamination to physical contact. The lower the humidity, the greater the static issue.

MIL 38999 connectors, designed to survive the extreme mechanical stresses and harsh environments of military aircraft battles, are too deep to be cleaned with traditional fiber-optic cleaning tools, and disassembling adapters and connectors to clean fiber end-faces would be time consuming and expensive. Special tools and methods are required to clean them effectively. To achieve optimal performance from the aircrafts’ optical network, a fiber technician should:
Prepare for cleaning – When possible, clean in an enclosed area, such as an aircraft hangar. Cleaning fiber on the aircraft ramp exposes the connectors to dust and debris.
Extensively clean the outside of the mated fiber connector with aerosol duster and general cleaning wipes before disconnecting the end-faces. However, do not use duster products directly on end-faces after disconnecting them since movement of duster gas creates static and draws dust and other contaminants to the end-faces.
Clean inspection tools and adapters to prevent cross-contamination.
Choose the right cleaning fluid – Optical-grade cleaning fluids engineered for fiber optic end-faces are best. Choose ultra-pure, non-flammable, residue-free cleaning fluids that are safe for glass, ceramic, and plastic surfaces. Fluids should come in hermetically sealed (un-refillable) containers to prevent cross-contamination and spilling. Fast-drying, static-dissipative fluids also eliminate additional drying, saving time.
Avoid using water-based cleaners because they are slow to dry and freeze at low temperatures. Also, avoid using isopropyl alcohol (IPA). Although inexpensive, alcohol is flammable and must be kept away from ignition sources. IPA also readily absorbs moisture from the air, contaminating it.
Use wet/dry cleaning to dissipate static – During wet/dry cleaning, use a section of an optic-grade cleaning wipe, dampened with a static-dissipative cleaning fluid. Wipe the connector end-face starting at the damp area, moving in one direction toward the dry area of the cleaning wipe. This removes contamination and dissipates electro-static charges in one step. Port-cleaning sticks or clicker devices should be dampened with cleaning fluid first and then used to clean the end-face.
Opt for high-grade optical wipes – Less expensive paper wipes can rarely clean microscopic contamination from optical connectors, as they tend to shred easily. As they degrade, they can leave lint and debris behind. They often generate high static charges, making their use counterproductive. High-grade, optical wipes that don’t lint or generate static charges are preferred. Economize by purchasing smaller wipes that reduce waste. Use wipes in packaging that minimizes static charges as individual wipes are dispensed. Leaving wipes in the package until ready to use ensures they stay clean, preventing waste. Use wipes only once to prevent cross-contamination on network end-faces.
Use cleaning sticks for better cleaning – Although mechanical clickers are often well suited for cleaning connectors, they are not always sized for cleaning termini in hardened connector housings. Combine a cleaning stick and static-dissipating cleaning fluid to clean connectors mounted in hard-to-clean alignment sleeves. Cleaning sticks conform to end-face geometry and can clean the entire end-face without disassembling the connector or adapter. They clean the terminus surface and eliminate issues associated with contaminates migrating into the signal path. The cleaning fluid also increases local humidity, creating a dissipative path to remove any incumbent static charges.
When cleaning, dampen the cleaning stick with cleaning fluid first. After inserting the stick into the connector, rotate it about six times in the same direction. Avoid extreme force and don’t excessively scrub the end-face as that can cause scratching, pitting, or scarring. A cleaning stick should be engineered to match the configuration of the end-face and be non-linting for optimal cleaning. A well-engineered cleaning stick will also make incidental contact with the alignment sleeve sidewalls allowing cleaning fluid to defuse static charges, so any debris on the alignment sleeve doesn’t jump onto the clean connector end-face during insertion. Cleaning sticks should be kept in their package until ready to use to prevent soiling or damage.
Inspect-clean-inspect – Always inspect, clean, and reinspect all termini on both ends of a connector pair before mating. Visual inspection identifies permanent defects, scratches, pitting, and contamination that can interfere or damage optical termini surfaces.
Take time to visually inspect the termini to identify possible contamination sources and try to eliminate the root problem. Only when the terminus surface is free of contamination are connector pairs ready to be mated. Taking extra care to clean and inspect both ends before mating will ensure military aircraft fiber optic network reliability and longevity.

Create a cleaning plan
The frequency needed to clean fiber optic connectors on an aircraft will vary but technicians should implement a maintenance program.
Cleaning procedures are straightforward. Personnel should follow the technical manual to the letter, so the fiber system is properly cleaned and maintained. If technicians don’t rush the process, connections will have greater integrity throughout the fiber optic system’s life.
In addition to regular maintenance, fiber connections should be cleaned if the system shows any communication signal degradation.
Find a cleaning partner
When choosing fiber optic cleaning fluids, tools, and methods, technicians should seek the help of an experienced supplier specializing in military fiber optic cleaning. The supplier can recommend specific products engineered for military use that effectively clean unique military connectors used within harsh environments.
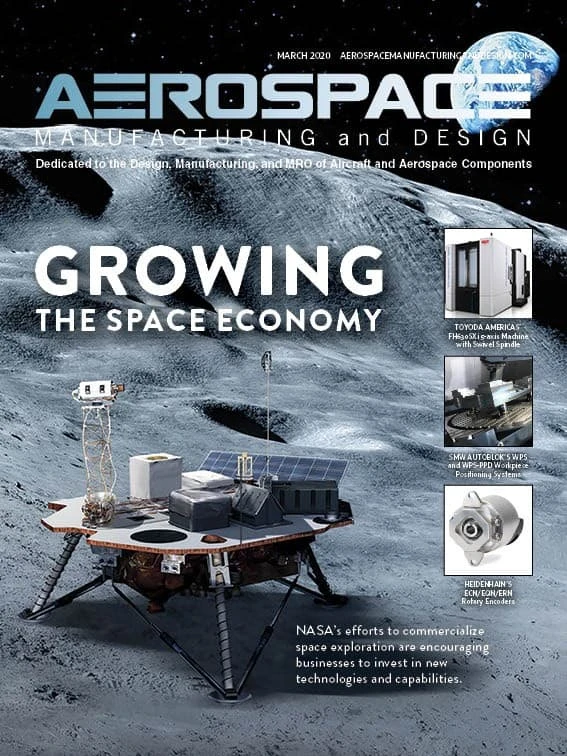
Explore the March 2020 Issue
Check out more from this issue and find your next story to read.
Latest from Aerospace Manufacturing and Design
- Essential strategies to protect your data
- NASA selects instruments for Artemis lunar terrain vehicle
- Twin-cutter boring head
- Bell awarded funding for X-plane build phase of SPRINT program
- Shaft coupling clamps
- #46 Lunch + Learn Podcast with SMW Autoblok
- Gleason Corp. acquires the Intra Group of Companies
- Thread milling cutter reduces cutting pressure, vibration