_fmt.png)
Seals and gaskets must perform in some of the most challenging aircraft conditions, solving high temperature, flame retardance, corrosive fluids, or extreme pressure challenges. Knowing which seal or gasket best addresses the need is paramount, and a trusted partner can identify products such as:
- A radial seal with rectangular cross-section that will outlast and outperform the standard radial seal for more fly time and revenue
- A gasket with single-fastener access that maintains a firewall barrier to save hundreds of hours in labor during installation
- A seal that can be vulcanized directly to metal with no adhesive that might burn off, eliminating fasteners
_fmt.png)

Understanding each application’s requirements, conditions, and related factors is crucial to selecting the appropriate seal and gasket for the job. Engineers and designers partnering with a manufacturer can develop a customized solution, selecting the appropriate materials in the proper lay-ups and configurations to successfully meet project needs.
Partnerships count
A manufacturing partner should be knowledgeable about the aerospace industry, have strong research and development (R&D) capabilities, a robust engineering department, and a proven history of success.
A manufacturer must be appropriately certified, understand the importance of industry technical specifications, and willing and able to meet ever-evolving needs by taking advantage of new technologies.
Strong R&D and engineering departments are critical to partnering with an OEM to create customized solutions. As the industry pushes to create more cost effective, fuel efficient, sustainable aircraft, manufacturers must respond and be ready with solutions that meet those needs.
A tailor-made solution for an aviation project can take many months (even years) to create. From the first inquiry to final production, many conversations, meetings, and revisions will likely occur, and knowing that a partner will see it through to the end offers reassurance for the substantial investment of time, energy, and dollars.
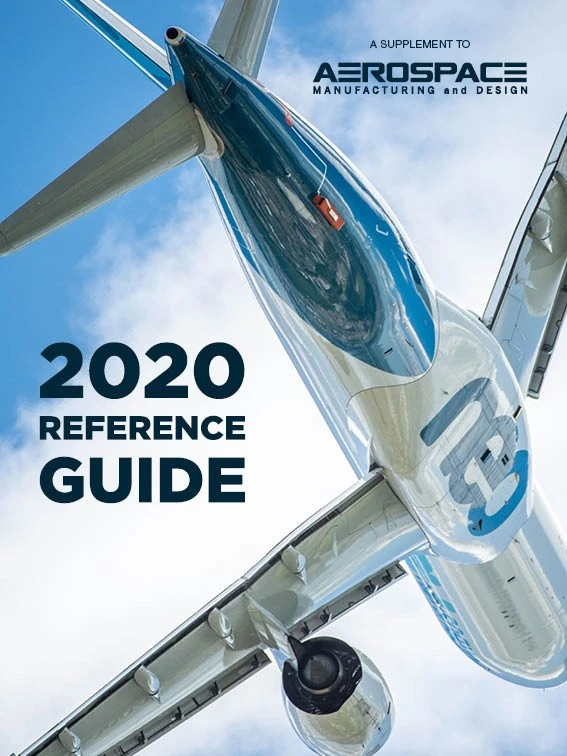
Explore the AMD Reference Guide 2020 Issue
Check out more from this issue and find your next story to read.
Latest from Aerospace Manufacturing and Design
- AIX shows aircraft interiors are a strategic priority for global airlines
- Machine Tool Builders Roundtable: Turn equipment into expertise
- No time to waste: How to machine MedTech parts more efficiently
- The 5 Best and Fastest Spindle Repair Services
- Mill smarter, not harder: How collaboration optimizes production
- Be proactive – stay ahead of tariffs and other economic and supply chain curveballs!
- Taiwan’s China Airlines orders Boeing 777X passenger, freighter jets
- Reamer re-tipping extends life of legacy tooling