
A weak link in even the most well-thought-out plans to optimize productivity can derail a CNC machining process. For Novato, California-based OMW Corp., applying advanced machine tool technology and cutting techniques that promise greater throughput were thwarted by inefficient chip and coolant management.

“We’re a contract CNC shop handling more than 2,000 discrete parts for our customers,” says OMW Vice President Michael Leeds. “We recently added an Okuma 4000 series horizontal machining center (HMC) with a standard 400mm pallet and a true 5-axis table to produce parts for an aerospace customer that makes launch vehicles for satellites. We run a wide range of components that have critical features and tight tolerances. The base material will vary from aluminum (75%) to high-nickel steel alloys (23%) and even copper and brass alloys (2%).”
Among the machining methods OMW employs to meet customer requirements are 3D surfacing that produces very light, fluffy chips, and trochoidal milling that creates narrow, long, stringy chips 0.02" to 0.03" wide. Trochoidal milling improves tool life and reduces cycle time by using higher spindle speeds, keeping the cutting tool moving continuously and maintaining low radial engagement, which produces the thinner chips.
“Although the machine tool did everything we expected, we had repeated stoppages because the chip conveyor wasn’t able to handle these types of chips. The light, fluffy and long, stringy chips floated on top of the coolant and 30% to 40% would float off the coolant from the conveyor into the machine sump,” Leeds says.
The accumulation of chips in the sump required daily maintenance in the form of removing covers, manually straining coolant to remove the chips, and mucking out the sump at the end of a shift. Worse, coolant passing through the pumps and nozzles deposited fines that clogged the system and damaged pumps that had to be periodically rebuilt or replaced.
“Production was so impacted, it made it impossible to use the machines on aluminum, so we switched to making parts from steel,” Leeds explains. “However, the chips continued to restrict coolant flow which made it difficult to maintain proper cutting area temperatures. That increases tool wear and affects ability to maintain tolerances. When pumps and nozzles get clogged and you don’t have proper coolant and chip removal, you risk destroying everything: cutting tools, the part, and fixturing. Plus, if your coolant wash slows down, the fines and the chips collect in the pallet changing station, which can stop the machine in its tracks.”

Although OMW has LNS Turbo chip conveyors on its other machine tools, the new Okuma HMC was equipped with a different brand. When Leeds discussed his problem with the LNS representative, he learned a new version of the LNS Microfine line of chip and coolant management systems was in development and well-suited to this application. The MF4 filters machine coolant to 50µm using a dual conveyor system and self-cleaning filter drum. It’s suitable for any chip type or material. The upper conveyor handles heavy loads including chunks, stringy, bushy, and large chips. The scraper-type lower conveyor removes the remaining small particles and deposits fines trapped by the filter drum onto the incline, delivering particle-free coolant to the machine sump.
“The whole LNS team was great to work with and were here for the installation to make sure everything worked properly. Most important, the MF4 does exactly what we need it to do: keep production running smoothly. Since this chip conveyor was installed, we’ve never had to clean out the machine sump. There are no pump or nozzle issues, chips wash out efficiently, coolant flows as it should, and the sump is clean, clean, clean. I would absolutely spec this chip conveyor for any machine running these kinds of processes,” Leeds concludes.
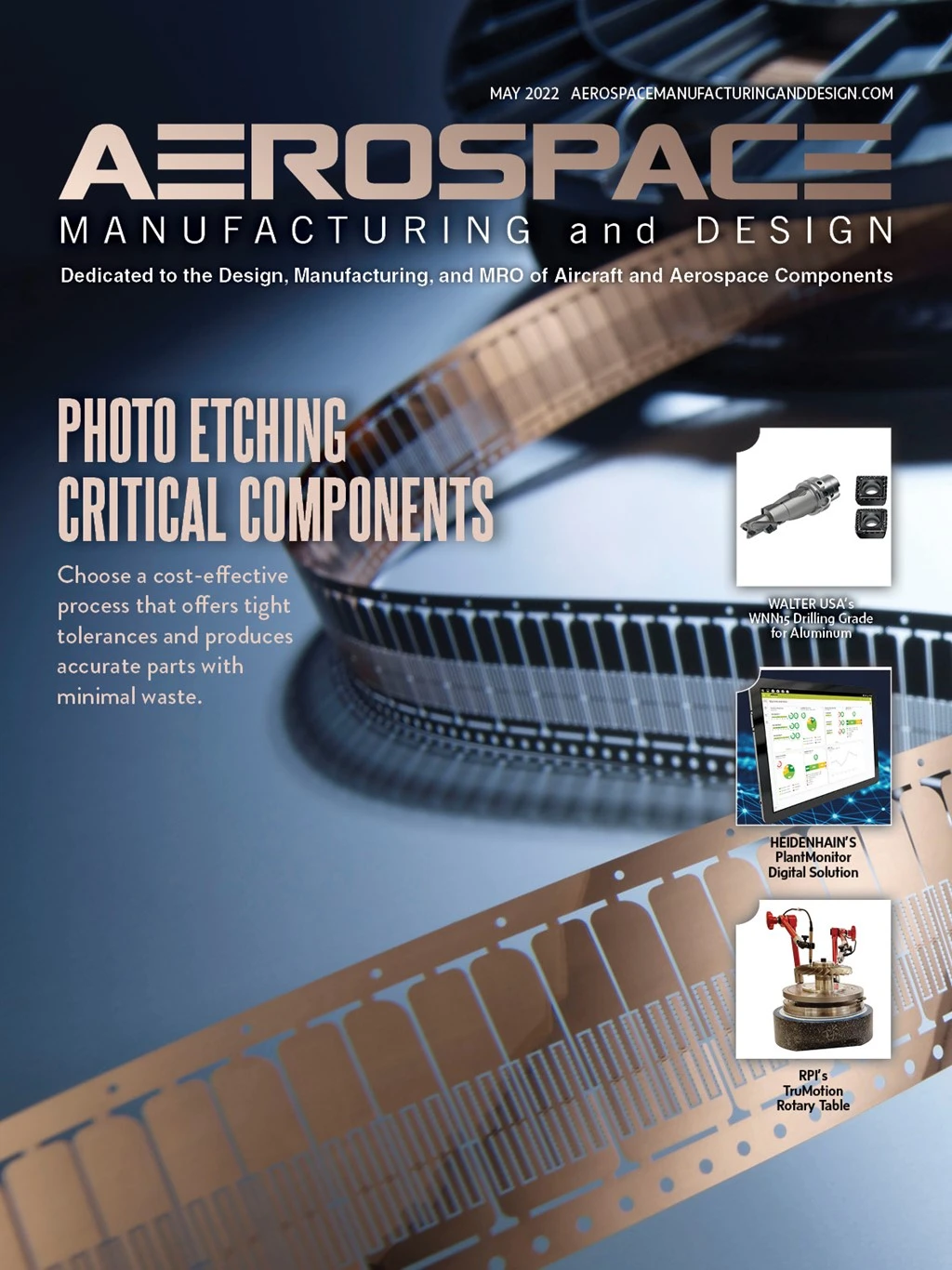
Explore the May 2022 Issue
Check out more from this issue and find your next story to read.
Latest from Aerospace Manufacturing and Design
- Heart Aerospace relocates to Los Angeles
- Fixtureworks introduces Stablelock Clamps
- Piasecki acquires Kaman's KARGO UAV program
- PI Americas’ long-travel XY piezo nanopositioners-scanners
- AAMI project call submission deadline extended to May 12
- Jergens launches cast iron tooling column additions
- Airbus to acquire assets relating to its aircraft production from Spirit AeroSystems
- FANUC America's Cobot and Go web tool