
CFM56 family aircraft engines power more than 13,400 commercial and military aircraft worldwide. However, historical maintenance data on the CFM56 shows a tendency for fretting-induced microcracking in the dovetail edge of the first-stage high-pressure compressor (HPC) blade, posing a significant safety concern.
Preventing fretting fatigue in the dovetail historically required a three-step process – a thermal spray anti-gallant, shot peening, and a dry film lubricant. However, dry lubricants wear away during service. Fretting-induced shear cracks can quickly penetrate the shallow protection offered by shot peening (approximately 0.005"), requiring repeated applications to remain effective. Frequent, stringent blade inspection was required to detect cracks. If the inspections found a blade with fatigue damage, the entire shipset required replacement.

In addition to the labor cost of inspections and blade replacement, frequent inspections require substantial downtime. End users of the engine sought a maintenance, repair, and overhaul (MRO) cost reduction solution. With so many engines in service, any savings in inspection time or repair cost could have major effects across the industry.
Low plasticity burnishing (LPB), an alternate method of treating metallic or alloy-based components, offers a solution. Like shot peening and laser shock peening, LPB introduces beneficial residual compression into a component to enhance fatigue strength and mitigate fretting. Tensile service stress in metallic components induces crack formation from stress concentrations formed by fretting surface damage. By producing a layer of high-magnitude compression substantially deeper than the surface damage, LPB prevents fatigue crack propagation from the fretting damage.

Rather than hitting a component with a shot or shocking the surface with a laser beam, LPB rolls a tool across the surface of the part under load. As the tool rolls across the surface, the surface yields in tension, rebounds elastically, and is left in residual compression. LPB introduces compression by essentially the same mechanism as shot peening, but without the random repeated impacts, dents, and high cold work that can damage the surface. The typical target depth of LPB compression is about 1mm.
Application
LPB is a CNC machine add-on, so the depth and magnitude are designed for each application and performed in a standard machine-shop environment using CNC mills, lathes, or robots. The application is strictly closed-loop, servo-regulated with quality control exceeding Six Sigma. The burnishing force and resulting compression can be adjusted on the fly at every point on the component to achieve the optimum residual stress distribution for fatigue performance.

LPB return on investment
LPB lowers cold work
Shot-peening applies compressive residual stresses by hitting a component’s surface randomly and repeatedly with the peening media, creating dimples. The repeated deformation of the surface creates excessive cold work, often more than 50%, leaving the beneficial residual stresses more susceptible to thermal and mechanical relaxation in service. LPB, however, produces only minimal deformation, just enough to achieve the required compression. Compression from LPB treatment will remain stable even at higher temperatures at which shot peening-induced compression relaxes.
Typical fretting-induced mode II shear cracks in the CFM56 are shallower than 0.005". The shear cracks form at the edge of contact between the blade dovetail face and the rotor disk post face. These cracks transition into mode I fatigue cracks that propagate rapidly due to vibratory stresses during normal engine operation. With induced compressive residual stress deeper than 0.025", complete mitigation of mode I crack propagation is possible. LPB produced compressive residual stresses to a depth greater than 0.040", which will completely arrest fretting-initiated fatigue cracks. When applied to a blade with existing fretting fatigue damage, LPB provided more than 10x life improvement of a new blade without fretting damage.
Lambda Technologies Group
https://www.lambdatechs.com
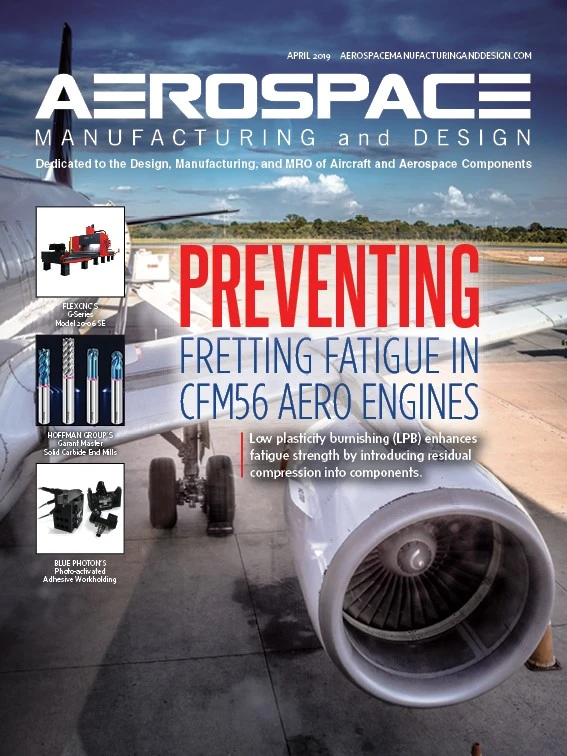
Explore the April 2019 Issue
Check out more from this issue and find your next story to read.
Latest from Aerospace Manufacturing and Design
- Trelleborg acquires Aero-Plastics
- Industrial automation products, enclosed encoders
- #61 - Manufacturing Matters: CMMC roll out: When do I need to comply?
- AIX shows aircraft interiors are a strategic priority for global airlines
- Machine Tool Builders Roundtable: Turn equipment into expertise
- No time to waste: How to machine MedTech parts more efficiently
- The 5 Best and Fastest Spindle Repair Services
- Mill smarter, not harder: How collaboration optimizes production