_fmt.png)
Commercial aerospace manufacturers want profitable growth in the long term. How can CERATIZIT help aerospace manufacturers achieve this?
DC: Today’s aerospace OEM and Tier 1, 2, and 3 suppliers can benefit from CERATIZIT’s extensive tool portfolio and deep industry knowledge. We deliver optimal cutting performance, precision, and quality. Whether they work with aircraft and assembly, mill parts of turbine engine components, turn sections of the landing gear, or drill holes for wing ribs, CERATIZIT offers indexable and solid carbide solutions that help manufacturers achieve tight tolerances, easily handle difficult materials, and improve cycle times to meet ever-growing demand.
Specifically speaking about aircraft assembly, what CERATIZIT solutions solve manufacturers’ toughest challenges?
DC: For today’s advanced materials such as fiber composites, aluminum, titanium, and superalloys, we tap into 50 years of extensive experience with our KLENK tooling line. Special diamond-coated carbide drills, milling cutters, reamers, counterbores, and multi-tools, were developed for these difficult-to-machine materials for manual, semi-automatic, and automatic drilling at a lower cost per quality hole. Specially designed uncoated and diamond-coated solid carbide drills, reamers, CFRP mills, counterbores, and multi-tools to drill/countersink also reduce your cost per hole.

Modern turbine engines are expected to provide more power while conserving resources. How can CERATIZIT help attain this?
DC: Customers get precise machining of turbine blades, fan cases, and blisks made from titanium, HRSAs, and Inconel by taking advantage of our wide tooling portfolio. CERATIZIT’s cutting solutions offer the latest PVD-coated carbide ISO turning tools, solid carbide end mills, and drills. KOMET brand solutions, such as reamers, provide precise bores with excellent surface quality in HRSAs. Manufactured in the U.S., these end mills, drills, and reamers easily handle tough materials whether you are grooving the inner diameter of a blisk or boring precise holes in a titanium combustion case.
What can we expect for tool life when machining these advanced materials?
DC: Machining difficult materials can result in short tool life. You can extend tool life by using tools with Dragonskin coating. Just like it sounds, this advanced coating technology is as tough as the skin of a dragon. It provides an additional layer of protection for high heat, up to 1,000°C, and extreme wear that comes when machining aerospace components.

About CERATIZIT
CERATIZIT Group has been a pioneer in developing innovative solutions for tooling and hard material technologies for almost 100 years. For aerospace and other industries, we continuously develop and test products and processes to guarantee your business meets its strategic goals to ensure future profitability. In the U.S., we proudly engineer and manufacture highly specialized, precision cutting tools for drilling, boring, reaming, milling, and turning within the Cutting Solutions by CERATIZIT, KOMET, WNT, and KLENK brands.
To learn more about the aerospace capabilities within CERATIZIT USA, visit: https://cuttingtools.ceratizit.com/us/en.html
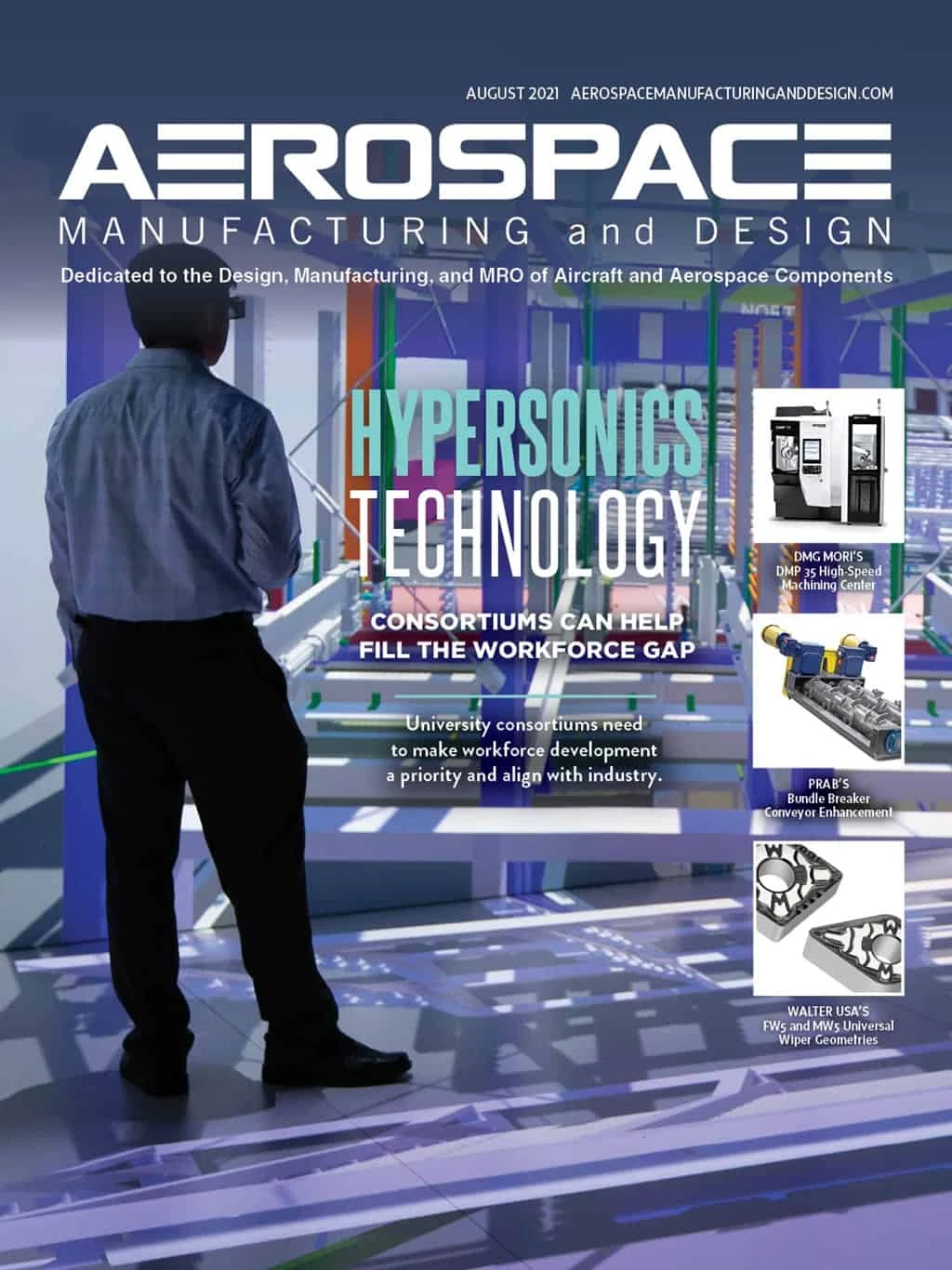
Explore the August 2021 Issue
Check out more from this issue and find your next story to read.
Latest from Aerospace Manufacturing and Design
- Registration is open for April’s Manufacturing Lunch + Learn!
- Natilus begins search for new home to build world's most efficient commercial aircraft
- Aerospace Industry Outlook webinar is back by popular demand
- Automation Webinar with Visual Components
- PrecisionX Group expands manufacturing operations
- Creaform Metrology Suite expands capacities
- United Performance Metals acquires Fabrisonic
- OES’ 30mm vertical lift stage