
G-9610 carbide insert grade offers a 25% increase in material removal rate and up to 100% increase in tool life versus the competition when machining titanium.
Using a PVD coating combined with a proprietary sub-micron substrate, G-9610 provides added productivity for turning titanium-based alloys. The smooth and lubricious coating is wear-resistant and chemically stable, protecting the heat-resistant substrate and allowing for higher speeds and extended tool life in continuous cuts. Other key attributes of G-9610 include:
- High resistance to built-up edge (BUE), chemical wear, abrasive wear, loss of hardness at high temperatures
- Best applied at higher speeds, moderate feed rates Retains a sharp edge longer, relieving cutting forces, excessive heat
- Inserts in grade G-9610 are available now in various geometries and chipforms
Greenleaf Corp. https://greenleafcorporation.com
Pneumatic clamping vise

The pneumatically operated clamping force block, Tandem PGS3-LH 100, can be directly mounted on machine tables, dividing heads, or Vero-S NSL 150 machining center clamping stations by an integrated flange. The compact design and square shape ensure accessibility, enabling a 6mm stroke per jaw with a clamping force of 4,500N and a repeat accuracy of 0.02mm.
Features include a chip-repellent design – the surface-treated components in the force flow and long base jaw guides prevent the chuck jaws from buckling under load. The vise can be equipped with all standard top jaws with tongue and groove (KTR, KTR-H) Schunk chuck jaws. With lateral air connections and built-in keyways on the bottom, the vise can be installed immediately in any machine tool.
PGS3 and the Vero-S modular quick-change pallet system automate workpiece clamping and quick setup changeover, reducing setup times to seconds.
Schunk Inc. https://schunk.com
3-to-5 axis vertical jig borer

The PJ812 CNC vertical machining center offers jig borer precision for boring, milling, drilling, and tapping.
A thermal compensation system employs sensors on the machine faceplate and inside the spindle to minimize temperature-change effects on part accuracy and reduce temperature-generated displacement by 60% and Z-axis thermal growth and deflection by 30%. Cooling systems for slideway lubrication and ball screw cores stabilize axis feed precision.
Mechanical design features that maximize machine rigidity and accuracy include hardened and ground tool steel box slideways and contact elements that enhance acceleration, reduce stick-slip, and allow for feed accuracy of 0.1µm. Another proprietary engineering detail drastically improves the static rigidity of the Z-axis to >6x that of conventional Z-axis arrangements.
Mitsui Seiki USA Inc. https://www.mitsuiseiki.com
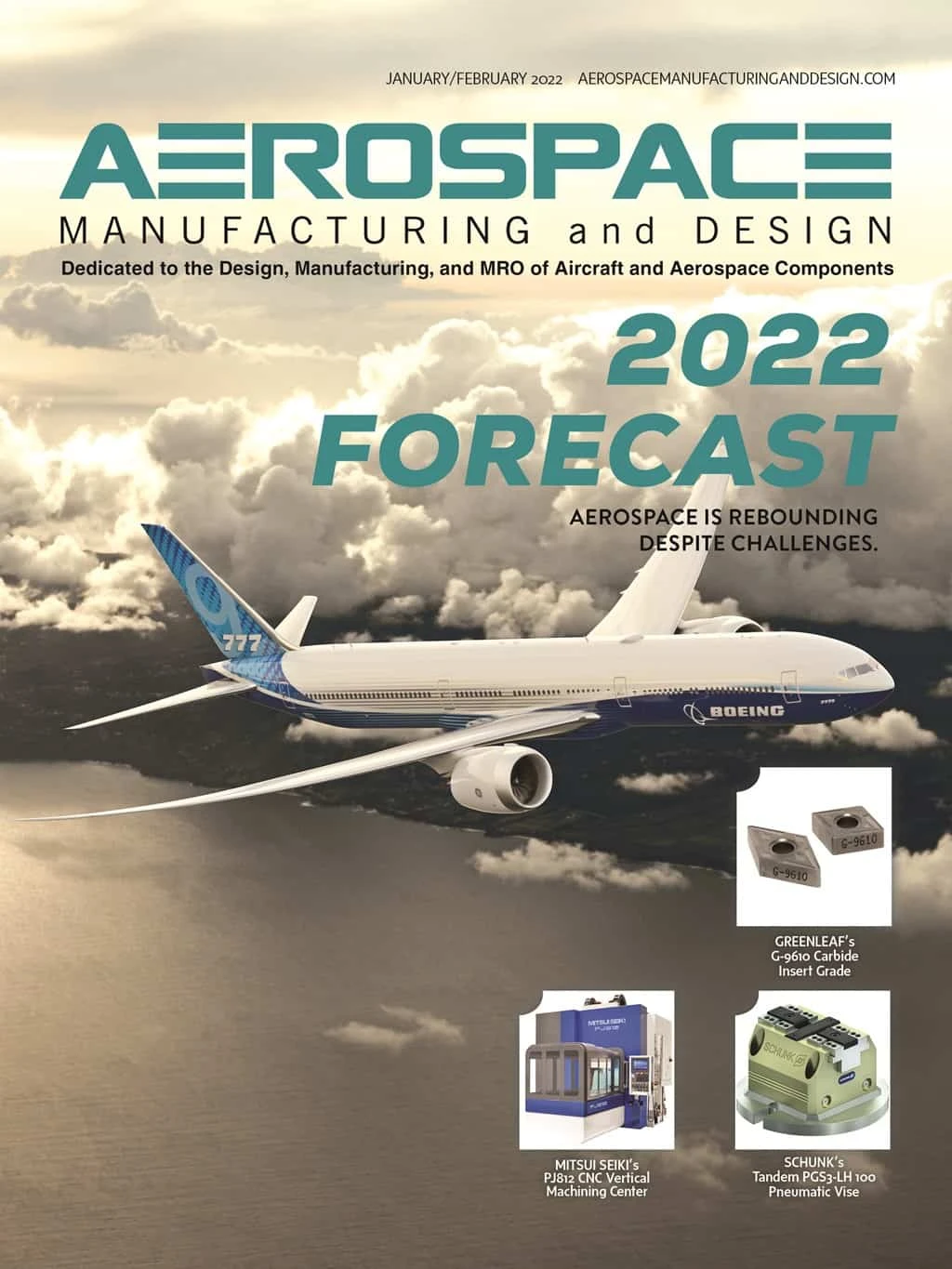
Explore the January February 2022 Issue
Check out more from this issue and find your next story to read.
Latest from Aerospace Manufacturing and Design
- Revitalizing the Defense Maritime Industrial Base with Blue Forge Alliance
- Safran Defense & Space opens US defense HQ
- Two miniature absolute encoders join US Digital’s lineup
- Lockheed Martin completes Orion for Artemis II
- Cylinder CMMs for complex symmetrical workpieces
- University of Oklahoma research fuels UAS development
- Motorized vision measuring system
- Everyone's talking tariffs