
Aerospace engineering test cells play an important role in ensuring the safety and performance of aircraft and spacecraft. Therefore, designing and building a test cell requires a commitment that includes a high level of expertise and attention to detail.
Because of the complexity of aerospace engine test cells, it’s not uncommon for a manufacturer to maximize the life expectancy of legacy equipment, which can result in test cells lasting as long as 50 years, but requiring continued improvements, adjustments, and repairs. One key challenge in building or upgrading an aerospace engineering test cell is the sheer complexity of the systems – from fuel and environmental control systems to automated technologies. It’s critical for each aspect to be carefully integrated and calibrated to ensure accurate testing and quality data. In addition, the design of the test cell must meet a wide range of regulatory and safety standards. While the goal of engine test cells is to offer vital data for improved efficiencies, product success, safety, and innovation, it’s essential to know when it’s time for a new or renovated facility, and how to tackle such a large-scale project. From designing and constructing the building envelope to integrating and commissioning the equipment, every step needs to be carefully planned and executed to ensure accurate and reliable results.
Test cell needs
As air travel increases, improving efficiencies and throughput becomes paramount for manufacturers. Advancements include shifts to new propulsion technologies, renewable fuels, and electrification to enhance efficiency and sustainability. Developments also include expanding production to keep up with increased demand for many aging test facilities. Because they represent huge capital assets, organizations will stretch their test cells’ life expectancy as much as they can with ongoing maintenance, but that can’t last forever, and this solution doesn’t address increased capacity these aging facilities can’t handle. It drives a need for aerospace manufacturers to construct new, additional, or remodeled facilities that can effectively address throughput goals now and in the future. Manufacturers committing to new or renovated engine test cells reap the benefits of decreased downtime and reduced facility upkeep and maintenance, in addition to more efficient or expanded testing abilities.
Today’s market challenges call for consistent budgeting and long-lead planning to manage volatile supply chain disruptions that can impact equipment procurement schedules, access to certain materials, and overall costs. Labor shortages and a shifting employment environment have changed the distribution of labor across most organizations, creating new challenges for organizations looking to make proactive test cell improvements or additions with limited staff availability and expertise. Because many aerospace test cell facilities haven’t been upgraded for decades, few internal facility managers, end-users, or executives have seen such large-scale renovation or construction of their test cell facilities. If the test cell has existed long enough, current employees may not have used anything else, increasing the likelihood of continuing patchwork fixes rather than committing to test cell growth. For an upgraded or new aerospace facility project to be successful, manufacturers must understand the core steps driven by expert insights.
Integration is key to success
When a new test cell project is necessary, thorough planning informed by industry expertise is a must. Consider the following essentials when planning, constructing, and implementing the next test cell project:
Design from the inside out, starting by defining testing criteria. Aerospace engineers, despite having extensive knowledge of test cells, tend to not be included in the planning process for the overall facility upfront. Often, design firms are contracted by leadership for the construction of the facility, meaning the initial focus of a project is on the facility as the foundation of planning. It seems easier to get started on the building side of a project when it’s vital to start with test cell criteria, equipment, and design first. This makes integration a central focus at every stage of the project. It’s difficult to effectively select equipment or design systems, let alone define the dimensions of a component or building, before truly understanding the data the core test is seeking.
Ensure all critical elements of the facility and test cell are integrated seamlessly. Lack of integration of equipment and control systems within the facility can result in an increase in the length of the project schedule, higher costs due to redesigns, added scope to contractors, or limiting the testing capability because a critical component was missed. This can be accomplished through planning, design, construction, and handoff stages with a dedicated systems integrator who can communicate with all project stakeholders. A systems integrator brings experience and a bird’s eye view to address the project holistically, helping companies gain a competitive advantage, improve efficiency, save time and money, and make better use of data to drive growth and innovation.

Clearly define the responsibilities of all involved parties. Test cell construction requires nuanced expertise and consistent and frequent communication across all levels of stakeholders to align goals and capabilities. An organization attempting to tackle a test cell project with internal resources only often demands additional commitments from engineers, executives, and other stakeholders, resulting in overburdened staff, missteps, delays, or hindered business growth. With large-scale projects, the complexity of the project is typically matched by a widespread, skilled network of teams. This vast ecosystem of knowledge is vital, but it also creates challenges when defining roles and responsibilities. By defining and communicating responsibilities at every stage of the project, integrators, builders, and end users are working in tandem toward a united goal, helping effectively address tasks, mitigate risks, and avoid scope gaps.
Commit to mutual knowledge transfer from start to finish. A vast network of skilled experts with key knowledge is important to bring diverse and informed perspectives to a project. Transferring that knowledge across that network is a fundamental, but easily overlooked step. Beginning with the design stage and understanding the owner’s testing criteria, to the final handover of the facility, transfer of knowledge between integrators and builders to the site engineers and executives must be ongoing and mutual. This starts before a project begins to ensure the expertise and goals of stakeholders are aligned. This requires committed communication at the critical touchpoints of a project across planning, design, building, and ultimately handing over the facility. Knowledge transfer is itself a type of integration, bringing together vital information needed by all team members of a project, informed by their individual expertise, and translated to all crucial stakeholders. This knowledge transfer is also vital to maintain and plan for inevitable modifications and future evolutions.
With a commitment to holistic systems integration throughout the design, build, and handover of a new testing facility, aerospace organizations can ensure that all aspects are built and operated to the highest standards of safety and performance.
ACS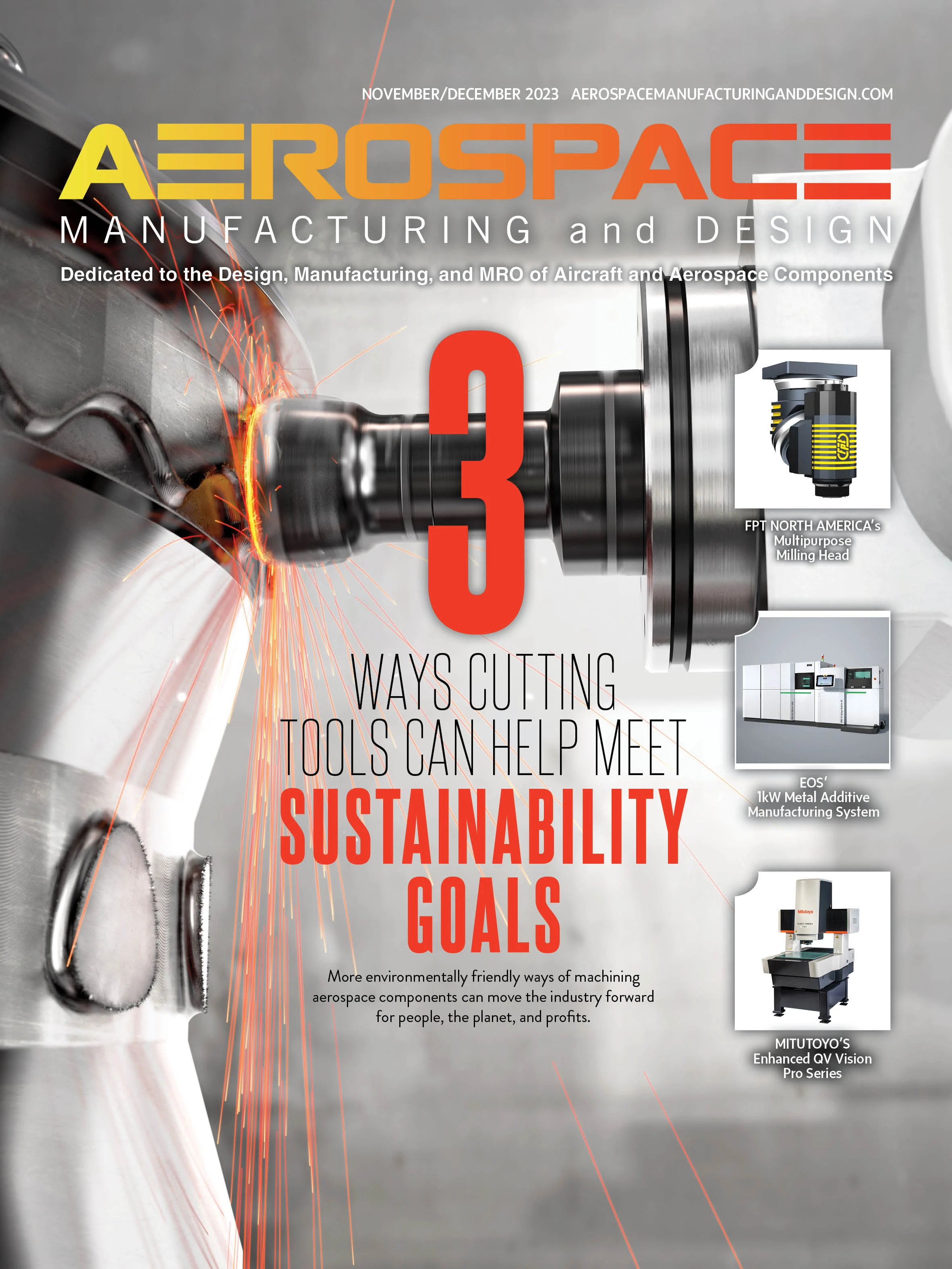
Explore the November December 2023 Issue
Check out more from this issue and find your next story to read.
Latest from Aerospace Manufacturing and Design
- Safran Defense & Space opens US defense HQ
- Two miniature absolute encoders join US Digital’s lineup
- Lockheed Martin completes Orion for Artemis II
- Cylinder CMMs for complex symmetrical workpieces
- University of Oklahoma research fuels UAS development
- Motorized vision measuring system
- Everyone's talking tariffs
- Boom Supersonic to launch Symphony engine testing in Colorado